Mastering Rock Grinder Polishers: A Comprehensive Guide
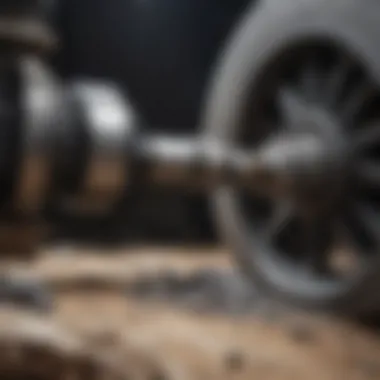
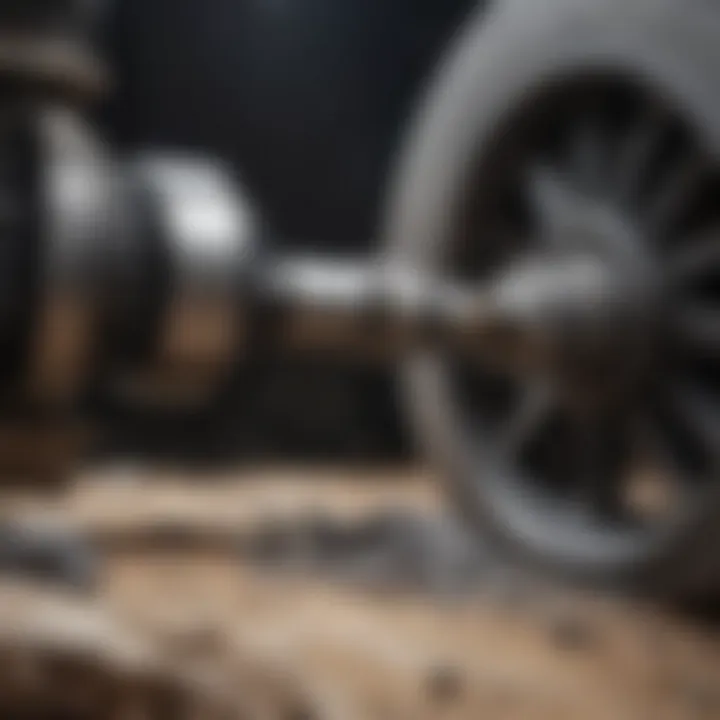
Intro
The exploration of rock grinder polishers delves into equipment that is essential for both enthusiasts and professionals within the fields of geology and mineralogy. These machines serve significant purposes, enabling users to refine and polish stones for aesthetic and analytical purposes. The functionality extends beyond mere polishing; it encompasses intricate precision required to achieve smooth finishes on various types of rocks and minerals.
This article seeks to clarify essential aspects of rock grinder polishers. By understanding the components that comprise these machines, the audience can better appreciate their application in practical settings. We will analyze the importance of these devices, discuss various models available, and provide useful insights into proper usage and maintenance.
An in-depth examination reveals that knowledge about rock grinder polishers enables collectors and enthusiasts to enhance their skills, ensuring that they can effectively utilize the tools to achieve optimal results. From novices to seasoned practitioners, mastering the nuances of these machines is crucial for anyone involved deeply with rocks and minerals.
Topic Overview
Definition of Rock Grinder Polishers
Rock grinder polishers are machines designed specifically to grind and polish rocks. They often have multiple grinding wheels made from various materials that allow users to achieve different finishes on the rocks. These machines operate by removing a small amount of material from the rock's surface, gradually smoothing it out to an aesthetically pleasing finish.
Brief History and Significance
Historically, the process of polishing stones can be traced back to ancient times, where primitive tools were used for similar purposes. As technology evolved, so did the machines used for grinding and polishing rocks. Today, modern rock grinder polishers come in various forms, including models specifically tailored for amateur use and those designed for professional applications. Their significance lies in their ability to improve the overall appearance of rocks, making them suitable for display or for collection purposes.
Identification and Classification
How to Categorize Rock Grinder Polishers
Rock grinder polishers can be categorized based on several criteria. One primary factor is the power source. They can be electric or manual, with electric polishers offering more consistency and efficiency.
Another classification involves the size and weight of the machines. Portable models are ideal for hobbyists who may want to work on smaller projects, while larger models cater to professionals in workshops or commercial settings. Some polishers also specialize in certain types of stones, such as softer minerals versus harder gems.
Tips for Identifying Key Features
When selecting a rock grinder polisher, consider the following key features:
- Motor power: A more powerful motor generally means faster grinding.
- Speed controls: Adjustable speed settings allow greater control over the polishing process.
- Durability: Look for machines made with high-quality materials that withstand prolonged use.
- Versatility: Check if the polisher can accommodate various tool attachments for different types of polishing tasks.
Understanding these features is vital to ensure the correct machine matches the user’s specific needs.
"A well-chosen rock grinder polisher not only enhances the beauty of rocks but also significantly boosts the efficiency of the polishing process."
Prologue to Rock Grinder Polishers
Benefits of Rock Grinder Polishers
Rock grinder polishers serve multiple functions. They not only grind down rough edges but also bring out the internal colors and patterns of the stones. This makes them indispensable for both hobbyists who enjoy lapidary arts and professionals in the gemstone industry. Moreover, proficiency in using these tools can significantly elevate the quality of the finished products, thus adding value.
While the appeal of polished stones is evident, some considerations must be taken into account. The variety of models available means that potential users must assess their requirements thoroughly. Knowing the specific applications, such as crafting jewelry or creating decorative pieces, will influence the choice of the right model.
Overall, gaining a solid understanding of rock grinder polishers is essential for maximizing their potential in both personal and professional endeavors.
Definition and Purpose
Rock grinder polishers are machines specifically designed for shaping and polishing stones. They work by using abrasive materials to gradually wear down the surface of the rock. The primary purpose is to create smooth, shiny surfaces, enhancing the aesthetic quality of the stone.
These machines can vary greatly in design and capability, making it vital for users to select one that suits their specific needs. Some models are made for intense professional use, whereas others are tailored for casual hobbyists.
Historical Context
The history of rock grinder polishers dates back to the early days of lapidary work. Initially, stones were polished by hand using simple abrasives like sand and water. As demand grew, machinery evolved to automate and speed up the process.
In the 20th century, with the rise of modern technology, electric grinder polishers became prominent. The introduction of these machines revolutionized the industry, allowing for greater precision and efficiency. Over time, these devices have been refined, adding features that cater to specific needs and preferences of users. Today, rock grinder polishers are integral tools, bridging traditional craftsmanship with modern techniques.
Types of Rock Grinder Polishers
Understanding the different types of rock grinder polishers is crucial for anyone interested in rock polishing and enhancement. Each type serves a specific audience, ranging from hobbyists to professionals in the field. Choosing the right model can significantly affect the quality of the final product. Inappropriate selection might lead to inefficiencies and potentially compromise the work quality. The major types are benchtop models, portable grinder polishers, and industrial versions.
Benchtop Models
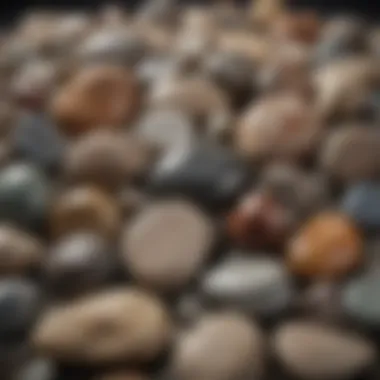
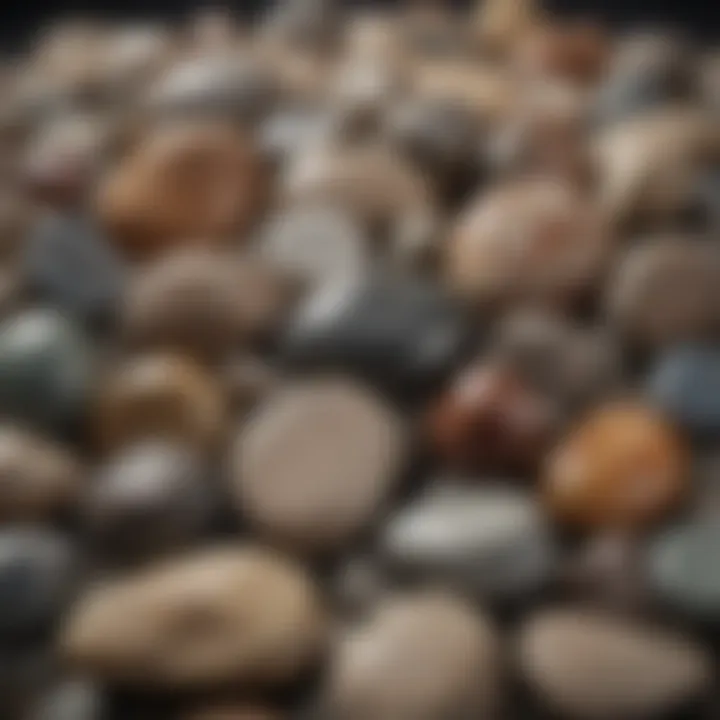
Benchtop models are designed for stability and precision. These machines are ideal for those who need a reliable tool for home use or at a small workshop. The motor power in these devices is usually robust, enabling them to handle various rock sizes. Their design often includes a larger polishing surface that allows for even results.
Benefits of Benchtop Models:
- Consistent performance over long periods.
- Enhanced ability for large rock polishing.
- Modular construction often allows for easier upgrades.
However, they may not fit all spaces, given the larger footprint. If you have limited space or need mobility, alternatives might be more suitable.
Portable Grinder Polishers
Portable grinder polishers offer a different advantage. These machines are lightweight and designed for ease of transport. They cater to those who need to polish rocks on site or wish to work outdoors. Their compact nature does not compromise on power, but they may vary in speed compared to larger models.
Considerations for Portable Grinder Polishers:
- Portable units are often battery-operated or can plug into a standard outlet.
- They provide flexibility for users who travel or need adaptability in their work.
However, users should be aware of potential limitations in drum size and motor strength compared to benchtop units. This selection might be better for smaller projects or quick touch-ups.
Industrial Specifications
For large-scale operations, industrial specifications are essential. These machines are made to withstand heavy use and can handle batch processing of multiple rocks simultaneously. Their motor power and durability make them suitable for professional settings, such as commercial rock polishing businesses.
Features of Industrial Models:
- High throughput capacity.
- Advanced features for precision and automated processes.
- Longer life span, reducing the frequency of replacements.
While these machines might require a substantial initial investment, their return on investment can be considerable with efficient use in a production environment. The choice between other types of polishers ultimately depends on individual needs and the scale of work intended.
Key Features to Consider
When selecting a rock grinder polisher, understanding the key features is critical for optimizing both efficiency and outcomes. The features profoundly influence not only how well a machine performs but also its longevity and versatility. In this section, we will delve into specific elements that are crucial for ensuring that the polisher meets individual needs, preferences, and project requirements.
Motor Power and Speed
The motor power in a rock grinder polisher is a foundational factor. It determines how effectively the machine can handle different types of rock and the speed at which it can grind and polish surfaces. A motor rated between 0.5 to 3 horsepower is common among most units. Higher horsepower often means better performance, especially for tougher materials or larger pieces.
Speed is also vital. Most polishers allow for variable speed settings, enabling users to adjust according to the task. For example, a lower speed is preferred for delicate rocks to avoid damage, while a higher speed can be efficient for tougher stones.
Owners can benefit significantly from machines with consistent motor performance. Look for features that allow for temperature control and overheating protection, as these can help extend the machine’s lifespan.
Drum Size and Capacity
Drum size correlates with the volume and dimensions of material that can be processed at a time. A larger drum can typically hold more rocks, thereby reducing the need for frequent reloads. This can be especially advantageous during professional projects where time is of the essence.
The capacity of the polisher is often determined by both the volume and the type of rock. Models with adjustable drum sizes can offer more versatility. Smaller, portable grinders might have limited capacity but provide excellent mobility.
Keep in mind that a larger drum size also implies the need for more power. Therefore, it’s essential to strike a balance between capacity, power, and the tasks you want to achieve.
Polishing Pads and Accessories
The choice of polishing pads and accessories is just as important as the machine itself. Different pads are suited for varying degrees of coarseness and finishing. For instance, diamond pads work exceptionally well with harder stones, offering durable performance and high-quality finishes.
Another aspect to consider is the ease with which pads can be changed. Some machines have quick-release features that facilitate swift changes, enhancing workflow. Additionally, investment in quality accessories can ensure better results and increased durability.
Accessories such as water cooling systems may also be crucial for maintaining optimal working conditions. Not only do they help in achieving a finer polish, but they also reduce the risk of overheating the rock or the machine itself.
Overall, taking the time to understand and evaluate these key features ensures that the selected rock grinder polisher fits individual work styles and results in splendid polished stones.
Selecting the Right Rock Grinder Polisher
Choosing the appropriate rock grinder polisher is crucial for both effective usage and satisfaction. These machines come with varying features and specifications, influencing their overall performance and suitability for different projects. Understanding specific elements, benefits, and considerations allows hobbyists and professionals alike to make informed decisions for optimal outcomes.
Assessing Personal Needs

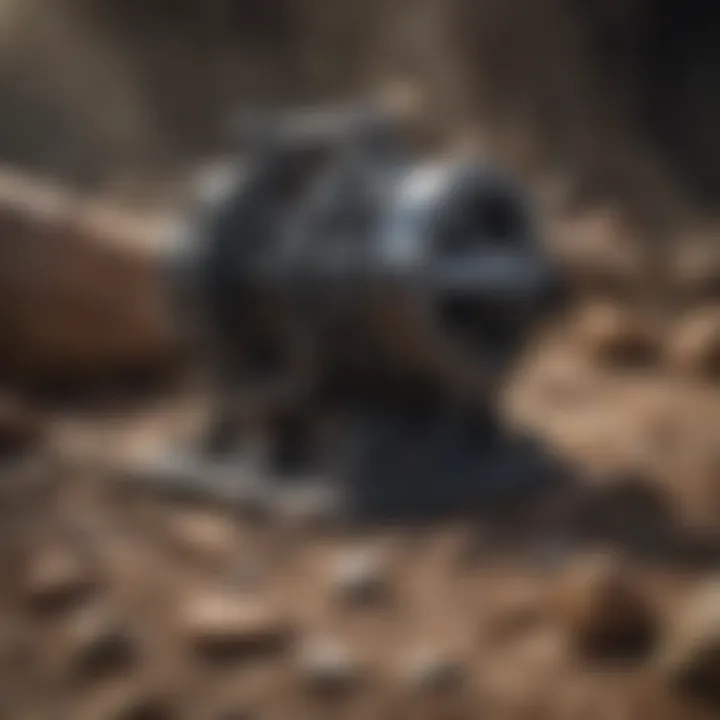
Before procuring a rock grinder polisher, assessing personal needs is pivotal. Individuals might have distinct goals based on their hobbies or work requirements. For example, a hobbyist focused on smoothing small stones may not need the same power as an individual in a commercial setting undertaking larger and tougher rocks. Evaluating the size, type, and hardness of the materials to be worked on guides the selection process. Moreover, consider whether the intended use extends beyond mere polishing. Will the machine need to shape or carve materials as well? Identifying these needs early on can significantly streamline the decision-making process.
Budget Considerations
Budget is always a determining factor when selecting a rock grinder polisher. The machines available vary widely in price, influenced by features, brand reputation, and capabilities. While it may be tempting to opt for the cheapest model, this might compromise quality and durability—leading to further costs over time in repairs or replacements. It's essential to find a balance between affordability and functionality. Setting a realistic budget allows for the exploration of options that meet personal needs while also considering longevity in investment.
Brand Reputation
Brand reputation plays a vital role in the selection of rock grinder polishers. Established brands often provide reliable machines due to their investment in research and development, as well as customer feedback mechanisms. Reading reviews and seeking recommendations from other collectors or professionals can guide potential buyers toward trusted options. Brands like Grindstone and Barranca Diamond have cultivated positive reputations in the field. They are known for their durable and effective machines. Conduct thorough research and take note of after-sales support, warranties, and the overall customer service experience when evaluating brand options.
"Invest in quality to ensure that your tools will last, and you can achieve your desired results without unnecessary complications."
Using Rock Grinder Polishers
Using rock grinder polishers is fundamental for achieving the desired finish and enhancing the aesthetic appeal of rocks. This section elucidates the process involved, emphasizing the importance of each step for rock and fossil collectors. Mastering the techniques of grinding and polishing can significantly affect the outcome, making it essential for both novices and professionals.
Preparation of Rocks
Proper preparation of rocks prior to using a polisher is crucial. It begins with selecting the right rock types to avoid complications during processing. Collectors typically choose soft to medium-hard rocks like agate, quartz, or jasper. These stones provide optimal results in terms of polish and shine.
Before polishing, rocks should be cleaned to remove dirt, dust, or any contaminants. Use water and a soft brush for this task. It's also advisable to inspect each rock for cracks or fissures. Such imperfections can worsen during grinding, possibly leading to breakage or a less than satisfactory finish. Once cleaned, rocks should be dried thoroughly to prevent issues with the grinder.
Grind and Polish Techniques
The grinding and polishing techniques utilized can vary based on the type of rock and desired finish. Start with a coarse grit diamond wheel. This initial step removes rough surfaces and shapes the rock. Ensure a steady hand and consistent pressure, allowing the tool to do the work.
Once rough shaping is complete, gradually progress to finer grits. Switching to finer pads reduces scratches and prepares the rock for final polishing. It is important to follow a logical sequence of grit sizes—this ensures a smoother surface as each grit stage reduces the marks left by the previous one.
Water is often applied during this process. It serves two key purposes: it cools the rock and reduces dust. Using water helps maintain the performance of the polishing pads and prolongs their lifespan. Polishing typically culminates with a very fine grit, which achieves a reflective, glossy finish.
Finishing Steps
Finishing steps are imperative to ensure a high-quality product. After grinding and polishing, a thorough cleaning is necessary. This helps remove any residual grit or dust left from previous stages, which can detract from the rock's appearance.
Following the cleaning, a final polish can be applied. Many opt for a polishing compound that suits the specific rock type. Applying this compound using a soft cloth can enhance the shine. Finally, inspect the finished rock closely under good lighting to ensure uniformity.
"A well-polished rock not only showcases nature's beauty but also reflects the skill of the craftsman."
Safety measures are also significant at this stage. Ensure that all polished rocks are thoroughly dry before they are stored or displayed. Proper maintenance of the grinder and pads will contribute to the longevity of both the tools and the finished products.
Maintenance of Rock Grinder Polishers
Maintaining rock grinder polishers is essential for ensuring optimal performance and longevity of the equipment. Regular upkeep can prevent wear and tear, reduce the risk of malfunction, and ultimately save you money in costly repairs. Both hobbyists and professionals need to be vigilant about maintenance routines, as this can significantly impact the quality of their work. When properly maintained, a rock grinder polisher can enhance efficiency and foster smoother operation, resulting in better polishing outcomes.
Regular Cleaning Protocols
Cleaning the rock grinder polisher after each use is crucial. Dust, debris, and stone particles can accumulate on the machine, hindering its performance. To maintain it, follow these basic cleaning steps:
- Disconnect the Power: Always unplug the machine before cleaning to avoid accidents.
- Use Compressed Air: Blow out any particles stuck in the motor housing or ports.
- Wipe Down Surfaces: Use a damp cloth to clean the exterior and any removable components. Avoid abrasive materials that could scratch the surfaces.
- Check the Polishing Pads: Inspect pads for debris and signs of wear. Clean them according to manufacturer instructions.
- Store Properly: Ensure the polisher is stored in a dry environment to prevent rust or moisture damage.
Replacing Parts and Accessories
Over time, parts of a rock grinder polisher will wear out and require replacement. Recognizing when to replace components is important to ensure effective functioning. Here are key aspects to consider:
- Identify Worn Parts: Regularly inspect components such as motors, polishing pads, and gears for any signs of wear or damage.
- Source Quality Replacements: Always opt for parts from reputable brands, like T SCM or Grizzly Industrial, to ensure compatibility and durability.
- Follow Replacement Guidelines: Refer to the user manual for detailed instructions on replacing parts. Keeping a set of common spare parts handy can prevent downtime.
- Schedule Routine Checks: Implement a routine check-up every few months to preemptively identify any accessory needing replacement.
Troubleshooting Common Issues
Even a well-maintained machine can encounter problems. Understanding basic troubleshooting can help resolve issues quickly. Common problems include:
- Machine Won’t Start: Ensure the power cord is plugged in and check for any blown fuses.
- Excessive Vibration: This may indicate misalignment of parts. Stop and reassemble the machine properly.
- Insufficient Polishing: If results are lacking, verify you are using the right polishing pad for your material and that it is in good condition.
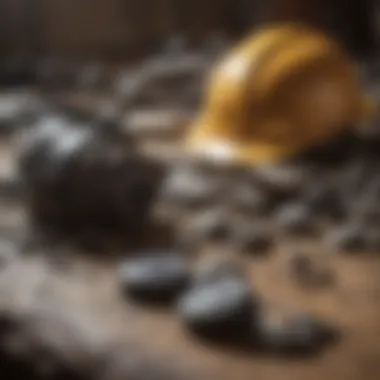
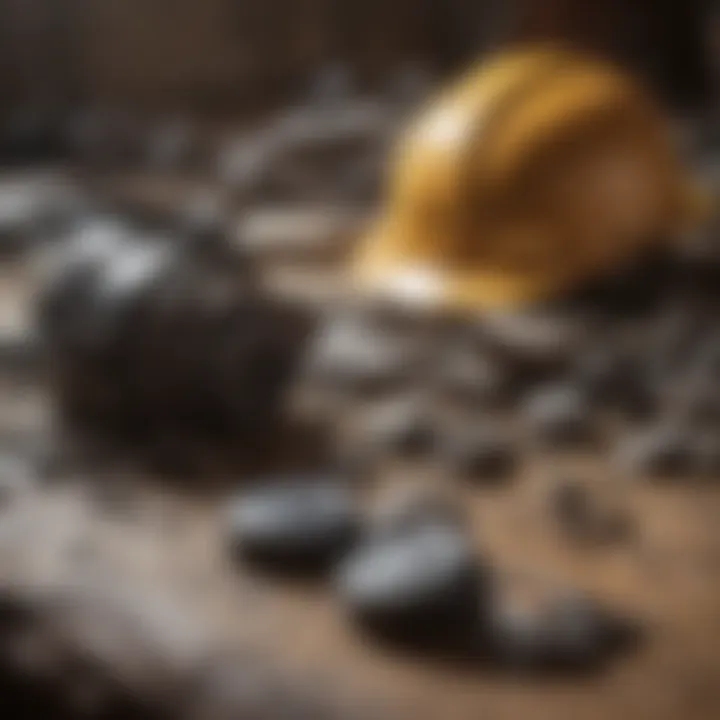
Regular maintenance, attentive cleaning, timely parts replacement, and effective troubleshooting are all vital for the functionality and reliability of rock grinder polishers. Engaging in these practices will not only enhance the performance of your equipment but also improve the quality of your polishing projects.
Safety Considerations
Safety is a critical aspect when using rock grinder polishers. With the potential for hazardous situations, understanding the safety guidelines can significantly reduce risks associated with their use. Properly addressing these considerations can lead to safer operations and enhance the overall experience of working with rock grinder polishers.
Protective Gear Requirements
When operating rock grinder polishers, one must prioritize personal safety through appropriate protective gear. Key elements of protective gear include:
- Safety Goggles: Protect eyes from flying debris or dust, ensuring clear vision during the polishing process.
- Dust Masks: These help filter out harmful particles and dust generated during grinding. A good-quality mask can prevent respiratory issues over time.
- Ear Protection: Prolonged exposure to the high noise levels from grinders can lead to hearing loss. Using earplugs or earmuffs is essential in noisy environments.
- Gloves: Heavy-duty gloves protect against cuts and abrasions. They also ensure a firm grip on the tools during operation.
- Apron or Protective Clothing: Wearing durable clothing or aprons prevents abrasions from flying materials and keeps the operator clean.
Having the right protective gear is not just a recommendation; it sets a strong foundation for a safe working environment.
Operational Safety Guidelines
In addition to wearing personal protective equipment, following operational safety guidelines is equally important. Here are several core practices:
- Read the Manual: Always consult the user manual before operating any machine. Understanding the manufacturer's instructions is vital for safe usage.
- Check Equipment Before Use: Regular inspections of the grinding machinery can identify potential issues. Ensure that parts are secure and functioning properly before starting.
- Work in a Well-Ventilated Area: Proper airflow helps reduce the inhalation of harmful particles. Keeping the workspace well-ventilated is crucial.
- Use Tools Correctly: Familiarize oneself with the correct techniques for grinding and polishing. Misuse can lead to accidents or damaging the equipment.
- Avoid Loose Clothing and Accessories: Loose attire may get caught in machines, leading to serious injuries. Tying back hair and avoiding long sleeves is advisable.
"Taking the time to implement safety considerations not only protects the user but enhances productivity by minimizing accidents."
By adhering to these guidelines, rock grinder polisher users can significantly reduce the likelihood of accidents and ensure a smoother operational process.
Applications of Rock Grinder Polishers
Rock grinder polishers serve multiple significant purposes, making them essential tools in both casual and professional settings. They enhance the aesthetics of various rocks and minerals, thus elevating their intrinsic value. Properly polished stones and gems catch the eye and are more appealing in a market where visual presentation often dictates sales.
The ability to refine and polish rocks is particularly important for collectors and artisans alike. Hobbyists utilize these machines to achieve a specific finish or texture, while professionals may often demand precise standards for commercial sale or exhibition. Each application requires understanding the nuances and capabilities of the equipment.
Hobbyist Use Cases
For enthusiasts, the joy of rock polishing is more than just a task; it is an art form. Hobbyists engage in polishing rocks as a creative outlet, finding satisfaction in transforming rough stones into beautiful specimens. Whether someone is working on agates, jaspers, or quartz, a rock grinder polisher can dramatically alter the appearance of each piece.
Some common use cases among hobbyists include:
- Creating Jewelry: Many hobbyists embark on making one-of-a-kind jewelry pieces. Polished stones serve as striking pendants or beads, enhancing the overall aesthetic appeal.
- Decorative Display: Finished polished stones can become centerpieces in households or offices, showcasing the collector's taste and expertise.
- Educational Purposes: For enthusiasts teaching others about geology or lapidary arts, polished rocks can serve as tangible examples of geological processes and techniques.
Professional Applications
In professional settings, rock grinder polishers are often indispensable. Businesses in fields such as gemology and geology rely on these tools for their functionality. Here are a few professional applications:
- Gemstone Preparation: Gemologists require precision tools to prepare stones for cutting and setting. Using a rock grinder polisher helps achieve the desired facets and shine.
- Research and Exhibitions: Museums often exhibit polished specimens. These polished pieces allow the viewer to appreciate the beauty of geological formations while also providing critical educational insights.
- Manufacturing and Retail: In the commercial market, polished rocks and gems are often sold at higher prices compared to their unrefined counterparts. Companies can expand their product lines by offering customized polishing services.
Utilizing rock grinder polishers caters to a diverse audience, enriching both personal collections and commercial offerings. Their role in enhancing the beauty and value of geological specimens is undeniable.
By carefully understanding and assessing the applications of rock grinder polishers, users can better leverage these tools to maximize their utility, whether for personal enjoyment or professional advancement.
Future of Rock Grinder Polishers
The future of rock grinder polishers stands as a pivotal topic in the realm of rock and fossil collection. As enthusiasts and professionals seek to enhance their capabilities, innovation in this space is crucial. With advancements in technology, users can expect more efficient machines that deliver superior results. Echoing this trend, the integration of user-friendly features will make these tools accessible to a broader audience, thus expanding the community of collectors and artisans.
Technological Innovations
Technological innovations are greantly influencing the landscape of rock grinder polishers. The emergence of smart technologies, including AI-driven features, is transforming how users interact with their equipment. For instance, sensors can now provide real-time feedback on grinding pressure, ensuring optimal performance. This feature helps minimize surface damage while polishing, leading to better finishes.
Moreover, enhanced motor designs contribute to improved energy efficiency. New models are being developed with brushless motors that offer longer life-spans, reducing costs related to replacements.
Another area of innovation is the development of advanced polishing pads. These pads now use specialized materials that provide finer finishes quicker than traditional versions. As materials science progresses, the longevity and effectiveness of these components will undoubtedly improve as well.
Sustainability in Material Processing
Sustainability is an essential consideration in the future development of rock grinder polishers. The growing awareness of environmental issues is prompting manufacturers to rethink their production methods. Eco-friendly materials are gaining traction in the manufacturing of grinder components, which can reduce the overall environmental footprint.
In addition, the industry is moving towards methods that allow for the recycling of materials. For example, using biodegradable lubricants during the grinding process can minimize harmful waste.
Furthermore, energy-conscious designs are increasingly important. Manufacturers are exploring ways to decrease energy consumption during operation.
As sustainability becomes a priority, those seeking to invest in rock grinder polishers will favor brands that emphasize eco-friendly practices, thus influencing market trends.