Essential Elements for Mastering Jewelry Soldering
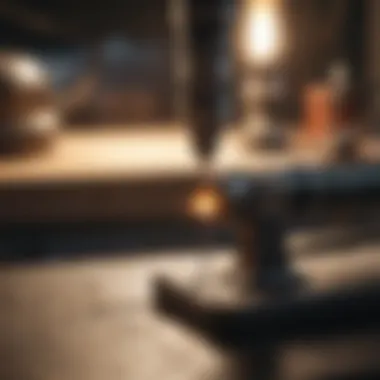
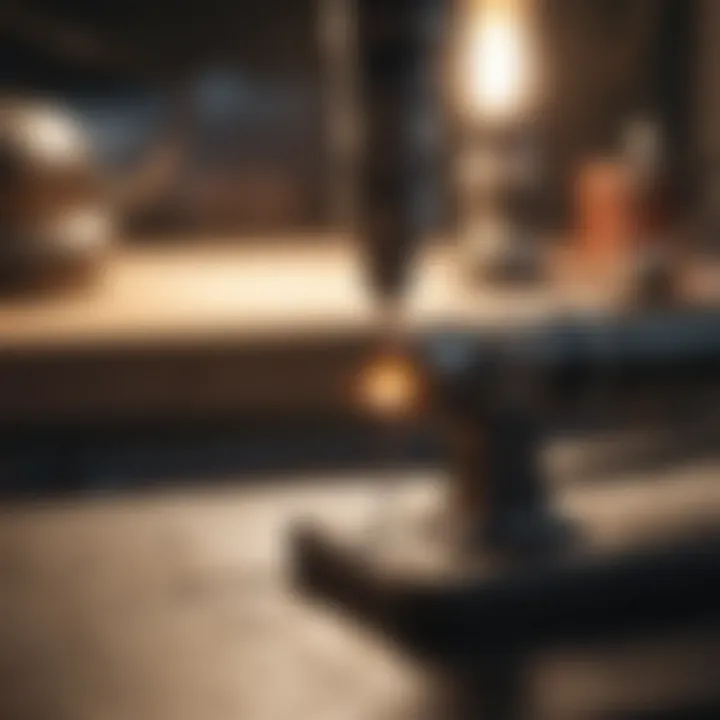
Intro
Soldering jewelry is a timeless craft that intertwines creativity with meticulous skill. Whether you’re a budding artisan or a seasoned jeweler, understanding the fundamental elements of soldering can elevate your work from mere ornamentation to exquisite craftsmanship. This guide takes a closer look at the critical tools, materials, and techniques that form the backbone of effective soldering, enabling creators to produce lasting pieces.
Craftsmanship in jewelry making requires not only artistic vision but also practical skills that can be developed over time. Soldering, in particular, plays a vital role in fusing metals together, allowing for unique designs and structural integrity. Knowing how to solder proficiently can dramatically expand one’s creative horizons, ushering in a plethora of design possibilities. From classic styles to modern interpretations, soldering unlocks a world of opportunities for artistic expression.
In this guide, we’ll cover essential tools that every jeweler should have at their disposal, delve into the types of solders available, and talk about techniques that are critical for achieving successful results. Additionally, we won’t overlook safety measures that must be observed, nor will we shy away from common challenges that might arise during the process. Understanding these elements can inspire confidence in your soldering abilities and enhance your overall craftsmanship.
Understanding Soldering in Jewelry Making
Soldering is the lifeblood of jewelry making. It's the magical process that unites separate pieces of metal into a cohesive whole. Without it, the artistry and vision behind each design would remain fragmented, utterly lacking in form and function. By grasping the essential aspects of soldering, jewelers can unlock the potential of their materials and bring their creative ideas to fruition.
Definition of Soldering
At its core, soldering is a method of joining metals together by melting a filler material, known as solder, which flows into the joint between them. This process typically occurs at lower temperatures than welding, making it suitable for delicate components in jewelry. Solder itself can come in various forms—sheets, wires, or even paste—depending on the requirements of the task at hand.
Here’s a breakdown:
- Solder types can vary based on the metal being joined, the project requirements, and the desired characteristics of the finished piece.
- Flux, a chemical cleaning agent applied to the metals before soldering, helps prevent oxidation and allows the solder to flow more freely.
In essence, soldering is about creating a seamless blend of metal, where the bond is often as strong as the original pieces.
Importance of Soldering in Jewelry
The importance of soldering extends far beyond just the assembly of parts. Here are a few key reasons why it holds a prominent place in jewelry making:
- Durability: Properly soldered pieces can withstand wear and tear better than those merely glued or mechanically fastened.
- Versatility: Soldering facilitates the creation of intricate designs that might be impossible through other methods. It allows for layered textures, varying metal types, and artistic flourishes.
- Aesthetic Coherence: A good soldering job ensures the final product looks polished. Gaps or unsightly joins can detract from the beauty and value of the jewelry.
- Functional Integrity: Soldering isn’t just about aesthetics; it ensures functional elements like clasps and chains operate smoothly.
"Soldering is where artistry meets engineering; a beautiful dance of heat and precision that results in wearable art."
Required Tools for Soldering Jewelry
When it comes to soldering jewelry, the tools you gather serve as the backbone of your craft. Choosing the right instruments can make the difference between a seamless joining of metals and a workshop that resembles a battlefield. Each piece of equipment plays a distinct role, enhancing your ability to execute intricate designs and ensuring safety throughout the process. Let’s delve into the essential tools you need to elevate your soldering skills.
Soldering Iron or Torch
The soldering iron or torch is more than just a tool; it’s the lifeblood of any soldering project. Each serves its unique purpose—while the soldering iron provides controlled heat to smaller components, a torch offers a more versatile application suitable for larger pieces or different types of metal. For a beginner, an adjustable soldering iron can be a simpler choice, allowing for precision and ease of control. If you’re looking to tackle more complex designs, a torch like the Bernzomatic TS8000 can provide the intense heat necessary to melt solder quickly. Choosing between these options ultimately hinges on your style and the materials you're working with.
Third Hand Tool
The third hand tool isn’t about magic; it’s about support. This device usually comes with alligator clips and an adjustable arm to hold pieces in place while you work. Imagine trying to balance everything on your own. It’s like juggling flaming torches during a circus act. Without proper support, you run the risk of ruining a precious piece. This tool is especially essential for delicate work, offering stability and freeing your hands for the actual soldering action. Think of it as your trusty sidekick that always has your back.
Tweezers and Pliers
When it comes to manipulating small components, tweezers and pliers are your best allies. Tweezers help you pick up tiny bits of metal or solder without getting burned. You’ll appreciate them especially when dealing with hot pieces. On the other hand, pliers come in various forms—chain-nose, flat-nose, and round-nose. Each type has its strengths, enabling you to shape and adjust metal as needed. These tools might seem commonplace, but their importance cannot be overstated. They offer finesse that can ultimately save a project from disaster.
Soldering Block
The soldering block is more than just a surface to work on; it influences the quality of your work significantly. A good block can absorb heat, preventing damage to your workbench and allowing you to manage temperature effectively. Consider investing in a block made from firebrick or ceramic. These materials can endure steady heat and provide a stable base for your projects. A soldering block is essentially where ideas take form; treating it with respect will help you create pieces that stand the test of time.
Essential Materials for Soldering
When embarking on the journey of soldering jewelry, the materials you choose play a pivotal role in the quality of your work. Unlike using a hammer or a saw, where skill can compensate for material shortcomings, soldering is highly dependent on the specific compositions and their behaviors under heat. Thus, understanding essential materials is key to achieving neat, strong, and long-lasting solder joints.
Different Types of Solder
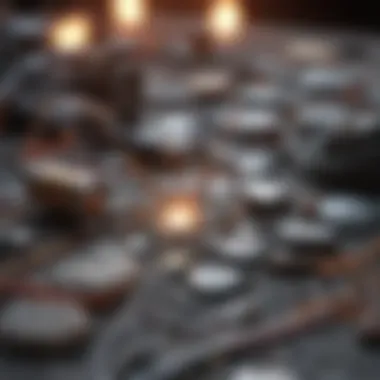
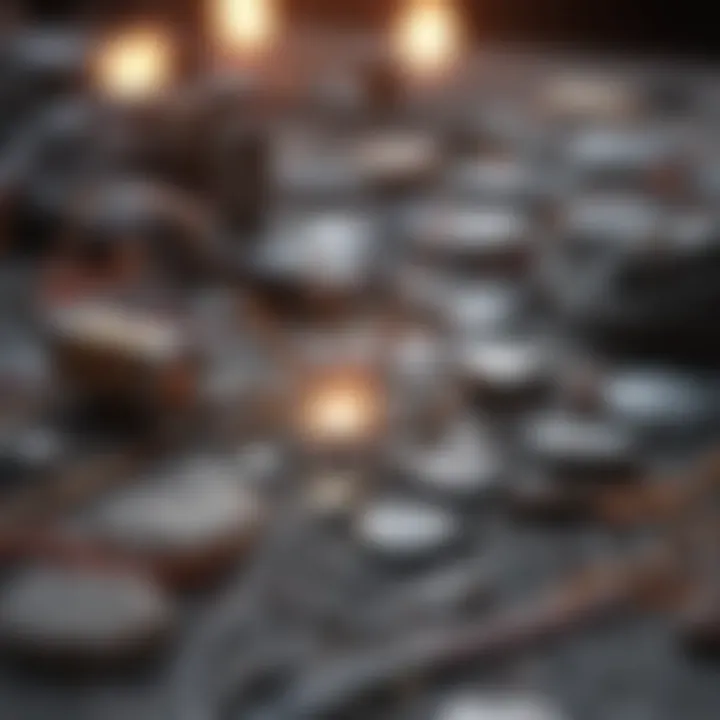
Solder comes in various types, each with its own characteristics and intended applications. The most common categories of solder used in jewelry making include:
- Soft Solder: This is generally lead-based, with a lower melting point. It’s more common in electronics and plumbing. Not recommended for jewelry due to durability issues.
- Rosin-Core Solder: A mixture of tin and other metals like copper or silver, this solder type contains rosin flux within its core. Great for delicate connections but likely not suitable for heavy-duty jewelry.
- Silver Solder: Often favored in jewelry making, silver solder is primarily a blend of silver and copper. It comes in a few different colors – white, yellow, and even pink – depending on the copper content.
- Gold Solder: Gold solder is specific to the type of gold you are working with – yellow, white, or rose gold. Matching solder to your metal works ensures the finish looks uniform.
Choosing the right type of solder is crucial, as it'll affect the color, strength, and application of your final piece. When in doubt, the silver solder usually provides a reliable connection and aesthetic finish.
Flux and Its Functions
Flux is an unsung hero in the soldering arena. It serves multiple purposes that directly enhance the soldering process:
- Prevents Oxidation: During heating, metals tend to oxidize. Flux prevents this oxidation, allowing for a stronger bond between the metals being soldered.
- Improves Flow: The presence of flux helps solder flow smoothly across the surfaces, creating a more efficient and clean join. Think of it as a lubricant for metal; it helps everything merge fluidly.
- Cleans Surfaces: Flux cleans the metal surfaces, which is vital for effective soldering. If the surface of your metals isn't clean, the solder might not adhere properly, leading to weak joints and potential failures down the line.
When selecting flux, consider the type of solder you’ll use. For silver soldering, for instance, a borax-based flux can be quite effective. On the other hand, acid-based flux may be better suited for specific situations in jewelry making.
"The right flux can mean the difference between a strong, lasting bond and a looming disaster."
In sum, the proper selection of solder and flux not only enhances the functionality of your finished jewelry but also greatly influences how seamless and aesthetically pleasing your pieces appear. As you gather your materials, take the time to understand their properties and consider how they interact. This knowledge serves as the bedrock for superior craftsmanship.
Setting Up Your Workspace
Creating a functional workspace is crucial for anyone who engages in soldering jewelry. It’s not just about where you work; it’s about creating an environment that fosters creativity, safety, and efficiency. A well-set workspace can make the difference between a successful project and a frustrating experience. Consider the elements that play a vital role in your setup, tools organization, and overall workspace efficiency.
Choosing the Right Environment
The choice of environment can seriously impact your soldering success. A well-lit, well-ventilated space is essential. Natural light is great, but if that's not an option, invest in good task lighting. You want to see what you're doing with clarity, avoiding shadows or dim spots that could lead to careless mistakes.
- Lighting: A bright desk lamp with a flexible neck can illuminate your work. Some artisans even use magnifying lamps to spot those tiny elements.
- Ventilation: Soldering generates fumes, some of which aren’t friendly to breathe. A simple window can work wonders, or you might consider a fume extractor if you're looking for an upgrade. This is crucial, especially if you’re using flux that produces unpleasant vapors.
- Space: Ensure your workspace isn’t cramped. You need to stretch out and reach for your tools without knocking over that delicate pendant you just crafted. Too much clutter can lead to accidents.
- Comfort: Don’t overlook your own comfort. An adjustable chair and a sturdy table at the right height can prevent strain. Your working hours can stretch, and you want to stay alert without discomfort.
Ultimately, choosing the right environment sets the groundwork for your creative journey and minimizes hindrances that can get in the way.
Organizing Your Tools and Materials
Once you have carved out that perfect space, it’s time to dive into organization. Instead of having a chaotic table strewn with tools and materials, aim for a systematic layout that makes everything easily accessible.
- Tool Storage: Invest in a tool organizer or toolbox. Ensure that your soldering iron, pliers, and tweezers are in dedicated spots. It might sound simple, but putting things back in their place saves time and reduces frustration.
- Solder and Flux Storage: Keep your solder and flux in labeled containers. Use small bins or boxes to separate different types of solder. This way, when you're ready to work, you don’t waste time searching through a heap of materials. Good organization translates to workflow efficiency.
- Work Surface: Ensure your work surface is clear. A soldering block is often best positioned front and center, easy to reach. Avoid cluttering it with unnecessary items. You will need sufficient space to maneuver your pieces while working.
- Labeling System: Adopt a labeling system for bins and boxes. Perhaps color-coded for flux types or solder grades. This is especially handy when you start accumulating materials and need an easy way to find them.
By organizing your tools and materials effectively, you ensure that your focus can remain on the art of soldering itself rather than the hassle of searching for what you need.
Remember: A clutter-free workspace isn't just a preference; it's a key ingredient to mastering the art of soldering jewelry.
Soldering Techniques and Tips
When it comes to soldering jewelry, techniques play a pivotal role in the overall success of the creation. Mastering these approaches not only enhances the quality of the work but also makes the process smoother and more enjoyable. Understanding the nuances of soldering techniques allows artisans to tackle intricate designs while avoiding common pitfalls. This section will dive into essential practices to ensure your soldering is top-notch, focusing chiefly on preparation, heating, and application of solder.
Preparing Your Pieces to Solder
Proper preparation of the jewelry pieces is the cornerstone of any successful soldering project. This step not only sets the stage for a flawless join but also minimizes the chances of mishaps during the application of heat.
- Clean Surfaces: Begin by cleaning the surfaces of the pieces you wish to join. Any grime, oxidation, or resin can interfere with how the solder adheres to the metal. You can achieve this by using a fine grit sandpaper or a metal file to remove any unwanted material.
- Fit Pieces Together: Before reaching for the torch, it is crucial to ensure that the pieces fit snugly together. Any gaps can lead to weak joints or areas where the solder cannot flow properly.
- Applying Flux: After cleaning, apply flux to the area where you want to solder. This substance serves as a barrier to oxidation and helps the solder flow evenly. Choosing the right type for your metal is key—different metals may require different flux types.
Taking these preparatory steps seriously can save you a lot of time and effort down the road.
Heating Techniques
Heating is an art as much as it is a science in the soldering realm. Too much heat can burn your pieces or cause them to warp, while too little can result in insufficient solder flow. Here are a few pointers on effective heating:
- Consistent Heat Application: Use a soldering iron or torch with a steady flame. Avoid fluctuating temperatures as this can create unwanted stress in the material.
- Heat the Metal, Not the Solder: Focus on heating the metal pieces and let the heat draw the solder into the join. The solder should flow naturally into the joint when everything is at the right temperature.
- Watch for Color Changes: Different metals will change colors when they reach specific temperatures. Keeping an eye on these changes gives a good indicator that the metal is ready for soldering.
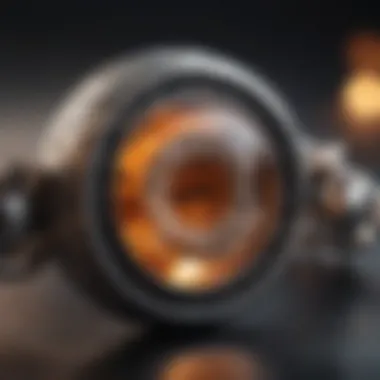
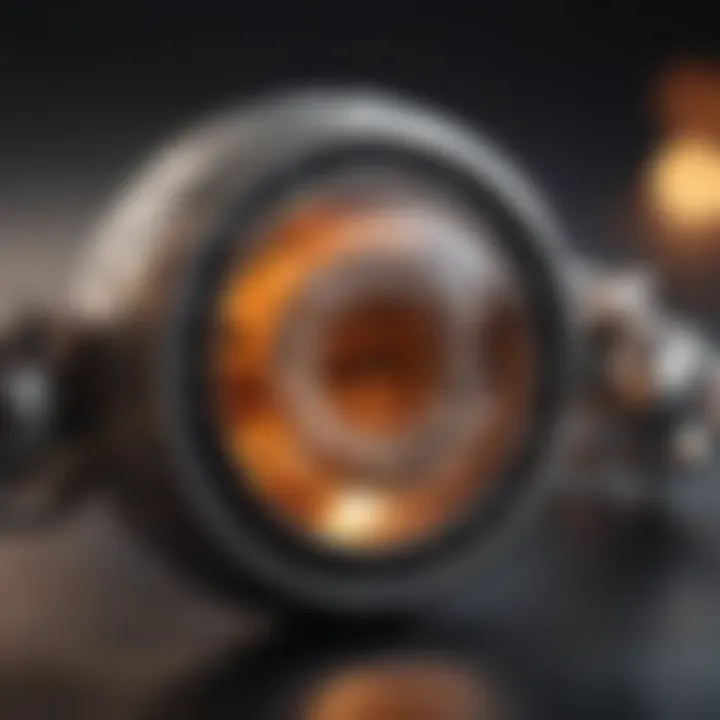
Utilizing these heating techniques effectively can make a world of difference in your soldering endeavors.
Applying Solder Effectively
Once your pieces are prepared and the heat is just right, it’s time to apply the solder. This part of the process requires a steady hand and some know-how to achieve a robust, clean joint:
- Use the Right Amount of Solder: A common mistake is using either too much or too little solder. Ideally, there should be just enough to fill the joint without creating excess that needs to be cleaned up later.
- Dab, Don’t Pour: Rather than pouring solder into the joint, dab small amounts with a soldering iron or tweezers. This allows for more control and ensures that the solder goes exactly where it’s needed.
- Allow Time for Cooling: After applying solder, give your piece some time to cool naturally. Abrupt changes in temperature can lead to cracking or other defects in the join.
Remember, patience is a virtue. Taking your time during this stage pays off in the longevity and beauty of your finished piece.
In sum, elevating your soldering skills hinges significantly on refining your techniques. By thoughtfully preparing your pieces, mastering heating, and applying solder effectively, you position yourself to create stunning, durable jewelry that speaks to your skill and artistry.
Safety Considerations for Soldering Jewelry
Soldering jewelry can be a rewarding and delightful activity, but it comes with its own set of risks. A successful soldering experience starts not just with the right techniques and materials, but significantly with ensuring a safe working environment. Taking the time to manage safety considerations can not only prevent accidents but also enhance your overall soldering experience. Proper safeguards allow artisans to focus on their craft without distractions or fear of harm.
Personal Protective Equipment
When you dive into soldering, the first step in prioritizing personal safety is to gear up appropriately. Personal Protective Equipment (PPE) forms the first line of defense against potential hazards arising from fumes, hot tools, and molten metals. Here’s what a focused jeweler should wear:
- Safety Glasses: Protect your eyes from spatter and bright flashes that may occur during soldering. Select goggles that fit snugly for maximum protection.
- Respirator or Mask: Soldering can generate fumes that may irritate your respiratory system. A mask fitted with a carbon filter is a smart choice.
- Heat-Resistant Gloves: Handling hot materials requires gloves that can endure high temperatures. Look for gloves specifically made for soldering.
- Protective Clothing: Wear a long-sleeved shirt and non-flammable clothing. This helps to shield your skin from any accidental burns.
Equipping oneself with the appropriate gear might seem tedious, but the benefits outweigh the inconvenience. Remember, taking these precautions is not only about protecting yourself but also about creating a safe space for others who may share your workspace.
Always remember: "Safety first makes it last."
Ventilation and Work Environment
Creating a safe work environment goes beyond just wearing protective gear. A proper workspace is vital to avoid dangerous situations. Proper ventilation is crucial. Here's what to consider:
- Choose an Open Area: Ideally, soldering should be done in a well-ventilated open space. This can significantly reduce the concentrations of harmful fumes in the air you breathe.
- Use a Fume Extractor: If you’re soldering indoors, consider installing a fume extractor. This apparatus draws away harmful fumes right from the source.
- Keep Emergency Equipment Handy: Have a fire extinguisher close by. It’s also wise to keep a first-aid kit on hand, just in case.
- Good Lighting: Make sure your workspace is well-lit. Poor lighting can lead to mistakes that could result in accidents or damage to your pieces.
All these aspects work together to foster a workspace conducive to creativity, allowing you to focus on crafting without worrying about hazards. Pay attention to these safety measures, and you’ll create a thriving environment for jewelry soldering.
Common Soldering Issues and Solutions
Soldering, while a fundamental skill in jewelry making, can throw a few curveballs your way. Just like any art form, issues can crop up that challenge the artisan's patience and skill. Identifying and resolving these problems is crucial, especially for those who aspire to create exquisite pieces with integrity and durability. In this section, we will explore common soldering challenges and share practical solutions to help enhance your craftsmanship.
Identifying Problems
The first step in troubleshooting is recognizing when things go awry. Several telltale signs can alert you to a soldering issue. Look out for the following:
- Weak Joints: If the pieces of jewelry look precariously held together or can be moved without much effort, the joint may not be secure.
- Uneven Seams: A good soldered piece should have smooth, even seams. If you see gaps or irregularities, that’s a signal something went wrong.
- Excessive discoloration: If metal appears burnt or discolored, this usually indicates overheating, which can lead to weak connections.
- Solder pooling: When solder gathers in an unwanted area instead of flowing into the joint, it can affect both the aesthetic and the integrity of the piece.
Being able to spot these problems early on can save you from greater headaches down the road. The sooner you address an issue, the less likely it will become a monumental task.
Fixing Cold Joints
A cold joint occurs when the solder does not flow properly, often leading to a joint that is not as strong as it should be. Here's how to handle it:
- Reheat the joint carefully: Focus on the area around the joint and gently apply heat. It’s crucial not to overheat, as it can cause further damage.
- Add more solder: If the joint seems too bare, adding a bit of solder can help. Ensure the solder flows well and encapsulates the metals involved. Using the proper solder wire for the job also matters; different solders have varied melting points.
- Cool and inspect: Once the repair is done, allow the piece to cool naturally. Check the joint for any remaining gaps or weaknesses. If there still are issues, repeat the process.
Fixing cold joints can take a bit of finesse, but with practice, you'll become adept at ensuring secure connections.
Dealing with Excess Solder
Excess solder is another common problem that can mar the beauty of your pieces. Here’s how to address it:
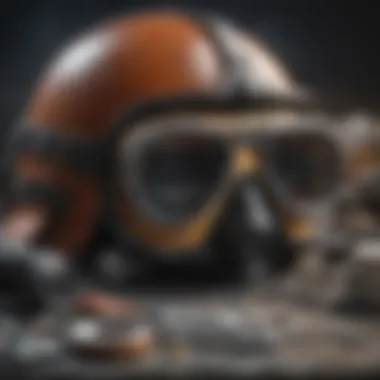
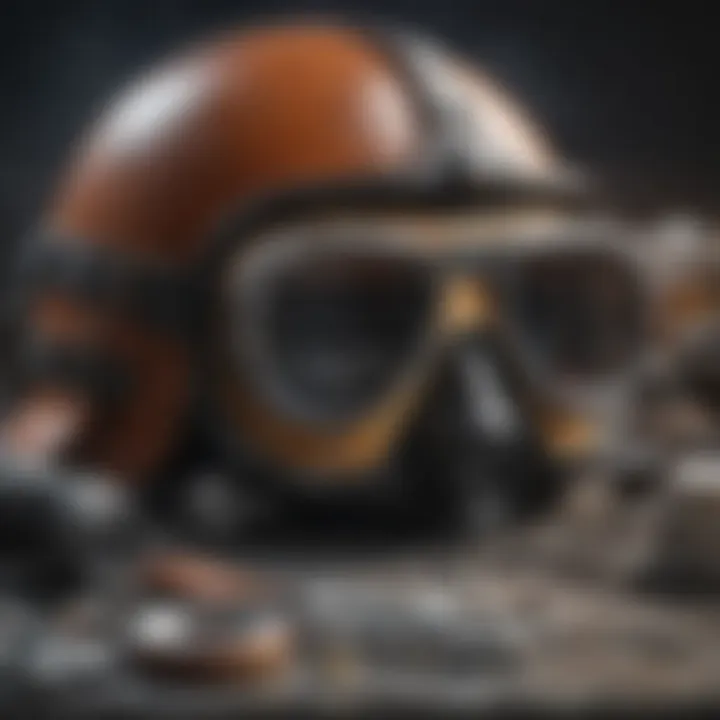
- Gentle Filing: Use a fine file to carefully remove excess solder. Maintain a light touch to avoid scratching the metal underneath.
- Dremel Tool: If you're dealing with a thicker layer, a Dremel tool can be effective. Just be cautious—too much pressure can create deeper scratches.
- Pickling: After filing or grinding, pickle the piece to remove any oxidation or residual solder material. This will restore the shine and ensure the metal is clean.
Excess solder can often be managed with a few careful techniques, allowing for a cleaner, more professional finish.
Being able to troubleshoot and solve soldering problems can mean the difference between a work of art and a regrettable mishap.
In every craft, challenges arise, and soldering jewelry is no exception. By developing an eye for common issues and familiarizing yourself with solutions, you can elevate your skills and ensure the quality of your work. Every mistake offers a learning opportunity that can lead to more refined techniques and a deeper understanding of the craft.
Advanced Soldering Techniques
Soldering is not simply about joining pieces of metal together; it's about merging creativity with technical skill. Understanding advanced soldering techniques significantly enhances the ability to produce intricate and durable jewelry designs. Mastery in this area opens the door to using a variety of metals, achieving clean joints, and applying heat with precision. This section explores two vital subtopics to elevate your soldering expertise: soldering different metal types and using a micro torch.
Soldering Different Metal Types
Different types of metals come with their individual characteristics and requirements when it comes to soldering. It's crucial to understand these differences to achieve seamless connections and maintain the integrity of the jewelry piece. Here’s a quick rundown of some common metal types and their soldering needs:
- Gold: A favorite among jewelers, gold provides excellent soldering capabilities. It's relatively easy to work with, but you should ensure that your solder matches the karat of your gold piece.
- Silver: Often regarded as more challenging, sterling silver can tarnish, so using proper flux is essential. Choose a solder with a melting point lower than the silver to avoid warping.
- Copper: With its higher thermal conductivity, copper requires quick soldering methods to prevent overheating. Use a suitable flux to ensure a clean joint.
- Brass: This metal can be a bit tricky due to its zinc content. The key to soldering brass is to work quickly and ensure adequate ventilation to prevent fume inhalation.
When moving between metals, adjusting the soldering heat is essential to avoid discoloration or damage. Each type of metal has its unique melting point and behavior when heat is applied.
"The art of soldering pivots on understanding your materials, knowing their quirks can save your piece from a world of headaches."
Using a Micro Torch
The micro torch is a jewelers' best friend. While traditional soldering irons have their place, the versatility and precision offered by a micro torch can turn a complex project into a smooth operation. Here’s how the micro torch stands out:
- Precision: Unlike larger torches, a micro torch provides a focused flame that allows for intricate work without affecting surrounding areas.
- Portability: These torches are compact, making them easy to take to workshops and classes or even to work in smaller spaces.
- Adjustability: Most micro torches come with adjustable flame settings, accommodating various soldering requirements. Whether you're working with fine details or larger surfaces, you're covered.
However, using a micro torch comes with considerations. Maintaining a steady hand is paramount; the small flame can easily be lost if you’re not careful. Additionally, practice is necessary. If you've only used soldering irons, the transition might take a little time. Consider starting with practice projects like simple rings or pendants before venturing into more complex creations.
Finishing Techniques Post-Soldering
Once the soldering work is done, it’s time to shift focus to finishing techniques. These techniques play a pivotal role in making your jewelry not just functional but also aesthetic. The post-soldering phase enhances the piece’s appearance, removes any impurities, and ensures a polished and refined final product. Ignoring this stage can leave a piece looking rough or unprofessional, detracting from the overall craftsmanship.
Cleaning Soldered Items
Cleaning soldered items is an essential step that cannot be neglected. After soldering, flux residues, tarnish, and oxidation might have accumulated on the metal surfaces. Not addressing these issues can lead to poor adhesion in future modifications or repairs. Here are some common cleaning methods:
- Ultrasonic cleaner: This gadget uses sound waves to remove dirt and grime effectively. Just place your piece in a cleaning solution and let the machine do the work.
- Soapy water: For a gentle approach, warm water mixed with mild soap can do wonders. After soaking the item for a few minutes, scrub lightly with a soft brush to remove residues.
- Chemical cleaners: Certain chemical cleansers can assist in removing soldering debris but be cautious. Always follow the instructions and ensure safety measures are in place.
Once cleaned, rinse the jewelry thoroughly and dry it with a soft cloth to prevent further moisture build-up.
Polishing and Final Touches
Polishing is arguably one of the most satisfying steps after soldering. It transforms a functional piece into a work of art. The objective here is to create a surface that shines brightly, emphasizing the intricacies of your design. Here are methodologies and materials you might consider:
- Polishing cloths: Using a high-quality polishing cloth can remove minor scratches and enhance shine.
- Rotary tools: For larger pieces or sections that need significant work, a Dremel tool equipped with various polishing bits can speed up the process significantly.
- Metal polish: Commercial metal polish can leave your finished piece gleaming. Just apply a small amount on a clean cloth and buff the surface until the desired shine is achieved.
Furthermore, don’t forget the final touch. Check for any sharp edges or rough spots that need smoothing. A little attention here can significantly enhance comfort when wearing the jewelry and adds to its overall quality.
A well-finished piece not only speaks volumes about the maker's skills but also elevates the jewelry's value.
In essence, finishing techniques are not merely an afterthought; they are a fundamental part of the jewelry-making process. By diligently selecting your cleaning and polishing methods, you ensure that your artistic vision is carried forward into the tangible outcome.
Resources for Further Learning
Continuing education is paramount in any craft, and soldering jewelry is no exception. This section highlights the significance of expanding your knowledge beyond the basics. Whether you’re just starting out or have been soldering for years, seeking resources to improve your skill set can enhance your jewelry-making experience tremendously. Accessing new information and techniques not only helps you refine your craft but also inspires creativity. In the fast-paced world of jewelry making, staying updated with the latest trends and tools can give you a distinct edge.
Books and Online Resources
Diving into books and online materials is an excellent way to deepen your understanding of soldering. Several authors have dedicated their works to the intricate world of jewelry making, offering insights that cannot be gleaned from hands-on experience alone.
Some popular recommendations include:
- "The Complete Metalsmith" by Tim McCreight – This book serves as an all-in-one guide. It has sections on tools, techniques, and materials that can aid both beginners and seasoned professionals.
- **