Exploring Dremel Grinding Attachments for Precision Tasks
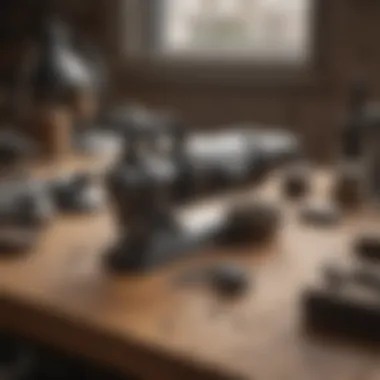
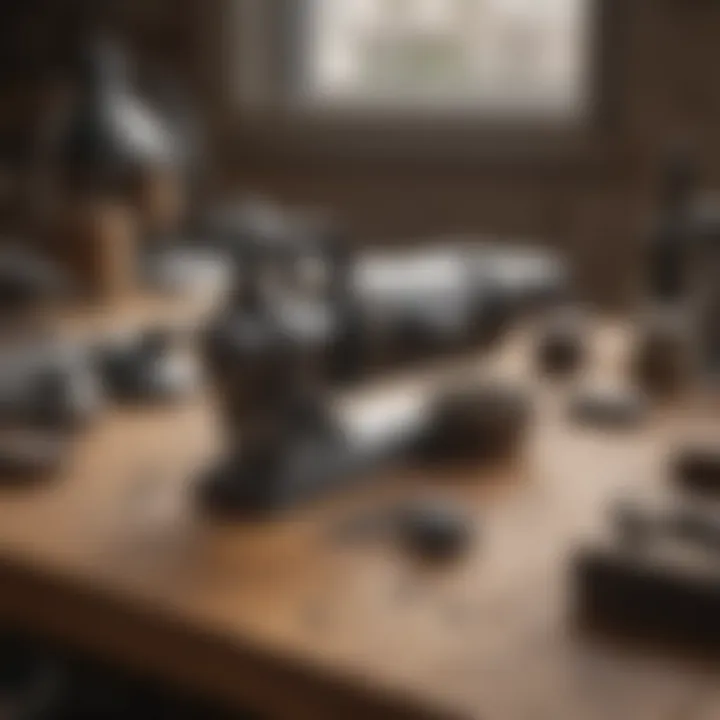
Intro
Dremel grinding attachments have become a game changer for hobbyists and professionals alike, especially for those diving into the world of collectibles, rocks, and fossils. If you're the kind of person who appreciates the finer details of craftsmanship, knowing how to effectively use these tools can take your work to the next level. In this guide, we will explore the various types of Dremel attachments available, their applications, and the best practices to ensure efficiency and precision in your grinding tasks.
The significance of mastering Dremel tools cannot be overstated. Whether you're looking to refine a delicate collectible or expertly shape a fossil, understanding the right attachments and techniques makes all the difference. This guide is tailored for both novices who are just starting out and seasoned collectors who wish to enhance their skills.
So, let’s take a deep dive into the world of Dremel grinding attachments and unlock the potential these tools offer.
Topic Overview
Definition of Rocks, Fossils, and Collectibles
When we talk about collectibles, it encompasses a vast range of items, from rare minerals and gems to unique fossils that intrigue both scientists and enthusiasts.
- Rocks: Naturally occurring solid aggregates of minerals. They come in various types, including igneous, sedimentary, and metamorphic, each with unique characteristics and stories to tell.
- Fossils: Remnants of ancient life, preserved in sediments or rocks, give us insight into Earth’s history. They can be bones, imprints, or even entire organisms.
- Collectibles: Items that are gathered by enthusiasts due to their rarity, beauty, or historic significance. This could range from specific rock specimens to ancient fossil finds.
Brief History and Significance
The practice of collecting rocks and fossils dates back centuries, often rooted in scientific exploration. In the 19th century, paleontology and geology gained momentum, leading to a surge in the popularity of collecting. These pursuits aren't just hobbies; they reflect a deep-seated curiosity about our planet's history and its natural wonders. Today, collectors use various tools, including Dremel grinding attachments, to enhance their collections and make the most of their finds.
As we navigate this comprehensive guide, we will unravel the intricacies of Dremel attachments, so you can approach your crafting with newfound confidence and skill.
Identification and Classification
How to Categorize Items
Understanding how to categorize your collections is essential. Here's how you can think about organizing your rocks and fossils:
- Type of Material: Distinguish between minerals, sedimentary rocks, igneous rocks, etc.
- Origin: Where they were collected or sourced from; this can include local sites or renowned fossil beds.
- Rarity: Items can be classified based on their availability.
Tips for Identifying Key Features
When examining your collectibles, focus on these aspects to get a better understanding:
- Texture: Describe how the surface feels—smooth, rough, layered.
- Color: Note any unique color patterns or variations that set the item apart.
- Form: Look at the overall shape; is it jagged, rounded, or intricate?
- Fossil Marks: For fossils, pay attention to any identifiable features that link it to a specific era or species.
By effectively categorizing your items, you not only enhance your ability to appreciate your collection but also set the stage for using Dremel attachments effectively in your future projects.
"Understanding the foundational characteristics of your collectibles sets up the entire framework for effective crafting and enhancing with tools like Dremel attachments."
With this groundwork laid, we can now transition into the specifics of various Dremel grinding attachments, exploring how they can be utilized for your crafting needs.
Intro to Dremel Grinding Attachments
Understanding the capabilities of Dremel grinding attachments is crucial for anyone delving into the realm of crafting and collectible restoration. These tools aren’t just small machinery; they empower hobbyists, professionals, and enthusiasts alike to achieve precision and intricacy in their work. As we explore the different facets of Dremel grinding attachments, the significance of these tools will become evident when considering how they can elevate the quality of projects, be it in jewelry making or detailed restorations.
With the right attachments, one can transform a seemingly mundane task into a showcase of skill and creativity. The article aims to equip readers with insights about Dremel tools, their applications, and how to maximize their effectiveness in various crafting and restoration projects.
Understanding Dremel Tools
Dremel tools are akin to Swiss Army knives in the world of craft and repair—versatile devices that blend power and functionality. A Dremel tool essentially serves as a rotary tool, but what sets it apart is its adaptability. Users can easily switch out attachments to handle a myriad of tasks.
These tools come in various sizes and models, but the common thread is their ability to rotate at high speeds, allowing them to cut, sand, grind, and polish with stunning efficiency. For instance, a Dremel 4000 or even the more compact Dremel Lite can accommodate a variety of grinding attachments, making it a valuable companion for those engaged in activities that require detail and finesse, such as working with rock and fossil specimens.
Being well-versed in the specific functions of each attachment ensures that one maintains the right tool for the right job. Knowledge about these tools goes a long way in achieving satisfying results, especially when manipulating delicate materials like gems or intricate metalwork.
Importance of Grinding Attachments
Grinding attachments are the unsung heroes of Dremel tools, often overlooked until the moment they are needed. Their significance cannot be understated as they facilitate control and precision that standard rotary tools may not provide. With grinding attachments, users can tackle everything from smoothing rough edges to performing detailed engraving.
Among the attachments, users find various types including aluminum oxide grinding stones, which excel at shaping and smoothing materials. In contrast, carbide burs, known for their toughness, are ideal for grinding harder materials.
In short, the right grinding attachment can mean the difference between a hastily executed job and a finished product that speaks volumes of skill and dedication. Investing time in selecting and mastering these attachments allows rock and fossil collectors to enhance their craftsmanship effectively.
"Using Dremel grinding attachments elevates your work, bridging the gap between potential and performance."
By the time you finish this guide, the landscape of Dremel tools and their grinding attachments will be clearer, allowing you to make informed decisions that may transform your crafting efforts.
Types of Dremel Grinding Attachments
In the world of Dremel tools, understanding the types of grinding attachments available is crucial for anyone looking to enhance their craftsmanship. Each type brings unique benefits and is suited for specific tasks. When it comes to working with delicate materials or hard substances alike, the choice of attachment can make all the difference. For enthusiasts and professionals, knowing how to match the right attachment with the right job serves not only to improve efficiency but also to elevate the quality of the finished product.
Aluminum Oxide Grinding Stones
Aluminum oxide grinding stones are a valuable staple in any toolbox. These attachments are known for their durability and effectiveness in grinding and shaping various materials, from metals to hard woods. The rough texture of these stones allows for an aggressive cut, making them ideal for heavy-duty tasks.
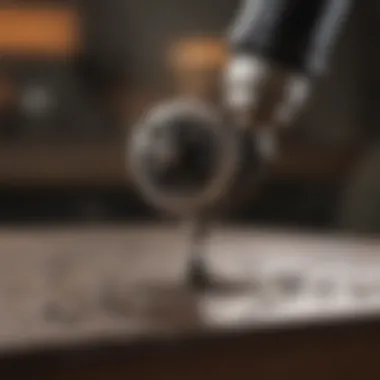
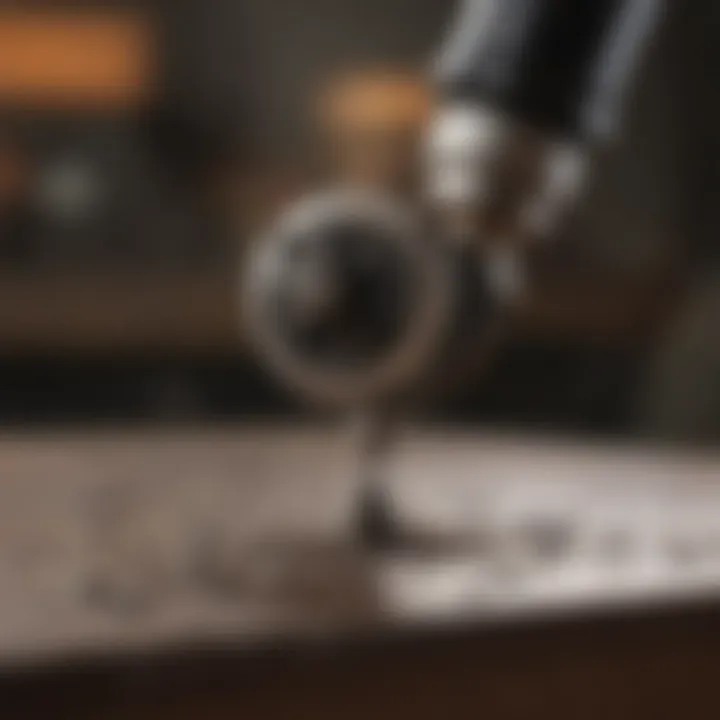
They also come in a variety of shapes, which gives users the flexibility to access tight corners or flat surfaces as needed. This makes them particularly useful in detailed work, such as jewelry making or model crafting. Because of their toughness, maintaining sharpness over time becomes less of a chore, and the user can enjoy extended periods of high-performance.
Carbide Burs
Carbide burs stand out for their exceptional hardness and resistance to wear. These are often employed in applications where precision carving is paramount. The design of carbide burs allows for intricate details to be added to pieces, often used in woodwork and stone carving. The ability to sculpt details with finesse often attracts those involved in art or craftsmanship that requires meticulous effort.
These attachments are generally categorized by shape, such as ball-shaped, flame-shaped, and tree-shaped, each appropriate for ensuring a suitable approach to various projects. However, bear in mind that carbide burs can generate heat during prolonged use, so it is important to keep an eye on any indicators of overheating.
Diamond Grinding Wheels
When it comes to durability, diamond grinding wheels reign supreme. Infused with diamond particles, these attachments can tackle some of the toughest materials, making them ideal for glass, ceramics, and hard metals. Their incredible strength allows for precision work that can hardly be matched by other types of grinding attachments.
Diamond wheels are particularly favored in restoration tasks. If you are working to bring back the shine of an antique or delicate collectible, these wheels will serve you well. It's worth noting that while they are more expensive than other types, investing in high-quality diamond grinding wheels can pay off significantly in terms of longevity and performance.
Rotary Grinding Bits
If you’re looking for versatility, rotary grinding bits should be on your radar. Available in different materials and sizes, they provide adaptability across various tasks. Ideal for both detailed engraving and light sanding, these bits can shift easily between roles in your workflow. The convenience they offer is especially important for hobbyists working on projects that may require several different approaches throughout.
One should however be mindful of speed settings when using rotary bits to achieve the desired effect without causing damage to the material. This flexibility makes them a favorite among many crafters, ensuring that no job feels out of reach.
"The right attachment can turn a tedious task into one that sparkles with creative potential."
All in all, knowing the types and applications of Dremel grinding attachments better equips one for any task at hand. Selecting the appropriate attachment not only optimizes the efficiency of the work but also assures that the results meet the standards set by your creative ambitions.
Choosing the Right Grinding Attachment
Selecting the appropriate grinding attachment for your Dremel tool plays a vital role in achieving the desired outcome, especially when it comes to precision work like crafting with rocks and fossils. Making the right choice not only enhances the effectiveness of your task but also minimizes the risk of damage to both the attachment and the material you are working on.
One of the main considerations when choosing a grinding attachment is the material hardness. Different attachments are designed to handle varying levels of hardness, and using the wrong attachment can lead to ineffective results or, worse, damage the workpiece. An informed choice also contributes to safety, as incorrectly matched tools can overheat or wear out faster, leading to potential hazards.
Assessing Material Hardness
To assess material hardness, you can start by using tools like the Mohs scale, which ranks materials based on their ability to scratch others. For example, soft materials—like talc—have a rating of 1, while harder minerals like diamonds rank up to 10. By testing a small, inconspicuous spot, you can get a better idea of where your material stands on this scale. This insight serves as a guide in selecting attachments.
When working with soft materials, you might opt for attachments like aluminum oxide grinding stones, as they offer a gentler touch. However, tougher materials necessitate using more robust attachments like diamond grinding wheels. Knowing the hardness of your target material ensures a smoother grinding experience.
Matching Attachment to Task
After assessing material hardness, it is essential to consider the specific task at hand. Different jobs demand different characteristics from your grinding attachments. For instance, if you’re polishing a rock surface, using a fine grit diamond bit might be in order. Conversely, for shaping rough edges, a coarse carbide bur can be more effective.
When you effectively match the attachment to your task, it can drastically enhance your efficiency. Below are a few points to consider:
- Task Complexity: For intricate designs, precision attachments are crucial, while broader attachments may work fine for simpler grinding tasks.
- Type of Material: Some materials respond better to specific tools; for instance, wood can be shaped easily with rotary grinding bits, whereas metals demand harder attachments like carbide burs.
- Desired Finish: If you aim for a polished surface, start with coarse tools and gradually progress to finer attachments. This layered approach can yield superior results.
"The key to effective grinding lies in understanding the tools and materials involved. Choosing wisely is half the battle won."
In navigating the vast array of Dremel grinding attachments, ensuring you choose one that aligns with your specific needs will set you on the path toward achieving fine results in your projects.
Specific Applications for Dremel Grinding Attachments
Dremel grinding attachments are not just tools; they are key assets for various hobbies and craftsmanship initiatives. When it comes to enhancing precision and efficiency in specific applications, the right attachment can make the difference between a superb finish and a less-than-stellar outcome. In this section, we will dissect three primary areas where Dremel grinding attachments can shine: jewelry making and repair, model making and miniature crafting, as well as the restoration of antique collectibles. Understanding these applications helps operators gauge the versatility of Dremel tools and optimize their projects.
Jewelry Making and Repair
Jewelry making is both an art and a science, requiring a delicate touch and a keen eye. Dremel grinding attachments can provide crafters with the precision they need for intricate designs. The carbide burs and diamond wheels stand out for cutting, shaping, and finishing various materials like gold, silver, and even softer gemstones.
Using the right attachment allows artisans to create unique textures. It also enables them to repair pieces, seamlessly removing scratches or blemishes. For instance, using a fine aluminum oxide stone helps smooth out rough areas while maintaining the integrity of the piece. This is crucial because while the goal is to enhance a jewelry item, one must avoid compromising its value or structure.
Some important considerations before diving into a project include:
- Material Type: Different materials demand different grinding tactics.
- Instance of Use: Be clear about whether you're crafting new pieces or restoring old ones.
- Attachment Selection: Opt for the attachment that aligns best with your project's demands.
Model Making and Miniature Crafting
Model making and miniature crafting require exacting detail and specialized techniques. Dremel grinding attachments offer a range of options suited to the delicate nature of these endeavors. From intricate architectural models to tiny figurines, operators can benefit from precision instruments.
For example, rotary grinding bits excel here. They can carve complex shapes or even engrave detailed patterns. When you’re fine-tuning components of a model, the right attachment can significantly enhance the fit and finish of parts. Additionally, the versatility of these attachments means you can switch between cutting, sanding, and polishing, all within the same workflow, making the crafting process much more efficient.
Considerations for effective model making include:
- Space Restrictions: Given the small scale of models, tools must fit comfortably and allow for close-quarters work.
- Attachment Variety: Using a mix of attachments can achieve different finishes and details.
- Patience and Control: Fine work demands a steady hand and the right technique; avoid rushing the job.
Restoration of Antique Collectibles
Restoring antique collectibles is a delicate process that requires a certain level of respect for the item’s original condition. Dremel grinding attachments can dramatically improve results when done correctly. Antique restoration often involves removing layers of grime, old finishes, and even minor damage. The use of grinding tools must be selective and judicious.
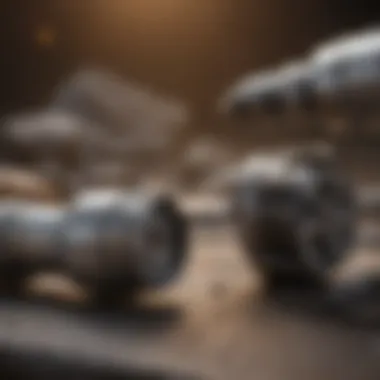
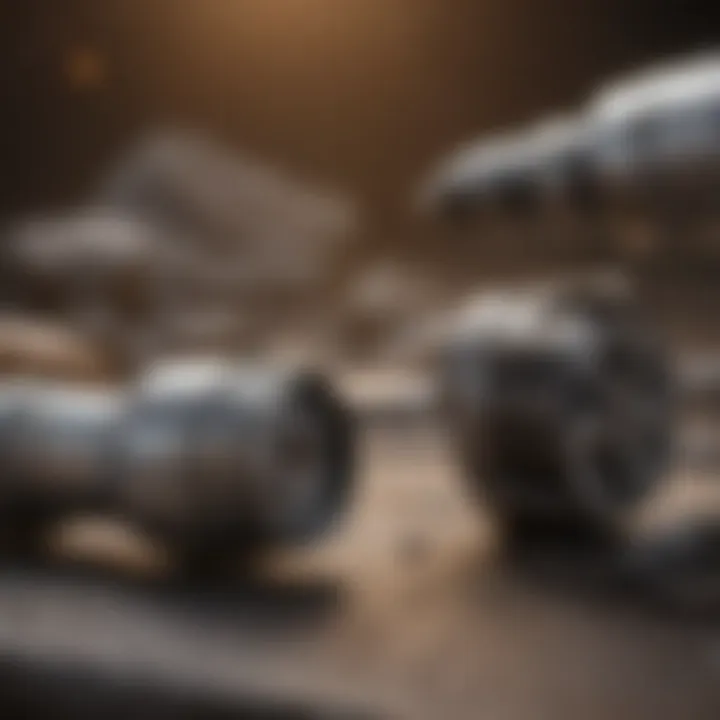
Diamond grinding wheels are exceptional for this purpose, as they can polish surfaces without causing significant wear. Additionally, they offer great control, allowing restorers to manage how much material is removed. It’s important to keep the original character of the collector’s item intact.
Key factors to bear in mind when restoring antiques include:
- Historical Value: Always prioritize preservation over alteration. Understand the origin of the piece before proceeding.
- Tool Selection: Not every attachment is suitable for every collectible; choose wisely.
- Consultation: When in doubt, consult with professional restorers or resources dedicated to antique care, ensuring rich historical artifacts remain as they are meant to be.
In summary, Dremel grinding attachments serve a cornucopia of needs across various craft disciplines. By mastering these attachments in specific applications, you amplify the quality of your work—be it jewelry craftsmanship, model making, or restoring antiques. Knowing not just how but when and why to use these tools is essential for anyone looking to delve deeply into their passion.
Best Practices for Using Dremel Grinding Attachments
Using Dremel grinding attachments can significantly elevate the quality and precision of your work, especially if you’re delving into detailed crafts or collectible restorations. Having a grasp on the best practices surrounding their use is critical. Implementing these guidelines not only enhances outcomes but also prolongs the life of your attachments and ensures your safety while operating these versatile tools.
Safety Measures
When working with any power tool, safety is paramount. Always keep in mind that Dremel grinding attachments can spin at high speeds, making safety precautions essential. Here are some key points to enhance your safety:
- Wear Protective Gear: Safety goggles are your first line of defense against flying debris. A dust mask is advisable too, especially when grinding materials that create fine dust.
- Secure Workpieces: Whether you’re working on a rock or a small collectible, make sure your piece is clamped down securely. This will not only prevent it from moving unexpectedly but will also provide stability during the grinding process.
- Work in a Well-Ventilated Area: Proper ventilation is crucial when you’re working with certain materials. Some can emit harmful fumes or dust that may be hazardous to inhale.
Remember, it’s better to take a few extra minutes to prepare and ensure safety than to rush and risk injury.
Proper Technique and Control
Having the right technique makes all the difference when using Dremel grinding attachments. Poor control can lead to uneven surfaces or even damage to your work. Here are some tips to keep in mind:
- Start Slowly: Begin at a lower speed setting. This helps you better gauge how your materialreacts to the attachment. Speed can be increased gradually as you gain more control.
- Hold the Tool Firmly: Grip the Dremel with both hands for stability. This allows for better control of the tool, especially when working on intricate details.
- Maintain a Steady Angle: The angle at which you hold the grinding attachment significantly influences the outcome. A consistent and appropriate angle prevents unnecessary wear on the attachment while achieving the desired shape or finish.
- Don’t Force It: Let the tool do the work. Applying too much pressure can lead to overheating and premature wear of the attachment.
Maintaining Grinding Attachments
Caring for your Dremel grinding attachments can drastically enhance their lifespan and effectiveness. Here’s how to ensure they remain in prime condition:
- Clean Regularly: After use, take a moment to clean the attachment. Dust and debris can build up and affect performance. A simple brush or compressed air can do wonders here.
- Inspect for Wear: Check your attachments for signs of wear such as cracks or dull edges. Replace them when necessary to ensure optimal grinding results.
- Store Properly: Avoid tossing your attachments into a drawer. Instead, store them in a dedicated case or holder. This prevents damage and keeps them organized.
By following these best practices, you not only enhance your work with Dremel attachments but also cultivate a safer and more efficient crafting environment. Keeping safety, technique, and maintenance at the forefront will undoubtedly lead to exquisite outputs, whether you're tackling small projects or larger constructs.
Comparing Dremel Attachments to Other Tools
When it comes to grinding or shaping materials, users often find themselves at a crossroads when they need to compare various tools. Understanding how Dremel attachments stack up against other options in the market provides clarity, giving users a better grasp of what they truly need for their projects. In this section, we will explore the merits of Dremel tools in relation to traditional grinders and highlight the unique versatility they bring.
Dremel vs. Traditional Grinders
Using a Dremel tool for grinding work is often favored over traditional grinders for several reasons. Firstly, it's compact. Traditional grinders can be bulky and require ample space, which can be a real hassle for hobbyists working in small workshops or even at the kitchen table. On the other hand, Dremel tools are manageable, allowing for easy handling.
Similarly, the speed control feature in Dremels offers users more precision when working on intricate projects, something that can't always be achieved with standard grinders. Traditional grinders usually run at a fixed speed, which may be suitable for heavy-duty tasks but can be cumbersome when precision is needed.
Another factor is the variety of attachments available for Dremel tools. With a range of grinding stones, polishing bits, and cutting wheels, users can choose the right accessory for their specific needs. In contrast, traditional grinders typically come with limited options, often forcing you to settle for dimensions that may not meet your requirements.
"In the world of grinding, flexibility and adaptability can make all the difference in achieving quality outcomes."
Versatility of Dremel Tools
One of the standout features of Dremel tools is its versatility. Unlike traditional grinders, which can be quite specialized, a Dremel can seamlessly transition from grinding to cutting, engraving, and polishing with the right attachment. This is particularly beneficial for rock and fossil collectors who may require a spectrum of functions from a single tool.
Here are a few key considerations that speak to their versatility:
- Multi-functional Use: The ability to change attachments easily enables the Dremel tool to cater to various tasks, making it an essential for any toolkit.
- Accessories Galore: Users can select from a wide array of attachments, from tungsten carbide bits for tough materials to soft, felt polishing pads.
In sum, choosing a Dremel tool gives you the freedom to explore different creative avenues, making it a top contender for anyone who values diverse functionality. Whether you're smoothing rough surfaces on fossils, engraving delicate patterns onto stones, or polishing your prized collectible, Dremel attachments allow you to do it all with ease and precision, steering clear of the limitations imposed by traditional grinding equipment.
Common Mistakes with Dremel Grinding Attachments
Using Dremel grinding attachments effectively can be a game changer for anyone involved in detailed work, yet many individuals, both new and experienced, fall into common traps that hinder their best efforts. Recognizing these mistakes is essential for maximizing both efficiency and precision in your crafting tasks. By understanding what not to do, you can avoid pitfalls that can lead to frustration, damage to materials, or even injury. This section aims to shed light on such errors and offer ways to sidestep them, ultimately enhancing the quality of your work.
Overheating the Attachment
One prevalent mistake is allowing the Dremel attachment to overheat during use. This generally happens when the tool is run for prolonged periods or placed under too much pressure.
When attachments like grinding stones reach excessive temperatures, it compromises their effectiveness. For instance, an overheated aluminum oxide grinding stone can become dull quicker, requiring more frequent replacements and wasting both time and resources. Plus, it can result in unwanted changes to your workpiece, like burning or melting.
Here are some tips to avoid overheating:
- Interval Work: Instead of grinding continuously, take breaks every few minutes. This allows the attachment to cool down, maintaining its integrity.
- Moderate Pressure: Let the attachment do the work. Pressing too hard can generate excess friction and heat.
- Use Cooling Techniques: Some crafters utilize a light spray of water or aromatherapy oil to cool attachments while working, but be cautious with electrical components.
"Avoid heat build-up. If you feel it’s getting too warm, pause before damage occurs."
This approach of mitigating heat build-up not only prolongs the life of your grinding tools but also ensures a smoother finish on your projects.
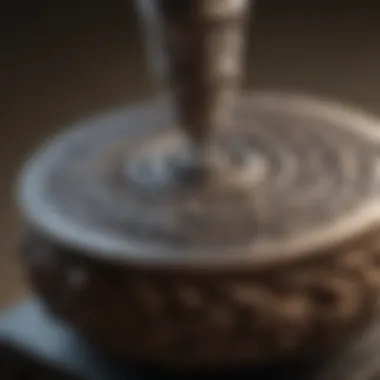
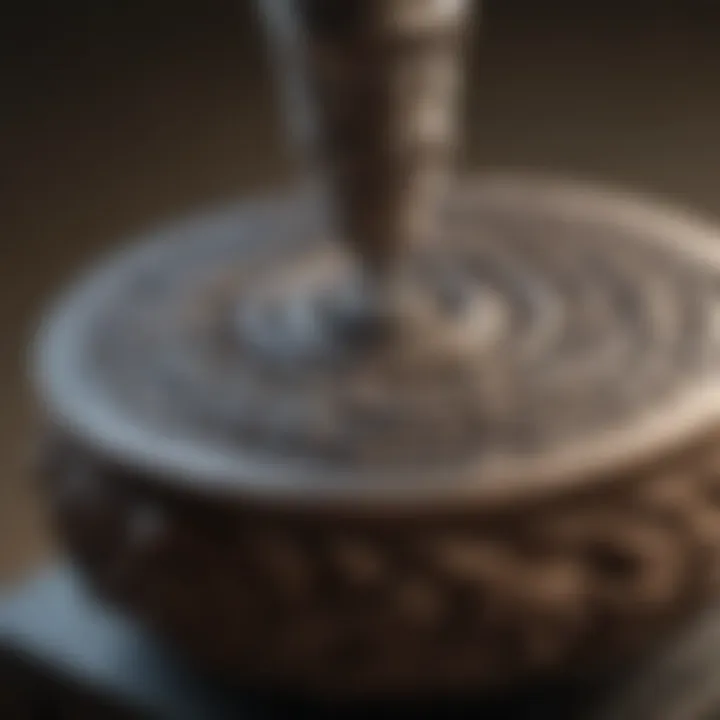
Incorrect Speed Settings
Another common blunder involves using the wrong speed settings for specific grinding tasks. Dremel tools are designed with adjustable speed controls that cater to a variety of materials and tasks. Ignoring this aspect can lead to insufficient grinding or excessive wear on your attachments.
For instance, using a high speed on a delicate material like wood can easily lead to splintering, while employing a low speed on hard materials like metal may result in an ineffective grind.
Here are some pointers for selecting the right speeds:
- Know Your Material: Different materials require different speeds. Soft woods typically can handle higher speeds, whereas more delicate materials, including certain plastics, need gentle, slower movements.
- Start Slow: If unsure, begin at a lower speed and gradually increase it until you find what's most effective.
- Adjust Based on Feedback: Pay close attention to how the attachment and material react. If you notice burning or uneven surfaces, it’s a sign the speed needs adjusting.
In the realm of craftsmanship, ensuring your settings are in line with the specific needs of your project can greatly contribute to an efficient workflow and optimum results.
Enhancing Precision in Detail Work
When it comes to fine crafting and detailed projects, precision is key. Whether you're working on delicate jewelry or intricate rock and mineral displays, the slightest margin of error can spell disaster. Dremel grinding attachments allow for an exceptional level of control, making tasks easier for both the amateur and the seasoned professional. In this section, we will explore how enhancing precision works, as well as how to utilize the appropriate tools for the job.
Using Collets and Chuck Systems
Collets and chuck systems are fundamental for maintaining precision in detail work. A collet securely grips the attachment and minimizes vibration while the tool is in motion. This is particularly important when grinding fine details or intricate designs in materials, since even a slight shake can lead to uneven surfaces or unwanted marks.
When selecting a collet, it’s essential to choose the right size for the bit you’re using. Using a collet that is either too large or too small can compromise the grip and lead to inaccuracies in your work. Dremel offers a variety of collet sizes which can accommodate bits ranging from 1/32 inch to 1/8 inch. Always ensure that the collet is properly tightened before beginning work, as this will not only improve precision but also enhance safety.
Another popular grip mechanism is the chuck system. Unlike collets, a chuck allows you to quickly swap between attachments without the need to replace or adjust different collets. However, ensure that the chuck is fully tight on the attachment to avoid slippage during operations. Using either system effectively can make a world of difference in your overall work quality.
Adjusting Speed for Fine Work
Another crucial factor in achieving precision with Dremel attachments is speed adjustment. Many Dremel models allow you to easily regulate the rotational speed of the tool. This feature becomes particularly significant when you're engaged in delicate grinding tasks.
Using a lower speed can help you control the amount of material removed and reduces the risk of overheating, which can damage both your work and the grinding attachment. For instance, when working on softer stones or fine metal details, setting the tool to a slower speed allows for more accurate work while minimizing the chance for chipping and cracks.
Conversely, for tougher materials, a higher speed may be warranted. However, it's important to gauge your approach based on the material's hardness. Finding the sweet spot often requires a little trial and error, yet once you do, you’ll notice a significant improvement in the quality of your craftsmanship.
„Precision in crafting is not just a skill but an art form. The right tools, used wisely, can create masterpieces in the tiniest of details.”
In summary, enhancing precision in detail work through the effective use of collets, chuck systems, and speed adjustments can significantly elevate your craft. Dremel grinding tools offer versatile options that are particularly advantageous for enthusiasts and professionals alike.
Innovative Techniques with Dremel Attachments
In the world of crafting and fine detailing, utilizing innovative techniques with Dremel grinding attachments can drastically elevate the quality of one's work. These techniques not only save time but also allow for a higher degree of creativity and precision. Understanding these methods is vital, especially for enthusiasts and professionals who wish to explore the full potential of their Dremel tools.
Creating Textures and Patterns
Harnessing textures and patterns is a quintessential part of any detailed project, particularly for rock and fossil collectors aiming to enhance the visual appeal of their specimens. Dremel attachments lend themselves well to this task, providing an array of options to create effects that range from subtle to striking.
To create intricate textures, you might opt for diamond grinding wheels or specialized carbide burs. Applying different pressures while working the attachment can yield gradients in texture, resulting in pieces that have depth and character. Here are some techniques to consider:
- Layering Techniques: Start by creating a foundational layer with a coarse attachment before gradually switching to finer ones. This transition results in a gradual reveal of the details beneath.
- Directional Scraping: By altering the direction of your movements, you can create unique patterns that enhance the item's surface. For example, using a rotary bit in a circular motion can create beautiful swirled designs.
- Incorporating Stencils: Use stencils during the grinding process for uniform textures. This method is particularly useful for creating repetitive patterns, aiding in achieving professional results.
This variety in techniques allows collectors to express their individuality in each piece they work on. The beauty lies in the creativity; some even experiment with combining different attachments to achieve a unique finish.
Combining Grinding with Polishing
When looking to achieve a polished finish on your rocks or fossils, it's crucial to understand how to effectively combine grinding and polishing techniques. Each step plays a unique role in the transformation of a rough specimen into a smooth, aesthetically pleasing piece.
Starting with a grinding attachment prepares the surface. Depending on what you're working with, the right choice of attachment based on material hardness is key. Once the initial grinding phase is done, switching to a polishing bit, such as felt polishing wheels, can refine the surface even further. Here are some steps to efficiently combine these processes:
- Begin with Rough Grinding: Use a heavy-duty grinding bit to remove any heavy scratches or irregularities.
- Smoothing Out: Transition to a finer grit attachment, gradually working up to smoother surfaces.
- Polishing Phase: Once satisfied with the smoothness, use a polishing compound or wheel, preferably at a lower speed to prevent overheating. This is especially important to maintain the integrity of delicate specimens.
- Final Touches: For a perfect shine, sometimes a mix of grinding and polishing can be done with the right attachments, giving the surface a distinct luster.
Using these combined techniques can set your work apart, providing a lustrous finish that can make your collection stand out. The transition between grinding and polishing highlights the versatility of Dremel tools, allowing users to adapt based on individual project requirements.
"The key to unlocking the potential of Dremel grinding attachments lies in understanding how to blend various techniques together to create true works of art."
By embracing these innovative strategies, collectors can elevate their crafting game, turning simple pieces into masterpieces of texture and shine.
Culmination: Mastering Dremel Grinding Attachments
In the vast realm of crafting and restoration, understanding how to expertly wield Dremel grinding attachments can be a game changer. This guide navigates intricacies that go beyond mere tool usage; it focuses on the principles that will elevate both quality and precision in your projects. Whether you're polishing a gemstone, refining a model, or restoring a cherished collectible, mastery of these attachments turns tasks from daunting to achievable.
Continuing Education and Resources
To truly grasp the nuances of Dremel grinding attachments, one must embrace a mindset of continuous learning. Resources are plentiful, covering everything from basic tutorials to advanced techniques. Here are avenues worth exploring:
- Forums and Community Groups: Websites like Reddit provide platforms for enthusiasts to share experiences, tips, and challenges.
- YouTube Tutorials: Visual guides are invaluable for grasping techniques. Channels focused on crafting often showcase the intricate uses of Dremel tools.
- Books and Magazines: Specialty publications may feature comprehensive sections on tool utilization, fostering a more detailed understanding of different grinding attachments and their applications.
- Workshops and Classes: Local community colleges or crafting stores may offer hands-on workshops. These sessions give practical insights, helping you see the effects of different attachment choices in real time.
Each of these resources provides ongoing support to refine your skills and broaden your repertoire.
Final Thoughts on Usage and Applications
As we wrap up this exploration of Dremel grinding attachments, remember that the journey is as important as the destination. The right technique, combined with appropriate attachments, significantly broadens your capabilities. Here are a few key takeaways:
- Practice Makes Perfect: Like any skill, mastering your Dremel takes time. Regular practice allows familiarity with different attachments, enhancing your precision and control.
- Know Your Task: Always consider the specific job at hand. Matching the right attachment to your material is critical for success. Some tasks may call for a fine finish, while others are better suited for more aggressive grinding.
- Safety First: Never underestimate the importance of safety measures. Proper gear and mindfulness can prevent mishaps.