Mastering the Craft of Precious Stone Cutting Machines
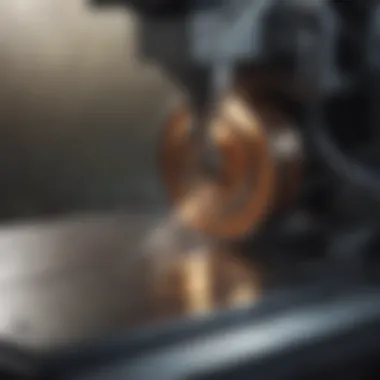
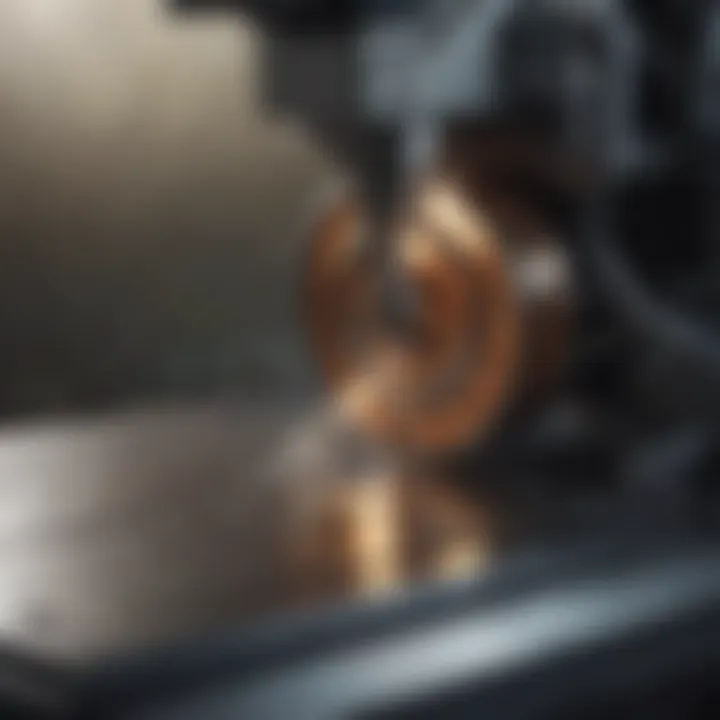
Intro
In the world of gemstones, the quest for beauty and precision leads us to the fascinating theme of stone cutting machines. Often overlooked, these machines serve as the backbone of the gemstone industry. Their remarkable capabilities enable artisans to transform rough stones into dazzling pieces of art. Understanding their intricacies allows both collectors and professionals to appreciate the craft behind each gem.
The array of advanced technologies and precision engineering found in today’s cutting machines has reshaped the way these natural wonders are processed. As a rock collector or gemstone enthusiast, it’s crucial to comprehend how these tools not only enhance the aesthetic appeal of stones but also significantly impact their value.
In this article, we will explore the operational principles of precious stone cutting machines, highlight the different types available, and delve into the maintenance practices that ensure their longevity. We'll also look at the future trends on the horizon, providing you with a well-rounded perspective on this vital aspect of the gemstone industry.
Understanding Precious Stone Cutting Machines
Precious stone cutting machines play a significant role in the world of gemology, transforming rough stones into dazzling jewels that capture light and admiration. These machines aren't just tools; they're the bridge between raw earth materials and the art of jewelry making. Understanding the nuances of these machines is paramount not only for professionals in the field but also for enthusiasts who appreciate the craftsmanship involved in gemstone processing.
Historical Context and Evolution
The journey of gem cutting began centuries ago when artisans utilized simple hand tools to shape the stones. These primitive methods evolved over time into the sophisticated machines we see today. In ancient civilizations, such as the Egyptians and Greeks, stones were carved by hand, an arduous process that required immense skill and patience. Over the decades, technological advancements introduced a variety of tools and machines designed to enhance precision.
For instance, the introduction of electricity in the 19th century led to the development of powered saws, revolutionizing how stones were cut. Furthermore, the 20th century witnessed the invention of CNC (Computer Numerical Control) machines and laser cutters, elevating the art of stone cutting to an entirely new level. The historical context provides insight into how far the gem cutting industry has come and underscores the importance of these machines in modern practices.
Significance in Gemstone Processing
The significance of precious stone cutting machines extends beyond mere functionality; they redefine the aesthetics and value of gemstones. Employing a cutting machine enhances accuracy, ensuring that every facet of a gem is cut with precision. This precision is crucial for maximising a stone's brilliance and fire. In fact, even the smallest misstep during cutting can result in considerable losses, not just in material but in the final product’s visual appeal.
Utilizing these machines means less time spent on manual work and more consistent results. For gem dealers and collectors, this consistency is vital. It allows them to present their inventory with pride, knowing that every piece has been crafted with the utmost care.
Moreover, understanding these machines opens up a dialogue about the balance between artistry and technology. While machines can perform tasks with incredible accuracy, the finesse of human touch still plays an essential role in nuanced design choices.
As the industry progresses, recognizing the significance of cutting machines not only informs buyers and sellers but also enriches the culture surrounding gemstone appreciation. Understanding how these machines operate and their impact on the final product broadens one's perspective on the value of gemstones.
"In the world of gemstones, precision cutting is akin to a painter’s brushstroke; every detail matters."
In summary, grasping the essentials of precious stone cutting machines enlightens both the professional and the casual observer about the complexities of gemstone processing. It serves as a foundation for further exploration into the types, operational principles, and ultimately, the artistry inherent in gem cutting.
Types of Precious Stone Cutting Machines
Understanding the various types of precious stone cutting machines is crucial for rock and fossil collectors, jewelers, and those keen on gem processing. Each machine offers distinct benefits and is designed for specific tasks, affecting both the efficiency of cutting and the quality of the final product. The choice between different cutting machines often hinges on the desired precision, cost, and complexity of the cutting tasks at hand.
Manual vs. Automatic Machines
Manual cutting machines put the power in the hands of the operator. There's a certain artistry involved in using a manual machine, where the skill of the cutter becomes a pivotal part of the stone transformation process. Operators have full control over the speed, pressure, and angle of cuts, which can result in unique styles and finishes not achievable with more automated techniques. For example, a skilled cutter might use a simple diamond saw for intricate designs, taking time to perfect each cut much like an artist adding details to a painting.
On the flip side, automatic machines incorporate computer technology to ensure consistency and precision. These machines can repeatedly produce cut stones that meet exact specifications without substantial human intervention. For collectors who prioritize uniformity and efficiency, these machines can be a game changer. Thoughtfully programmed, automatic machines can churn out perfectly faceted gemstones, ideal for modern jewelry applications. However, it might lack the personal touch of manual cutting, sometimes leading to pieces that feel more mechanical than crafted.
CNC Machines
Computer Numerical Control (CNC) machines revolutionized gem processing. They bring together the precision of computer algorithms with the intricacies of stone cutting. By utilizing a digitized blueprint of the desired cut, CNC machines can execute complex designs with unparalleled accuracy. This transformation allows for the creation of unique facets that enhance the stone’s brilliance and appeal.
CNC machines are often seen in larger operations due to their costs and space requirements. However, the upfront investment pays dividends in terms of generating high-quality, precise cuts that improve the stone’s resale value. For enthusiasts looking to hone their craft, learning to operate a CNC machine can greatly expand their capabilities. Besides, their versatility means that these machines can work with a range of materials beyond just gemstones, making them a worthy addition to any serious collector’s toolkit.
Laser Cutting Technology
Laser cutting technology is making waves in the gemstone industry, offering a cutting-edge solution to intricate designs. This method utilizes focused light beams to cut or engrave stones, resulting in remarkably clean edges and precise shapes. The speed and accuracy of laser cutting are astonishing, allowing for more complex patterns than traditional methods ever could. For instance, delicate engravings or unique motifs can be swiftly executed without the risk of chipping or fracturing that might accompany blade cutting.
With laser technology, the potential for creativity is virtually limitless. Jewelers can create patterns that are not only beautiful but also replicate efficiently. From the production standpoint, the ability to minimize waste while maximizing production volume also makes laser cutting an attractive option. However, the investment in such technology can be significant, often reserved for larger businesses unless smaller units are available.
In summary, the types of precious stone cutting machines available today—a mix of manual, automatic, CNC, and laser technologies—each have unique strengths. Collectors and creators alike must weigh the benefits and drawbacks of each to find the right fit for their needs. As the industry advances, staying informed about these technologies becomes vital for those who wish to maintain a competitive edge in gem cutting.
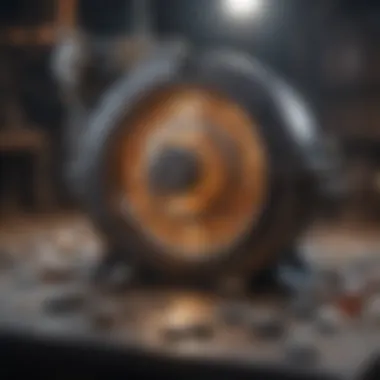
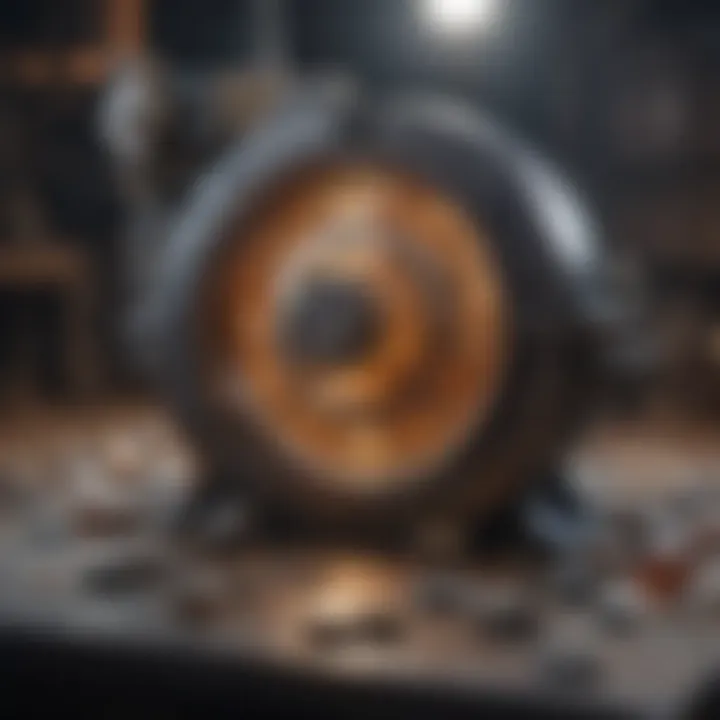
Key Features of Stone Cutting Machines
In the world of gem and mineral processing, the quality of the stone cutting machine plays a crucial role. The key features of these machines can define their efficiency, precision, and overall effectiveness. Understanding these specific elements not only helps in selecting the right machine for a given task but also significantly influences the final product produced. The heart of stone cutting machines is to refine gemstones, enhancing their natural beauty while maintaining integrity. Therefore, evaluating features like precision, speed, and versatility becomes paramount for any serious gem collector or enthusiast.
Precision and Accuracy
When it comes to cutting precious stones, precision is not merely a luxury; it is a necessity. Cutting machines are designed to achieve extremely narrow tolerances and high levels of accuracy. This precision is especially important for stones like diamonds and sapphires, where even a slight miscalculation can affect the stone’s appearance and value. Advanced cutting machines often employ computer numerical control (CNC) technology. This allows for intricate designs and shapes to be cut with remarkable exactness.
"Precision in stone cutting ensures that every facet reflects light to its fullest potential, enhancing the gem's brilliance."
The exactness of cuts dictates not just the aesthetics but also how the stone refracts light. Layers of carefully arranged facets can turn an ordinary piece into something extraordinary. Ultimately, better precision translates to better quality gems, appealing to both collectors and the market.
Speed and Efficiency
In any industry, the balance between speed and quality is always a tightrope walk. Stone cutting machines have evolved significantly, making advances in both speed and efficiency without compromising quality. Notably, automatic machines can significantly reduce the time it takes to produce each stone. While traditional cutting might require hundreds of hours to produce a single quality gem, modern machines can do this in a fraction of the time, thanks to quicker setups and automated processes.
Additionally, the efficiency of cutting machines minimizes the waste produced during the cutting process. When machines are faster and more efficient, fewer raw materials are wasted, which can translate to lower costs and a more sustainable practice in the gemstone industry. Thus, not only do collectors benefit from higher quality stones but also from more affordable prices, making efficiency a critical feature in modern machines.
Versatility and Adaptability
The spectrum of gemstones available today is vast, each requiring different cutting techniques and approaches. Therefore, versatility is a key characteristic that modern stone cutting machines must possess. Being able to adapt to various shapes, sizes, and hardness levels is crucial for any machine that aims to serve multiple facets of the gemstone industry.
Many machines now come with interchangeable heads or blades, allowing for various styles of cuts, from simple to complex designs, and catering to different types of gemstones. This adaptability ensures that professionals can switch tasks seamlessly without needing entirely new equipment each time.
This feature is paramount for businesses that handle diverse inventories, enabling them to meet market demands more effectively and cultivate a wider range of clientele. Plus, the need for adaptability is ever-growing as new technologies emerge and as the tastes in gemstones shift in the marketplace.
Operational Principles
To truly appreciate the craftsmanship involved in precious stone cutting machines, one must grasp the operational principles that underpin their function. These principles serve as the backbone of the cutting process, ensuring that precision and quality are maintained at every stage. Understanding these elements not only educates enthusiasts and professionals but also emphasizes the technological sophistication ingrained in modern machinery.
Understanding Blade Types
The type of blade used in a stone cutting machine plays a pivotal role in determining the quality of the cut. Blades can vary significantly based on material, design, and intended application. Generally, two main types of blades are widely used: diamond blades and abrasive blades.
- Diamond blades are the gold standard when it comes to cutting precision stones like diamonds, sapphires, or emeralds. Their composition allows for cleaner cuts, which minimizes damage to the stone.
- Abrasive blades, on the other hand, are typically made from a mixture of softer materials and are better suited for less precious stones, where high precision might not be as critical.
Each blade type has its pros and cons, and selecting the right one is crucial for achieving the desired outcome. An operator’s knowledge of these blade types helps in both enhancing aesthetics and increasing the efficiency of the cutting process.
Cooling and Lubrication Methods
When cutting stones, heat generation is an ever-present issue. Without proper cooling and lubrication, the blades and the stones themselves can suffer significant damage. Employing effective cooling methods is therefore essential for extending the life of the equipment and enhancing the quality of the cut.
- Water Cooling: The most common technique involves using water to cool down the blade during the cutting process. It helps remove debris and can significantly reduce the temperature of the blade, which in turn protects both the blade and the gemstone from thermal shock.
- Oil-Based Lubricants: In some cases, especially during heavier machining tasks, oil-based lubricants may be preferred. These provide a slick surface that reduces friction and keeps the blade from dulling quickly.
A well-thought-out cooling system not only protects the machine but also aids in achieving more polished cuts. Operators must be diligent in monitoring the levels of coolant or lubricant throughout the cutting process.
User Interface and Controls
In the modern landscape of gemstone cutting, user interface design is just as important as the machinery itself. A user-friendly interface can greatly enhance operational efficiency and minimize the risk of errors. Most contemporary stone cutting machines come equipped with digital controls that offer a variety of features:
- Touchscreens: Many machines now utilize intuitive touchscreens that allow operators to input precise measurements and cutting parameters quickly.
- Programmable Settings: Advanced machines come with programmable cutting patterns, enabling users to replicate complex designs reliably.
- Diagnostic Displays: These features provide real-time data about the machine's performance, alerting the operator to any irregularities that may need attention.
The clarity and responsiveness of these controls can directly affect the outcome of a cut, emphasizing why careful attention to the user interface can be as critical as the mechanics of the machine itself.
Understanding the operational principles behind precious stone cutting machines is essential for anyone in the gemstone industry. The efficiency, accuracy, and quality of the final product hinge on these underlying elements.
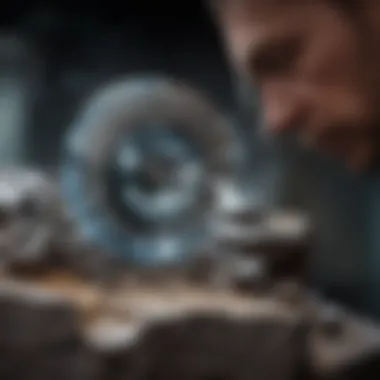
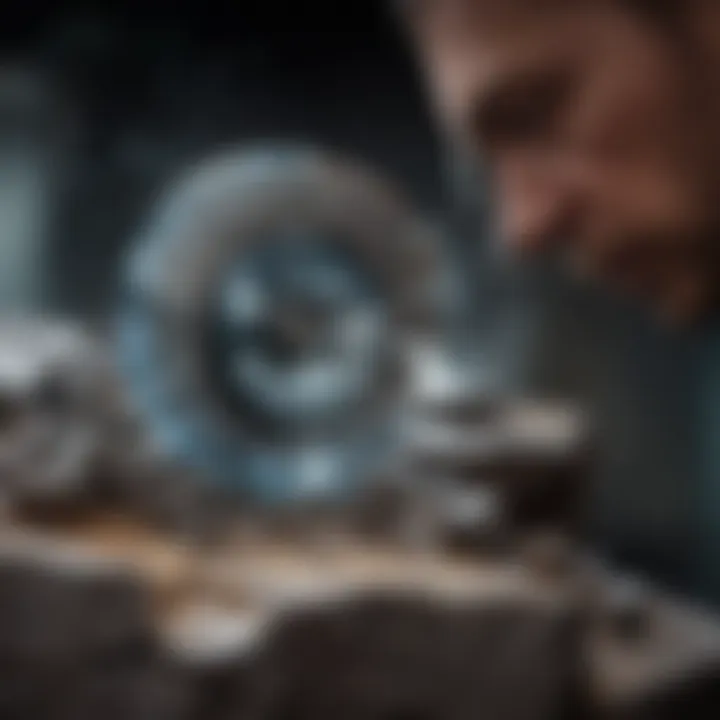
Impact of Cutting Machines on Gem Quality
The quality of precious stones is deeply influenced by the cutting processes employed during their transformation. Here, we delve into how cutting machines impact the overall quality of gemstones, a focal point that shapes the industry's standards and practices.
Enhancing Aesthetics and Brilliance
Precision in cutting translates directly to the aesthetics of a stone. Cutting machines are equipped with technological advancements that allow for consistent, intricate designs that uplift a gem's natural beauty. When gem cutters use these machines, they can manipulate light effectively, maximizing the stone's brilliance—an essential attribute highly sought after in both commercial and collector markets.
For example, a well-cut diamond can reflect light in a way that enhances its sparkle, resulting in a visually striking piece. With the help of CNC and laser cutting technology, cutters can achieve angles and facets that are beyond what manual methods may allow. Such advancements not only improve visual appeal but also can increase a gem’s resale value.
Minimizing Waste
Another practical benefit of utilizing cutting machines is their ability to minimize waste during the cutting process. Traditionally, manual cutting could lead to significant waste. In contrast, modern machines optimize every cut, extracting the most value from the raw materials. This efficiency is paramount in maximizing resource use, which is especially critical in a market where fine stones can be scarce and expensive.
In using automated systems, a higher yield of useable gemstones can be achieved. By calibrating the machines to ensure the best placement and cutting techniques, gem cutters can expect to see reduction in waste and therefore more profitability in their final products. Precise cutting may also mean less risk of damaging fragile stones, which is an important consideration for valuable pieces.
Preserving Gem Integrity
The integrity of a gemstone is crucial in maintaining its inherent value and physical properties. Cutting machines contribute significantly here, as they allow for gentle yet effective cutting methods that preserve the key attributes of the stone. High-quality cutting machines ensure that the pressure exerted during the cutting process does not compromise the stone’s structure, which can sometimes lead to chipping or fracturing.
When gems are cut with care—using advanced machines designed for specific hardness levels and properties—the result is not only a superbly crafted item but also one that retains its durability over time. This preservation is vital for collectors and investors who are often keen to ensure that their pieces stand the test of time.
"The merging of technology and artisan skill in gemstone cutting machines marks a revolution in how we perceive and value gemstones."
Maintenance of Precious Stone Cutting Machines
Maintaining precious stone cutting machines is not just a matter of keeping the equipment running; it plays a crucial role in extending the life of the machines, ensuring high-quality cuts, and minimizing operational disruptions. Regular maintenance helps to safeguard the precision and accuracy that these tools are known for. When collectors, hobbyists, or professionals invest in these machines, they rely on their performance for success. A well-maintained machine not only enhances output but also provides peace of mind.
Routine Checks and Balances
Routine checks form the backbone of proper maintenance. Just as one wouldn't drive a car without checking the oil, operators should frequently inspect their cutting equipment. This includes looking for wear and tear on blades, checking wiring, and ensuring that the machinery is clean and free from debris.
- Blade Inspection: This is paramount. Dull or damaged blades can lead to poor quality cuts and even shatter precious stones. Regular sharpening or replacement could save time and frustration.
- Lubrication: Many cutting machines require proper lubrication for moving parts. Neglecting this can cause parts to wear out faster, leading to costly repairs.
- Cooling Systems: If the machine uses coolant, it's essential to regularly check and refill as needed. Coolants play a major role in maintaining proper temperatures during cutting operations.
Incorporating a routine schedule for these checks helps in identifying potential issues before they escalate, saving time and money.
Common Issues and Troubleshooting
Even the best machines can run into problems. This section covers some common issues and how to tackle them effectively. If an operator is knowledgeable about these hurdles, they can often resolve them without necessitating professional assistance.
- Uneven Cuts: Often an indicator that the blade is dull or misaligned. Rerouting the machine's calibration can often restore precision.
- Overheating: This can cause significant damage, leading to operational delays. The first step is to check if coolant levels are sufficient and that the cooling system is functioning optimally.
- Vibration: Excessive vibration can indicate mechanical faults, often due to wear on bearings or incorrect settings. Re-evaluating the setup or reaching for professional evaluation may be necessary.
"Regular maintenance is the silent guardian of gemstone quality."
Taking the time to familiarize oneself with these common issues can significantly empower the operator.
Upgrading and Retrofitting
As technology advances, older machines may require upgrades or retrofitting to stay competitive. This is especially vital in a field where precision cutting can greatly affect the value of gemstones. Evaluating current capabilities can point to areas needing enhancement.
- Software Upgrades: Many modern machines come equipped with the latest software that improves cutting patterns and speeds. Keeping software updated ensures operators leverage the best available technology.
- Hardware Modifications: Adding new components, like advanced cooling systems or powerful motors, can enhance performance without the need for a complete machine replacement.
- Training and Skill Enhancement: With upgrades often come new features. Investing time in training operators can maximize the output from these enhancements.
By considering these upgrades, operators can keep their machines at the forefront of technology and maximize their investment.
Environmental Considerations
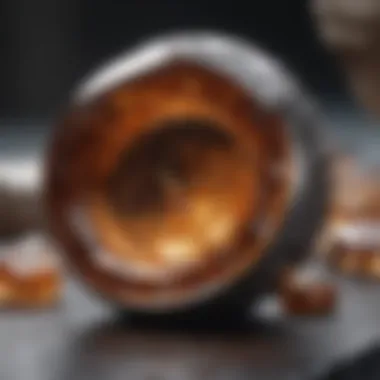
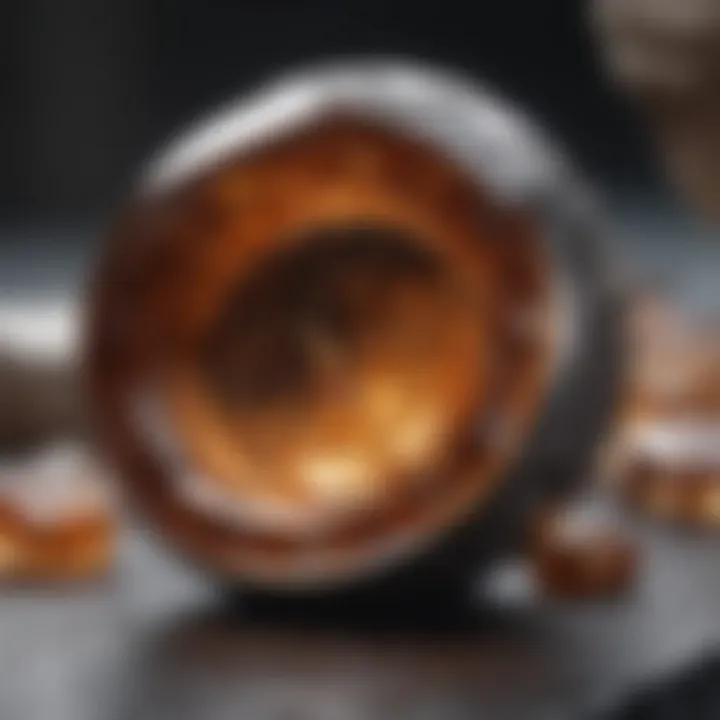
The gemstone industry has been undergoing a significant transformation in recent years, especially concerning environmental considerations. As more collectors and businesses recognize their ecological responsibilities, it's essential to delve into how precious stone cutting machines can align with sustainable practices. By prioritizing these considerations, the industry not only addresses the direct environmental impacts of stone processing but also paves the way for a more conscientious production model that benefits both the planet and its inhabitants.
Sustainable Practices in Cutting
Sustainability in precious stone cutting extends far beyond the mere act of cutting itself. Here are some notable sustainable practices that are being integrated into the operations:
- Water Conservation: Many cutting operations rely heavily on water for cooling and dust suppression. Advanced systems that recycle water minimize waste and reduce the consumption of this precious resource.
- Eco-friendly Blades: Utilizing blades made from more sustainable materials not only enhances cutting efficiency but also reduces harmful emissions. These innovations are delivering better results with less environmental harm.
- Energy Efficiency: The push for energy-efficient machines is stronger than ever. Operations investing in equipment with lower energy consumption reduce their carbon footprint. Modern CNC and laser cutting machines often have this feature, proving further beneficial for the planet.
These sustainable practices not only demonstrate a commitment to environmental health but also improve operational costs over time, making them an attractive option for businesses looking to balance profit with responsibility.
Minimizing Environmental Impact
The impact of gemstone cutting on the environment cannot be overlooked, particularly in terms of waste generation and resource depletion. To tackle these issues, several strategies have gained traction:
- Reduction of Waste: Improving cutting techniques to optimize the use of raw materials is key. Techniques like precision-cutting yield fewer scraps, thus decreasing waste significantly.
- Proper Disposal: Establishing protocols for waste disposal ensures that any leftover materials are dealt with responsibly. Recycling and recovery of stone scraps for other uses, such as gravel or decorative landscaping elements, underscores effective waste management.
- Sustainable Sourcing: As gemstone cutting machines evolve, the materials used for cutting often reflect the same environmental consciousness. Selecting stones sourced from environmentally regulated mines further minimizes the negative ecological effects linked to mineral extraction.
"A commitment to sustainable practices is not just good for the environment; it's becoming a prerequisite for businesses in the gemstone industry to thrive in a conscientious market."
By integrating these considerations into the core of gemstone processing, the industry reaffirms its commitment not just to profitability but to the stewardship of the earth. It's a clear takeaway for collectors and industry players alike: making mindful choices today ensures a viable future for both the gemological and environmental landscapes.
Future Trends in Precious Stone Cutting
The sphere of precious stone cutting is constantly evolving, shaped by technological advancements and shifting market dynamics. Understanding these trends is crucial for collectors and professionals alike, as the tools and practices adopted today set the foundation for quality and innovation in the future. Not only do these trends indicate how the industry is adapting, but they also offer insights into enhancing precision, efficiency, and sustainability—all key factors in gemstone processing.
Technological Advancements
In recent years, technological innovations have spearheaded a transformation in precious stone cutting. Automated machines are now equipped with advanced software and artificial intelligence, enabling them to deliver high precision in cuts that were once unattainable by manual means. For instance, the integration of machine learning algorithms allows these machines to analyze various stone types and adjust cutting parameters dynamically.
Moreover, the rise of 5-axis CNC cutting machines has introduced unprecedented versatility. These machines can handle complex designs with multiple angles, ensuring that every facet of a gemstone is artfully crafted. This capability not only increases cutting speed but also enhances the overall aesthetic appeal of stones—impressive results, especially in premium gemstones.
"The advent of these technologies does not just accelerate the cutting process, it heightens the artistry involved, merging craftsmanship with innovation."
Additionally, improvements in laser cutting technology have made it possible to achieve remarkable detail in intricate designs. Lasers offer greater control over depth and angle, allowing gem cutters to create patterns and finishes that elevate the luxury of the stone. As these technological advancements continue to unfold, we can anticipate an even broader range of creative possibilities for artisans in the industry.
Market Trends and Demands
The global landscape of precious stone demand is undergoing significant changes. Collectors are becoming increasingly discerning, often seeking stones that are not just valuable, but also reflect ethical sourcing and environmentally friendly practices. Consequently, manufacturers are responding by adopting sustainable methods in their cutting processes.
Furthermore, the rise of online marketplaces has changed how gems are distributed and purchased. This shift calls for high-quality visuals and certifications that reassure buyers of the stones' authenticity. With an informed customer base now firmly established, companies are compelled to improve transparency about their sourcing, cutting processes, and gem quality.
The trend towards customization is also gaining traction. Buyers are keen on unique pieces tailored to their preferences, pushing cutting machine manufacturers to facilitate bespoke solutions. Custom cuts require machines to be adaptable, thus enhancing the appeal of technologically advanced stone cutting equipment.
In summary, the future of precious stone cutting is being shaped by technological breakthroughs and evolving market preferences. By keeping a finger on the pulse of these developments, those in the industry can not only stay competitive but also contribute positively to the gem trade as a whole.
Ending
The exploration of precious stone cutting machines reveals their significant role in the gemstone industry. One might say, these machines are the unsung heroes behind the stunning gems that adorn jewelry and collectable pieces alike. Their precision and operational excellence not only define the quality of the cut but also reflect the artistry involved in transforming raw minerals into sparkling treasures.
Recap of Key Insights
Throughout this article, it became clear that the evolution of these machines has burgeoned, from rudimentary tools to highly sophisticated technology. The journey of understanding the various types of machines - from manual to CNC and laser technologies - offered a glimpse into the unique benefits each type brings to the table. With a strong emphasis on precision, durability, and efficiency, precious stone cutting machines enhance the aesthetic appeal of gems while minimizing waste.
Moreover, environmental consciousness has gained traction in recent years; thus, implementing sustainable practices is no longer optional but a necessity for respecting our planet. The future trends are equally riveting, with promising advancements on the horizon that could revolutionize how stones are processed and handled.
Final Thoughts on the Industry
As we wrap our heads around the intricacies of precious stone cutting machines, it is essential to recognize that they are indispensable to the industry. Cutting high-quality gemstones demands not just an investment in these machines, but also an understanding of their capabilities and maintenance. Enthusiasts and collectors should not only admire the end products but also appreciate the technology and precision that brought them to life.
In essence, this article serves to highlight the importance of adapting to the latest technological trends and embracing a sustainable approach in stone cutting operations. By staying informed and involved, those within the jewel and gem community can better appreciate and participate in this art form, ensuring the industry's longevity and continued innovation.
Every gemstone tells a story, and cutting machines are the authors of that narrative.