Cutting and Polishing Collectibles: A Complete Guide
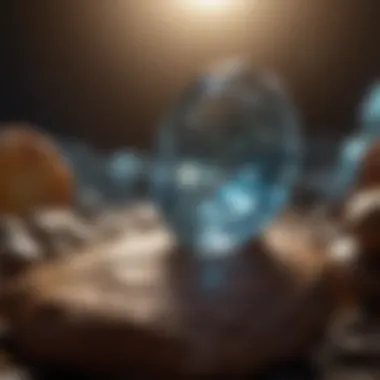
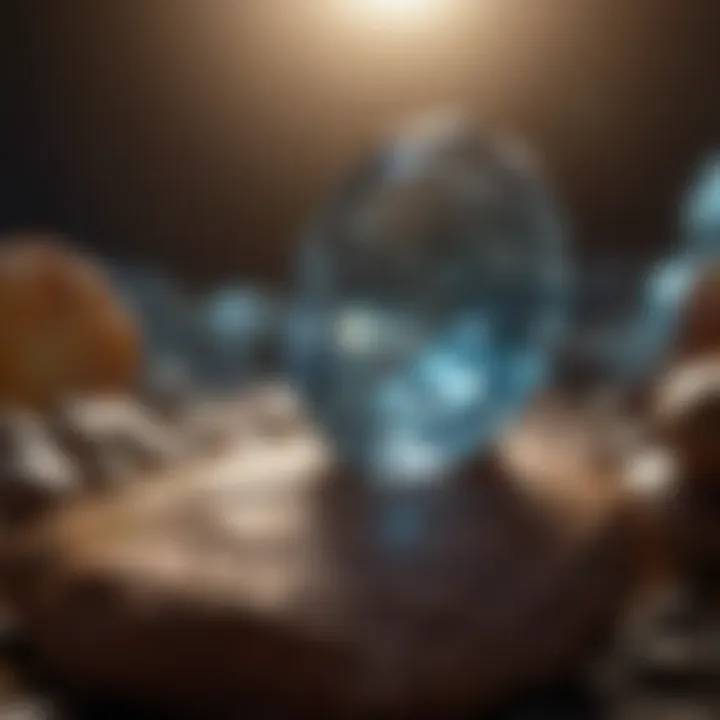
Intro
The world of collectibles is vast and diverse, encompassing a cornucopia of materials, including stunning stones and captivating fossils. Engaging with these items can be a fulfilling pursuit. However, achieving their full potential—both in beauty and value—requires a deep understanding of the cutting and polishing processes. In this guide, we will explore the essential techniques, tools, and scientific principles governing these practices. By doing so, we will provide collectors and enthusiasts with a foundation to enhance their treasures.
Topic Overview
Definition of the collectible/rock/fossil
Collectibles generally refer to items prized by enthusiasts for their unique characteristics, historical significance, or aesthetic appeal. In the context of stones and fossils, these may include raw minerals, polished gemstones, or prehistoric remnants. Stones, for example, are often classified by their hardness, luster, and formation, whereas fossils are categorized based on the type of organisms they represent and their geological age.
Brief history and significance
The practice of cutting and polishing stones dates back thousands of years. Ancient civilizations utilized these techniques not only for aesthetic purposes but also for functional items. For instance, polished stones have been used as tools and adornments throughout history. The significance of fossils further elevates their appeal; they serve as reminders of Earth's history and the evolution of life. Collectors often seek to possess these pieces of the past, enhancing their significance through careful preservation and improvement of appearance.
Identification and Classification
How to categorize items
Identifying and classifying stones and fossils is vital for collectors. Here are some tips to categorize your items:
- Type of Material: Differentiate between minerals, crystals, fossils, and more.
- Geological Age: For fossils, knowing the era can enhance understanding.
- Appearance: Classification based on color, pattern, and texture can help determine value.
Tips for identifying key features
To effectively identify key features in your collectibles:
- Examine Surface Texture: Look for glossy finishes or natural patterns.
- Use Educational Resources: Books and online databases, such as Wikipedia or Britannica, can provide in-depth knowledge.
- Seek Expert Opinions: Joining communities, like those on Reddit, can offer access to experienced collectors and professionals.
"Knowledge of your collectible’s origin and characteristics contributes to its value and story."
By grasping the foundational aspects of cutting and polishing, collectors can significantly elevate their experience and investment in stones and fossils. Each carefully enhanced piece not only reflects a higher aesthetic value but also encapsulates a stronger narrative—intriguing both the collector and the wider audience.
Intro to Cutting and Polishing
Cutting and polishing are fundamental processes in the world of collectible stones and fossils. These techniques not only shape raw materials but also enhance their aesthetic appeal and market value. Collectors must grasp these processes to appreciate the full potential of their materials, whether for personal collection or sale.
Defining Cutting and Polishing
Cutting involves removing material from a stone or fossil to achieve a desired shape or form. This process is essential as it dictates the overall appearance of the collectible. The cutting can be done through various methods, such as sawing, grinding, or chiseling, depending on the material's hardness and the desired outcome.
Polishing, on the other hand, is the final stage. It involves smoothing the surface to a high sheen, often using specialized polishing compounds and tools. The goal of polishing is to bring out the natural beauty of the collectible, revealing its colors and patterns while eliminating any blemishes that might detract from its visual appeal.
Importance in Collecting
Understanding cutting and polishing is vital for collectors for several reasons. Firstly, the quality of cutting can significantly affect the value of a piece. A poorly cut stone may lack aesthetic appeal, making it less desirable in the market. On the contrary, a well-cut stone enhances the visual allure and can fetch a higher price.
Secondly, polishing transforms a rough piece into something extraordinary. It not only showcases the natural features of the stone or fossil but also makes it more durable. Properly polished collectibles are less susceptible to damage and degradation over time.
Moreover, mastering these techniques allows collectors to take control of their pieces. They can improve their own collections or even create items for resale. Thus, the processes of cutting and polishing are not mere technical skills but pivotal tools in the collector's arsenal.
"A thorough understanding of cutting and polishing can convert the mundane into the magnificent."
In summary, grasping the intricacies of cutting and polishing is indispensable for anyone in the realm of collectibles. It leads to informed decisions, better preservation, and ultimately, a more valuable collection.
Materials Used in Cutting and Polishing
Understanding the materials used in cutting and polishing is crucial for anyone interested in enhancing collectibles such as stones and fossils. The choice of materials affects not only the process but also the final appearance and value of the items being worked on. Selecting the right materials can make a significant difference in achieving optimal results.
Types of Stones
Different types of stones have unique characteristics that influence their cutting and polishing needs. Commonly used stones include:
- Agate: Known for its vibrant colors and banding, agate is relatively easy to cut and polish, making it popular among collectors.
- Amethyst: This purple quartz variant is sought after for its beauty but requires careful handling to prevent breakage during cutting.
- Obsidian: A naturally occurring volcanic glass, obsidian can achieve a brilliant shine when polished but must be handled with precision due to its brittleness.
- Jade: Valued for its cultural significance and beauty, jade can be more challenging to work with than other stones due to its toughness, requiring specialized techniques and tools.
Each type of stone has its own set of challenges and advantages during the cutting and polishing process. Recognizing these characteristics helps collectors to better prepare and approach the work.
Metals and Other Materials
In addition to stones, various metals and materials are often utilized during the cutting and polishing processes. These include:
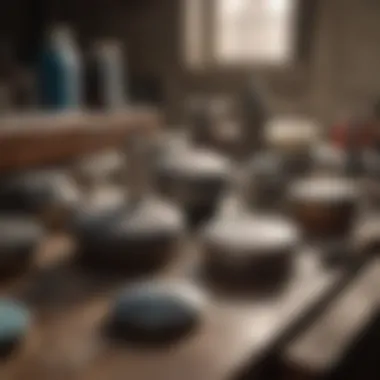
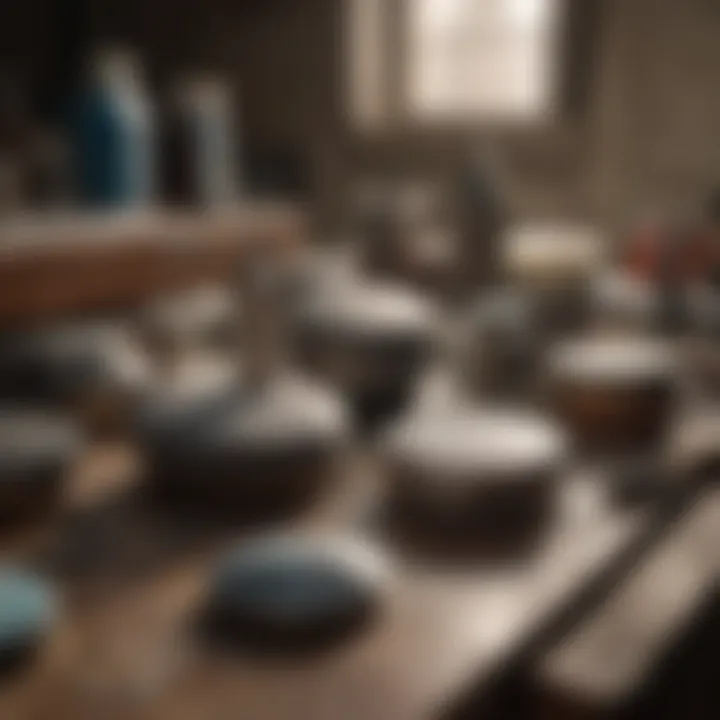
- Diamond: Used primarily in cutting tools and saws, diamonds offer unparalleled durability and precision, making them essential for working with harder stones.
- Cobalt and Steel: Used in many cutting tools, these metals are common choices due to their strength and resistance to wear. Regular maintenance of these tools is crucial for optimal performance.
- Polishing Compounds: Substances such as cerium oxide or tin oxide assist in the polishing process, providing a fine finish on surfaces after cutting.
- Abrasives: Materials like sandpaper or diamond pastes come in various grits, allowing for progressive smoothing and polishing of surfaces.
The interplay of these materials significantly affects the outcome of the cutting and polishing processes. Understanding the characteristics and appropriate applications of each material is vital for success in enhancing collectibles.
Tools of the Trade
The effectiveness of cutting and polishing stones and fossils heavily depends on the tools employed in these processes. Utilizing the right tools can significantly enhance the quality of the finished product. Collectors need to invest in equipment that ensures precision and efficiency. Proper tools also lead to greater control during each step, allowing for more intricate designs and finishes. In this section, we will focus on two primary categories of tools: cutting tools and polishing equipment. Each of these categories includes specific tools that provide unique contributions to the art of cutting and polishing.
Cutting Tools
Diamond Saws
Diamond saws are essential for cutting various types of stones and fossils. A significant aspect of diamond saws is their durability. They are designed with diamonds embedded in the blade, a feature that allows for clean and precise cuts. This quality makes them highly sought after by those in the collecting community. Diamond saws offer a level of accuracy that other types of cutting tools struggle to achieve.
One unique feature of diamond saws is their ability to handle tough materials like quartz and agate. However, they can be more expensive than traditional saws, which may be a consideration for some collectors. Still, their longevity and cutting efficiency often justify the higher cost.
Lapidary Saws
Lapidary saws are popular for both beginners and experienced collectors. These saws excel at cutting softer stones and are particularly well-known for their versatility. The key characteristic of lapidary saws is their ability to be adjusted for different cutting speeds, providing users with flexibility during the cutting process. This attribute makes lapidary saws a favorable choice for several types of projects.
A unique feature of lapidary saws is their size; they are generally more compact than diamond saws, making them suitable for hobbyists with limited workspace. Nevertheless, lapidary saws may not be ideal for harder materials, which could limit their use in more ambitious projects.
Polishing Equipment
Polishing Wheels
Polishing wheels play a critical role in achieving the final sheen on stones and fossils. These wheels are typically composed of various materials that contribute to the polishing process. The key advantage of using polishing wheels is their efficiency in achieving a smooth surface. They can adapt to different materials, ensuring versatility in their applications.
A unique feature of polishing wheels is their ability to be used with different polishing compounds, catering to various levels of gloss and finish. However, the choice of wheel needs to align with the material being polished. Some polishing wheels may wear quickly, which is a disadvantage in prolonging the overall efficiency of polishing sessions.
Buffers and Grinders
Buffers and grinders are indispensable for refining the finish of a piece. Buffers add the final touch by creating a high-gloss surface, whereas grinders are used earlier in the process to smooth rough edges and surfaces. The key characteristic of buffers is their ability to polish larger areas quickly, while grinders are designed to handle more intensive shaping tasks.
One unique feature of buffers is their speed control. This allows users to adjust the speed according to the needs of the specific material being polished. On the downside, the fast speed may sometimes lead to over-polishing if not handled carefully. Grinders, while effective, may consume more time and require a steadier hand to ensure the shape is maintained throughout the process.
"Selecting the right tools is fundamental to maximize the potential of your collectibles."
The Cutting Process
The cutting process is a critical step in the enhancement of collectibles, particularly stones and fossils. Effective cutting lays the groundwork for successful polishing. The precision of a cut greatly influences both the aesthetic quality and the structural integrity of the material. Without a proper cutting technique, the potential beauty of a stone may remain hidden, and the overall value can diminish.
Preparing the Material
Before any cutting occurs, preparing the material is essential. This preparation involves several stages:
- Selection of the stone or fossil: Identify the specimen's aesthetic and market potential. Each material has unique properties that affect cutting techniques.
- Cleaning: Remove any dirt or debris. A clean surface allows for a clearer view of the material's internal structures, which is crucial for determining cutting patterns.
- Analyzing Structure: Inspect the object for any flaws, such as cracks or inclusions. Understanding these natural weaknesses helps in planning cuts that minimize damage.
- Stabilization: For some softer fossils or fragile stones, stabilization with adhesives may be necessary to prevent chipping during cutting.
Making the Cut
The act of cutting should not be taken lightly. It requires focus and expertise. Various techniques and tools come into play during this stage. Here are some important elements to consider:
- Tool Selection: Choose the right cutting tool based on the material's hardness. Diamond saws and lapidary saws are common for stones.
- Orientation: Determine the best orientation for the cut. Positioning plays a significant role in maximizing the visual appeal of the final product.
- Technique: Employ a consistent speed and pressure. Uneven application can lead to jagged edges or poorly aligned cuts.
A well-executed cut transforms a rough specimen into a piece with potential value.
Post-Cut Treatments
Once cutting is complete, post-cut treatments are essential for further enhancing the material. The initial cut can leave rough edges and may expose vulnerabilities, which must be addressed. Here are the key treatments:
- Smoothing Edges: Using grinding wheels or finer saws helps to refine edges, preparing the piece for polishing.
- Inspection: After cutting, inspect the specimen for any new flaws that may have developed during the cutting process. Addressing these promptly is crucial.
- Sealants: Certain materials benefit from the application of sealants to protect against environmental damage.
- Cleanup: Remove any residual dust or particles. A clean working surface enhances the effectiveness of the next stages, especially polishing.
Proper cutting is not merely about shaping; it is an art that requires understanding of the material and precision in execution.
The Polishing Process
The polishing process is a critical phase in enhancing collectibles, particularly stones and fossils. It is the final step that elevates the appearance of the material, maximizing its aesthetic appeal and marketability. A well-polished collectible can significantly influence its perceived value. Collectors often prioritize this stage because it not only improves the look but also gives a sense of care and craftsmanship associated with the piece. Polishing can also reveal hidden details, enhancing personal enjoyment and appreciation.
Setting Up for Polishing
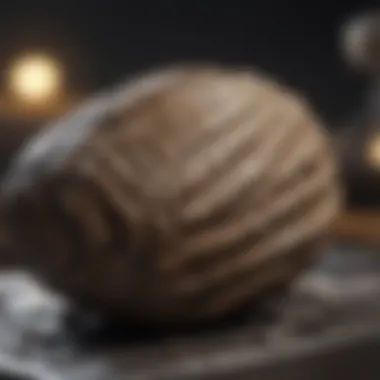
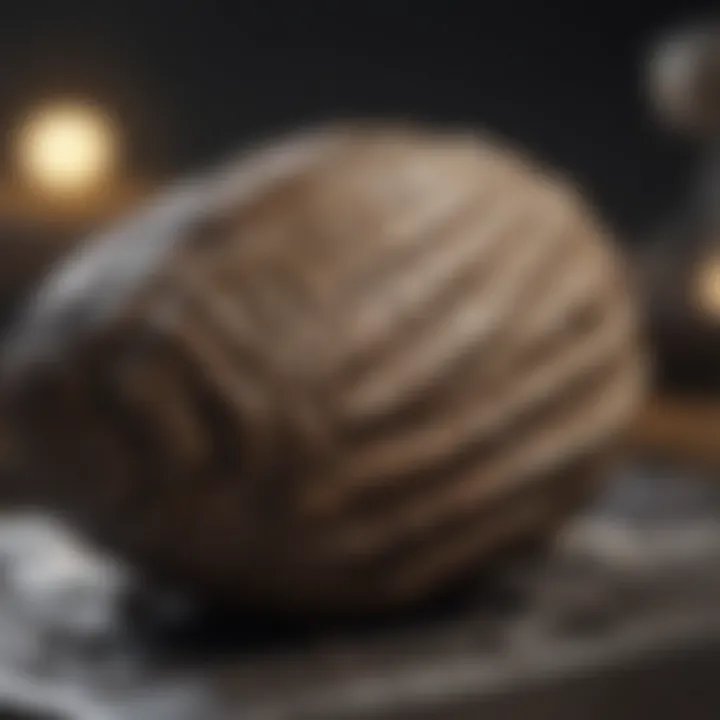
Before embarking on polishing, a proper setup is essential. This setup includes selecting the right workspace and gathering necessary tools. A clean, well-lit area free from distractions ensures focus and precision during the process.
- Workspace Considerations: Choose a flat, sturdy surface. Consider soundproofing if working with noisy machines.
- Safety Equipment: Always use protective gear, including goggles and masks. This protects against flying debris and fine dust.
- Tool Arrangement: Organize materials and tools systematically. This aids in efficiency and helps maintain a smooth workflow.
Having everything in place before starting prevents interruptions and allows full attention to the polishing technique itself.
Techniques for Effective Polishing
Effective polishing involves specific techniques that enhance the final product. When applied correctly, these techniques can create a finish that highlights the collectible's best features.
Using Polishing Compounds
Using polishing compounds is fundamental to achieving a bright, reflective surface. These compounds contain tiny abrasive particles that smooth out imperfections and enhance gloss. One key characteristic of these compounds is their ability to work with various materials, ensuring versatility in polishing.
- Benefits: Polishing compounds optimize the material’s shine. They are simple to use and often yield quick results.
- Drawbacks: However, overuse can lead to excessive removal of material, so care must be taken to use them judiciously.
Polishing compounds, such as cerium oxide or tin oxide, remain popular choices due to their effectiveness across different surfaces. Their application is typically done using a soft cloth or specialized pads, contributing to a seamless finish.
Adjusting Speed and Pressure
Adjusting speed and pressure during polishing is essential to achieve desired results. The right combination affects the material's surface texture significantly. Typically, slower speeds are better for finer finishes, while higher speeds are useful for removing scratches more expeditiously.
- Benefits: Proper adjustment reduces the risk of overheating the material, which can damage it. It also enables better control over the polished surface’s texture and gloss level.
- Drawbacks: Not adjusting these factors can lead to inconsistent results or even harm to the collectible, highlighting the importance of attention to detail.
In practice, experimenting with various settings on a small piece before committing can lead to optimum outcomes. Final touches often require finesse, so finding the right balance is key to a successful polishing venture.
Best Practices for Cutting and Polishing
In the realms of cutting and polishing stones and fossils, the adherence to best practices is not merely a recommendation but a necessity. Techniques that appear trivial can significantly impact the final appearance and value of a piece.
The methodology employed during these processes can ensure not only aesthetic beauty but also the integrity of the materials. When collectors embrace these best practices, they enhance the likelihood of producing pieces that are not only visually appealing but also maintain their worth over time.
Safety Considerations
When engaging in cutting and polishing, prioritizing safety cannot be overstated. The tools used can pose various risks, including cuts and inhalation of harmful dust. Here are some critical safety measures:
- Protective Gear: Always wear safety goggles and gloves to shield against sharp edges and flying debris. Dust masks can prevent inhalation of fine particles.
- Ventilation: Ensure that the workspace is well-ventilated. Utilizing tools like wet saws can minimize dust creation, which helps in maintaining air quality.
- Safe Handling: Be mindful of how materials are handled. Slippery stones or improperly secured pieces can lead to accidents.
These practices are vital, as neglecting them could lead to injury or damage to collectible items.
Quality Control
Quality control is essential in the cutting and polishing processes. It ensures that each step taken leads to the desired outcome without compromising on quality. The following points highlight key aspects of maintaining quality:
- Inspection Instantly: After the cutting process, inspect the edges and surfaces closely. Look for chips, cracks, or uneven cuts that could affect the final appearance.
- Consistent Polishing: The polishing phase should aim for uniformity. Use the same technique and pressure throughout to avoid inconsistent finishes. Rotate pieces frequently to ensure even exposure to the polishing medium.
- Final Evaluation: Once polishing is complete, perform a thorough evaluation in good lighting. This includes checking for scratches or dull spots that may require additional attention.
Ensuring quality control is paramount, as a well-finished piece will stand out in any collection and potentially command a higher market value.
"Quality is not an act, it is a habit." - Aristotle
By implementing strict safety protocols and rigorous quality control, collectors and enthusiasts can protect both themselves and their investment, creating stunning pieces that resonate in aesthetics and value.
Common Pitfalls in Cutting and Polishing
Cutting and polishing collectibles is an art that requires both skill and knowledge. However, many enthusiasts face challenges due to certain misconceptions and neglectful habits. Understanding common pitfalls in cutting and polishing can help collectors avoid costly mistakes and enhance their collectible items effectively. Each pitfall has specific elements that can significantly affect the quality and value of the finished products. Thus, identifying these issues is key to achieving optimal results in this intricate process.
Overestimating Material Durability
Many collectors assume that all stones and fossils can withstand extensive cutting and polishing without damage. This is not the case. Different materials have varying degrees of hardness and fragility. For example, a soft stone like alabaster can easily be scratched or chipped compared to a harder stone such as granite. Overestimating the durability of a material can lead to irreversible damage during processing.
Key considerations include:
- Assessing hardness: Utilize the Mohs scale of mineral hardness to evaluate how a stone behaves under tools.
- Testing small samples: Before starting on a valuable piece, experiment with small or less valuable samples to observe how it responds to cutting tools and polishing methods.
- Understanding flaws: Inspecting for natural cracks or inclusions is vital. Neglecting such characteristics can lead to significant splits during cutting.
In short, it’s important to remember that not all materials are created equal in the context of cutting and polishing.
Neglecting Equipment Maintenance
Equipment maintenance plays a pivotal role in achieving high-quality results when cutting and polishing. Familiarity with tools is not enough; regular upkeep is essential for performance and safety. Many collectors overlook this aspect, which can lead to suboptimal cutting results and even accidents.
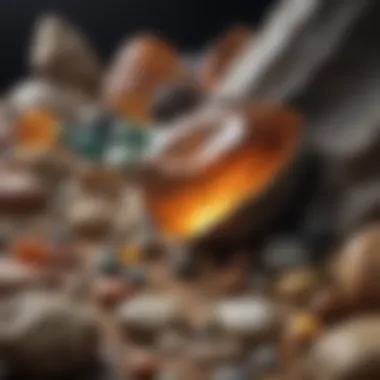
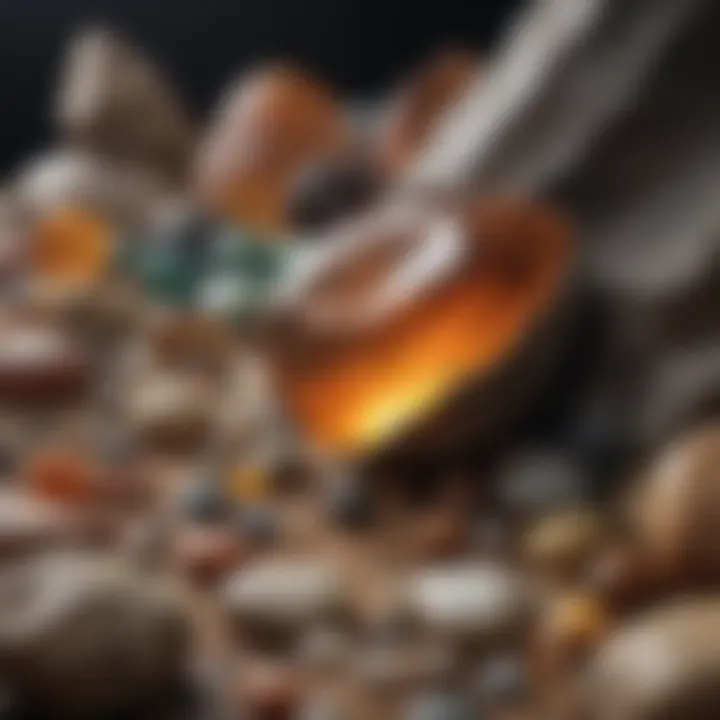
From diamond saws to polishing wheels, each tool requires care.
- Regular cleaning: Dust and debris can accumulate on equipment, hindering performance and accuracy. A quick wipe down after each session can keep tools in top condition.
- Sharpness checks: Dull blades or worn-down polishing pads result in inefficient cutting and polishing. Inspect and replace tools as needed to maintain peak effectiveness.
- Calibration: Ensuring that machines are properly aligned can avoid unnecessary wear and improve cutting quality. Misalignment can cause uneven surfaces and lead to further work down the line.
Maintenance is an ongoing consideration that can save time, effort, and resources over time. Paying attention to this critical aspect ensures that tools remain effective, which directly impacts the quality and value of the finished product.
Evaluating Finished Products
Evaluating finished products holds significant importance in the realm of cutting and polishing collectibles. This section provides insight into what defines a successful refinement process and how collectors can recognize quality in their stones and fossils. Understanding the evaluation criteria not only enhances personal collections but also informs decisions when engaging in the market, where aesthetics and perceived value are paramount.
An efficient evaluation process involves multiple factors, including visual appeal, craftsmanship, and market considerations. Each of these elements contributes to determining both the aesthetic and monetary value of the collectible.
Factors Affecting Aesthetics
The aesthetics of cut and polished collectibles is a key indicator of their quality and appeal. Several specific factors play a role in shaping the overall look of the finished product:
- Surface Finish: The smoothness and shine achieved during polishing significantly affect visual appeal. Any blemishes or scratches can detract from its beauty.
- Color and Clarity: The vibrancy of colors and overall clarity of the materials will impact how they are perceived visually. Higher clarity and vivid colors typically command higher interest.
- Shape and Proportion: The final shape should highlight the natural features of the material. A well-proportioned piece, emphasizing its unique characteristics, will always attract more attention.
- Pattern and Texture: Unique patterns and the texture of the surface can enhance visual richness, making the piece more desirable to collectors.
In assessing these elements, collectors can identify both strengths and weaknesses of their pieces. A well-evaluated collectible can lead to better care practices and improved preservation strategies as well.
Market Value Assessment
The market value assessment of finished products is a vital step in understanding the investment potential of collectibles. Several core factors influence how market value is determined:
- Rarity: Unique stones or fossils that are rare tend to fetch higher prices. Scarcity can greatly enhance desirability among collectors.
- Condition: The condition of the collectible is an essential consideration. Items that are well-maintained and without damage usually command a premium.
- Historical Significance: Items that possess historical or geological significance often hold higher value. Provenance can play a critical role in justifying the price.
- Market Trends: Understanding current market trends can provide insights into what collectors are currently seeking. This can guide decisions in terms of buying and selling.
Evaluating market value requires a thorough analysis of these factors. Collectors should stay informed and continuously update their knowledge on market conditions. An informed approach not only enhances personal collections but can lead to profitable transactions when selling.
Overall, meticulous evaluation helps collectors make prudent decisions regarding acquisition, preservation, and sale of their collectibles.
Preservation Techniques Post-Polishing
The journey of cutting and polishing stones and fossils does not conclude with the formation of a visually appealing piece. To ensure that the enhanced collectibles retain their beauty and value over time, proper preservation techniques come into play. These techniques are crucial for collectors who treasure their pieces not just for their aesthetic charm but also for their potential monetary worth.
Preservation techniques are vital for maintaining the condition of polished items. Factors such as environmental exposure, handling, and storage greatly influence the longevity of these collectibles. Proper techniques can prevent damage, ensure longevity, and maintain their market value.
Storage Methods
Collectibles require specific storage conditions to avoid damage. Here are some effective storage methods:
- Use of Display Cases: Display cases with UV filters can protect items from harmful light exposure. This reduces the risk of fading and deterioration.
- Soft Storage Materials: When storing stones or fossils, wrap them in soft materials such as felt or microfiber cloth. These materials minimize scratching and friction.
- Controlled Environment: Aim for a stable environment with controlled humidity and temperature. Fluctuations in these conditions can lead to cracks and other structural issues.
- Avoiding Stack or Near Heavy Objects: Stacking can cause scratches and chips. It is advisable to store items in a way that prevents them from being compressed or bumped.
These methods play an instrumental role in preserving the integrity of your items. If done properly, they will retain their appeal and reduce the threat of deterioration.
Preventive Care Strategies
Preventive care is crucial to assure the long-term beauty and value of polished collectibles. Effective strategies include:
- Regular Cleaning: Lightly clean items with a soft brush or cloth to remove dust. Avoid harsh chemicals, as they can damage the surface.
- Periodic Inspections: Regularly check for signs of wear or damage. Early detection allows for timely repairs or adjustments.
- Controlled Handling: Always handle items with clean hands. Oils and dirt from hands can affect the surface finish over time.
- Avoiding Direct Sunlight: Store polished items away from direct sunlight to prevent color fading and heat-related damages.
Implementing these preventive strategies will not only enhance the life of your collectibles but also help preserve their value in the collection market. As with any crafted item, diligent care and attention to detail are paramount in safeguarding your investments.
Closure
The conclusion of this guide serves as both a reflection on the processes and a forward-looking statement about the evolution of cutting and polishing techniques in the collectibles realm. This section is pivotal, as it synthesizes crucial insights on enhancing the aesthetic and economic value of stones and fossils. Collectors need to recognize that proper cutting and polishing can significantly influence not only the appearance of their items but also their market demand.
Summary of Key Points
The cutting and polishing journey involves several stages, each contributing to the final product. The essential points to remember include:
- The significance of using the right tools and techniques for cutting.
- The importance of maintaining equipment to avoid damage to materials.
- Understanding the various types of materials that can be processed and how they react differently to cutting and polishing.
- The need for safety precautions to protect oneself while engaging in these tasks.
- Evaluating the final product based on aesthetics and market potential.
These elements collectively highlight that cutting and polishing are not merely mechanical tasks; they require an appreciation for the art and science involved in collectible enhancement.
Future Trends in Cutting and Polishing
As technology continues to advance, we can expect several emerging trends in cutting and polishing that will transform the landscape for collectors. Some noteworthy developments include:
- Innovative Tools: New cutting and polishing tools equipped with advanced features are becoming more accessible. These tools aim for precision while reducing the physical exertion required.
- Eco-Friendly Practices: Increased awareness of environmental impact is leading to the development of sustainable materials and processes. Collectors will likely see more options that align with eco-friendly practices.
- Virtual Reality Assistance: The integration of technology such as virtual reality could help collectors visualize the cutting and polishing process before making physical alterations to their collectibles.
- Community Involvement: Platforms like Reddit and Facebook are fostering a sense of community among collectors, encouraging the sharing of knowledge and techniques which will expand the collective understanding and appreciation of cutting and polishing.
Understanding where the industry is heading can provide collectors with an edge, enabling them to remain competitive and informed in a swiftly changing market.
"Knowledge in cutting and polishing can elevate a simple stone into a sought-after collectible."
In summary, the conclusion not only wraps up the guide but also inspires continued education and adaptation to new trends in cutting and polishing.