Selecting the Best Drills for Rock Applications
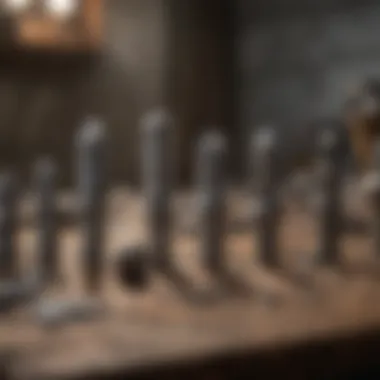
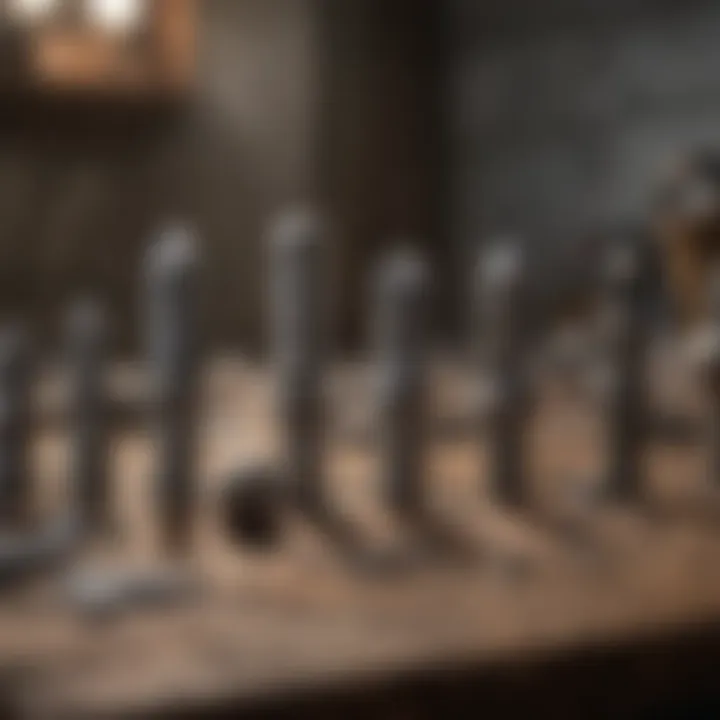
Intro
When embarking on a journey to drill into the rugged terrain of the earth, understanding the tools at your disposal is paramount. Selecting the right drill doesn’t just streamline tasks, it enhances the overall efficiency of your rock drilling projects. As enticing as the landscape may be, it is equally fraught with challenges. A well-chosen drill can mean the difference between a smooth operation and a frustrating endeavor, leaving you tangled in setbacks.
This guide presents a deep dive into the intricate world of rock drilling tools. We’ll explore various drills suitable for handling a diverse array of rock types. From the heavy-duty ones that chew through granite to more specialized options for softer sedimentary formations, knowing your tools provides a significant edge. The focus here will echo across both seasoned professionals and novices alike, cultivating a thorough understanding of the selection process.
Topic Overview
Understanding drills for rock applications is not merely about picking a tool; it’s about acknowledging the geology at hand and catering to it effectively. Let’s briefly lay down some groundwork:
Definition of Rock Drills
Rock drills are machines or tools specifically designed to penetrate hard surfaces like stone, concrete, or mineral deposits. These drills come in various forms and sizes, each tailored for unique drilling requirements, be it for construction, mining, or archaeological excavations.
Brief History and Significance
The inception of drilling tools dates back to ancient civilization, where rudimentary hand-held drills were leveraged to make holes in rocks. Fast forward to today, and we've witnessed innovations that have transformed the industry. The evolution from manual drilling techniques to advanced mechanized drills signifies immense progress.
This technological advancement is crucial because drilling plays an essential role in resource extraction, construction, and even scientific exploration. Understanding this evolution provides context on why selecting the appropriate drill is so important, as tools are continuously being refined to meet the demands of modern rock applications.
Identification and Classification
Selecting the right drill isn’t just a matter of preference—it’s about matching the tool with the geological challenges you are likely to encounter. Here’s how to navigate the selection process:
How to Categorize Drills
Recognizing different drill types can help substantially in making an informed choice. Common categories include:
- Rotary Drills: Best for penetrating hard rock, these utilize a rotating motion combined with some form of hammering.
- Impact Drills: These deliver rapid blows to break the rock as they drill, making them effective for tougher materials.
- Percussive Drills: Ideal for softer rocks, they operate with a percussion mechanism without the rotary function.
Tips for Identifying Key Features
When zeroing in on drills, certain features should catch your eye:
- Bit Type: The drill bit significantly influences performance. Options like tungsten carbide bits are customarily suited for extreme conditions.
- Weight and Portability: Depending on your application, a lightweight drill may be advantageous for maneuverability.
- Power Source: Electrically powered drills can perform consistently, while pneumatic drills offer unique benefits in specific environments like mining.
"Choosing the best drill is as much about the landscape as it is about the tools themselves. Know your terrain to find your fit."
Remember, a well-informed choice not only results in successful operations but can also enhance safety and reduce costs in the long run. Each decision made in selecting a drill is a step toward harnessing the full potential of your upcoming rock drilling pursuits.
Prelims to Rock Drilling
The world of rock drilling is not only technical, but it’s also a fascinating intersection of geology, engineering, and craftsmanship. For anyone involved in geological exploration, construction, or fossil excavation, understanding the nuances of rock drilling is crucial. This article aims to highlight the key steps in selecting the most suitable tools for various rock applications, and how these choices can significantly impact efficiency and outcomes.
When we talk about rock drilling, we are fundamentally discussing the methods and tools that make it possible to break through some of the Earth’s toughest materials. It’s an art that has evolved over centuries, and with it, a plethora of techniques and equipment come into play. From pulsating percussion drills to high-speed rotary machines, each tool offers unique advantages based on the type of rock and drilling objectives.
The importance of this topic can’t be overstated; selecting the right drill can save time, reduce costs, enhance safety, and ensure successful project completion. Moreover, the decision-making process involves various key factors such as the type of rock being drilled, the intended application, and even environmental considerations. It's like choosing the right key to fit into a lock — you wouldn’t use a hammer when what you need is a screwdriver.
Additionally, understanding rock as a material—the different types, surfaces, and densities—helps in making informed decisions. The historical development of rock drilling tools also shows how innovative solutions have risen in response to challenges across eras, influencing modern techniques and choices.
By diving into the nature of rock, the evolution of drilling practices, and the implications behind these choices, we equip our readers—especially those passionate about rock and fossil collecting—with knowledge that’s not just academic. Their endeavors, whether in research or hobbyist pursuits, depend significantly on the tools and methods they choose.
"Success is where preparation and opportunity meet." — Bobby Unser
In this context, preparation comes from understanding how to effectively select and utilize drilling equipment tailored to specific rock types and drilling objectives. This article sets the stage for deeper exploration into the different types of drills, key considerations in selection, and the practical aspects necessary for effective rock drilling.
Types of Drills for Rock
Understanding various types of drills is crucial for anyone looking to delve into the world of rock drilling. Different drills serve specific purposes and functions, which can dramatically affect both the efficiency and outcome of the drilling process. This segment aims to shed light on four primary drill types—each offering unique benefits and considerations that should be weighed before making a selection. By recognizing the nuances of rotary, percussion, diamond, and masonry drills, you’ll be better equipped to choose the right tool for your rock-related tasks.
Rotary Drill
Rotary drills are the workhorses of rock drilling operations. They employ a simple yet effective mechanism wherein a bit is turned in a circular motion to penetrate the rock. This type of drill is particularly effective in softer to medium-hard rocks.
Key Features:
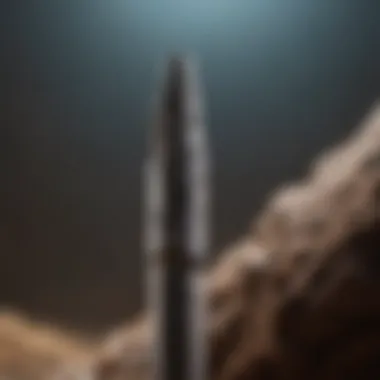
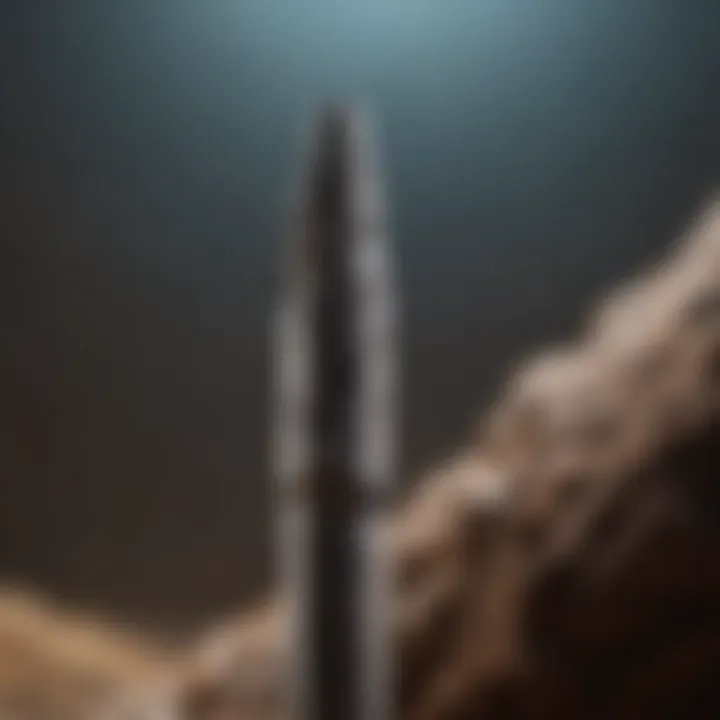
- Bit Design: The drill bit often features a sharp or pointed edge for efficient rock cutting.
- Versatility: Suitable for a wide range of applications including geological surveying and below-ground construction.
- Power Options: Rotary drills can be powered either electrically or by gas, enabling flexibility depending on the job's requirements.
Using a rotary drill can lead to a clean hole in rock structures, making them a preferred choice among rock and fossil collectors looking to excavate without causing excess damage to the geological layers.
Percussion Drill
In contrast, percussion drills take a different approach by combining rotating motion with high-impact blows. This is ideal for breaking through hard rock formations. The combination of rotational movement and hammering action allows these drills to shatter rock where simpler techniques may fail.
Key Advantages:
- Performance on Hard Rock: Especially useful for drilling through granite and other dense materials.
- Speed: Generally can drill faster than a rotary drill when dealing with tougher surfaces, drilling quickly while minimizing heat and wear.
When precision is paramount, using a percussion drill can make a substantial difference. It allows the user to maintain control, making it a go-to choice for many professionals involved in construction and exploration.
Diamond Drill
Diamond drills are often regarded as the crème de la crème in rock drilling. Embedding diamond particles on the drill bit allows for unmatched hardness and cutting performance. These are specifically designed for deep drilling and tasks that require utmost accuracy.
Noteworthy Characteristics:
- Exceptional Durability: With diamonds, the drill bits can cut through the hardest geological materials, such as igneous rocks, with ease.
- Precision: Ideal for core sampling, where collecting samples for analysis is essential. The minimized damage to surrounding material is advantageous for geological research and exploration.
"Investing in a diamond drill may seem steep, but for rigorous exploration or mining activities, it pays off in spades due to efficiency and longevity."
Masonry Drill
Masonry drills, while not as specialized as the previously mentioned types, serve a crucial role when materials like brick or concrete come into play. Though they are intended for softer materials, they also find utility in certain rock formations—notably when used with specifically designed bits.
Key Points:
- Application Focus: Best suited for construction projects, masonry drills are versatile enough for smaller rock drilling tasks as well.
- Design Variance: They commonly feature a spiral flute design that aids in faster drilling of tougher materials, allowing for effective removal of debris.
Key Considerations When Choosing a Rock Drill
Selecting the right rock drill involves several important factors to ensure effectiveness and efficiency during drilling operations. Each aspect plays a pivotal role in influencing the overall outcome and performance of the drilling process. Understanding these considerations not only helps in selecting an appropriate drill but also enhances user satisfaction and operational success. Here’s a breakdown of the critical elements that should guide your decision-making when venturing into rock drilling.
Type of Rock Being Drilled
The nature of the rock dictates which kind of drill will perform best. Soft rock, like sandstone, may respond well to rotary drills, while hard rock, such as granite, demands robust percussion or diamond drills. Knowing the specific characteristics of the rock helps in determining the drill's capabilities and limitations to maximize drilling efficiency. For example, drilling through igneous rocks often requires specialized bits designed for high durability.
Drill Bit Material
Drill bit material is another cornerstone aspect to consider. It not only influences the drilling speed but also the longevity of the bit itself under varying rock conditions. Choosing the right material can make or break a drilling operation.
Carbon Steel
Carbon steel drill bits are widely appreciated for their affordability and versatility. They are hard enough for common drilling tasks in softer rock types yet may dull quicker in harder formations. Their affordability makes them a popular choice for hobbyists or those just starting out, offering decent performance without breaking the bank. However, they can struggle under intense conditions where wear resistance is crucial.
Cobalt Steel
Cobalt steel bits stand out due to their improved hardness and wear resistance. They are often used for tougher applications, making them suitable for drilling through harder rock types. The unique feature here is their ability to withstand high temperatures, which occurs during difficult drilling tasks. Although more costly than carbon steel, they offer a significant endurance advantage, especially in repeated use scenarios.
Carbide
Carbide bits are often the go-to for professionals dealing with challenging rock materials. They exhibit exceptional hardness and retain their sharpness even under extreme conditions. This choice minimizes downtime that can happen when bits wear out. However, they are more fragile and can shatter under sudden stress. Thus, understanding the specific rock context and the potential risks involved is essential when selecting carbide bits.
Power Source Options
Choosing the power source for your rock drill can drastically affect performance and usability.
Electric Drills
Electric drills are favored for their consistent power output and ease of use, especially in confined areas. They eliminate exhaust fumes, making them suitable for indoor drilling tasks. The connection to an electrical source offers infinite runtime, but users must plan for the availability of outlets, especially on construction sites.
Gas-Powered Drills
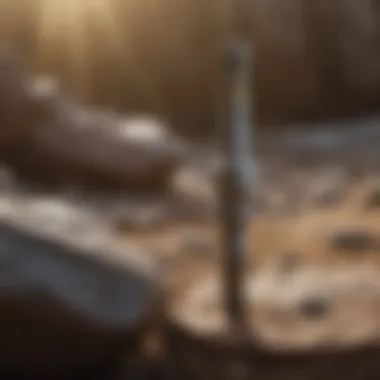
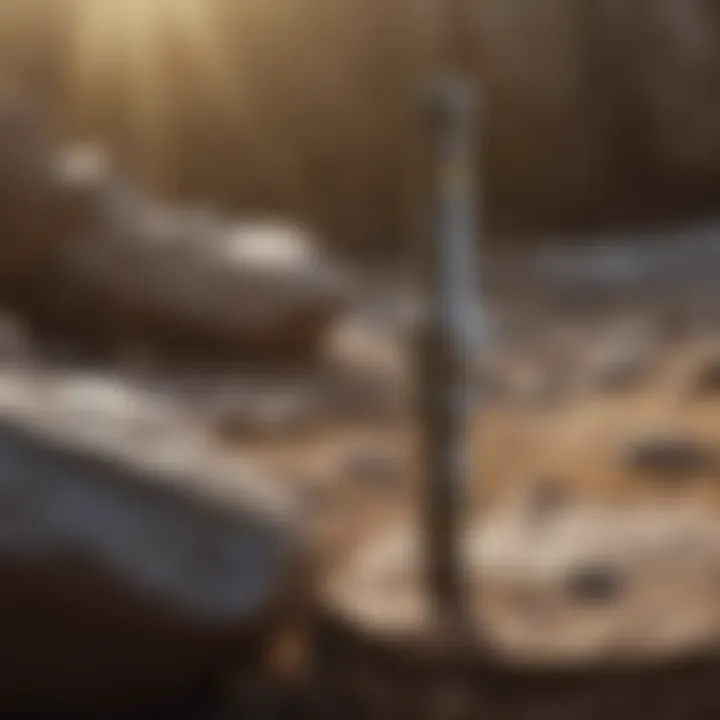
Gas-powered drills provide mobility and are generally favored for outdoor applications. With no cords, users can maneuver freely, making them ideal for remote locations. They exhibit strong drilling power, particularly in rugged terrains. However, the key disadvantage lies in the maintenance required for gas engines and the emissions produced during operation, which might not suit every workplace.
Pneumatic Drills
Pneumatic drills utilize compressed air, providing a powerful option for heavy-duty drilling tasks. Their ability to deliver high torque speeds often results in faster drilling times. They are particularly advantageous in drilling projects where electricity is unreliable or unavailable. That said, they demand access to an air compressor, limiting their use in certain situations. Their effective nature allows for greater efficiency but also requires caution due to the complexity of their setup.
Size and Weight Considerations
The drill’s size and weight can influence handling and the type of work that can be carried out safely. Heavier drills may provide more power, but maneuverability becomes a challenge, especially for overhead or vertical drilling tasks. A lightweight drill often allows for more ease of use, but it might sacrifice durability and power.
Drilling Techniques and Tips
When it comes to rock drilling, the techniques employed can significantly impact the outcomes of your projects. Selecting the right methods not only maximizes efficiency but also ensures greater precision, ultimately saving time and reducing costs. This section delves into three critical aspects of drilling techniques: maintaining proper angles, avoiding common mistakes, and enhancing overall drilling efficiency.
Proper Drilling Angles
Nailing the right drilling angle is akin to having a keen eye in the world of rock applications. The angle can determine the rate of penetration, the wear on your drill bit, and the integrity of the hole being drilled. For instance, a steep angle might help in breaking through softer materials but can increase the risk of damaging the drill bit when working on harder surfaces. Conversely, drilling at a shallower angle is often more suitable for deep holes but may demand more time to achieve desired depths.
- Consider the following tips for proper angles:
- Assess the material: Identify the type of rock – softer sedimentary compositions require a different approach compared to hard igneous rocks.
- Use a level tool: Leveling equipment can help maintain consistent angles, especially during longer drilling sessions.
- Adjust dynamically: Ground conditions might change unexpectedly, so be prepared to adjust your drilling angle as needed.
"Proper angles can make or break your rock drilling experience. They play a crucial role in optimizing the drilling process."
Avoiding Common Mistakes
There are several pitfalls that even experienced drillers can fall into when working on rock projects. Awareness of these mistakes allows one to steer clear of them and enhances the overall experience and results.
- Common mistakes to avoid include:
- Insufficient Lubrication: Failing to adequately lubricate the drill bit can result in overheating, damaging both the bit and the rock being drilled.
- Inappropriate Speed Settings: Operating the drill too fast on tough materials can increase wear and tear, while going too slow on softer materials can hinder progress and productivity.
- Ignoring Safety Protocols: Skipping safety precautions, such as wearing protective gear or neglecting to check equipment before use, can result in serious accidents and injuries.
Enhancing Efficiency in Drilling
Efficiency is the name of the game in rock drilling. The quicker and more accurately you can drill, the more productive your work will be.
- Strategies for enhancing drilling efficiency include:
- Choose the right drill bits: Depending on the rock type, using specialized bits tailored for particular applications can improve performance.
- Regular Maintenance: Keeping equipment in top shape reduces downtime from repairs and failures.
- Work in teams: Two or three people can make light work of a heavy drilling session, ensuring that one person is managing the drill while others take care of logistics or handling materials.
In summary, employing effective drilling techniques is indispensable for optimal rock applications. By considering the right angles, avoiding common missteps, and continuously improving efficiency through strategic practices, you can transform your drilling endeavors into successful projects.
Applications of Rock Drilling
The topic of rock drilling applications holds significant weight in understanding the real-world utility of drilling technologies. Different industrial and scientific fields depend heavily on effective rock drilling techniques. It’s not just about choosing a drill and getting to work; aspects like the specific type of job at hand, efficiency, and project goals matter deeply. A well-selected drill can enhance productivity, reduce costs, and increase the overall safety of the work environment.
Geological Exploration
In geological exploration, the primary objective is to gain a deeper understanding of the earth's composition. Here, rock drilling isn’t merely a means to an end; rather, it’s a critical path to uncovering valuable insights. By collecting core samples, geologists can analyze rock types, mineral compositions, and potential resources.
Drilling provides the tangible evidence necessary to inform decision-making processes for resource extraction or environmental assessments. Applications in this field can include:
- Identifying mineral deposits for mining Ventures
- Mapping geological formations to assess stability for future construction
- Conducting research related to seismic activity
In geological exploration, utilizing a diamond drill is common due to its precision and ability to cut through hard rock efficiently. Consequently, selecting the right drill can mean the difference between success and costly setbacks.
Construction Projects
Rock drilling is perhaps most visible in construction projects. Whether constructing foundations for towering buildings or creating tunnels for efficient transportation, the quality and efficiency of drilling operations are paramount. The size of the drill, power source, and drill bit material should align with the project's specific demands.
Key considerations in construction include:
- Safety Regulations: Adhering to industry-standard safety measures is non-negotiable. Workers must be trained, and protective equipment utilized.
- Project Specifications: The geological conditions determine the type of drill used. In softer rock, a rotary drill may suffice, but harder materials may necessitate a percussion drill.
- Time Efficiency: Selecting a drill capable of expediting the drilling process ensures that the overall project timeline stays intact.
The right drilling equipment can prevent project delays and cost overruns, making it an essential area of focus.
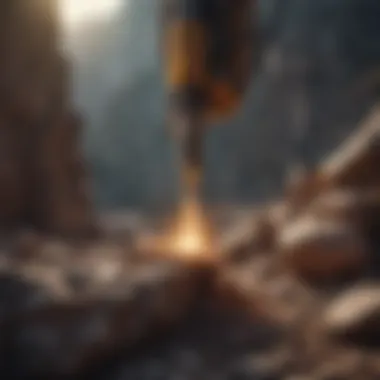
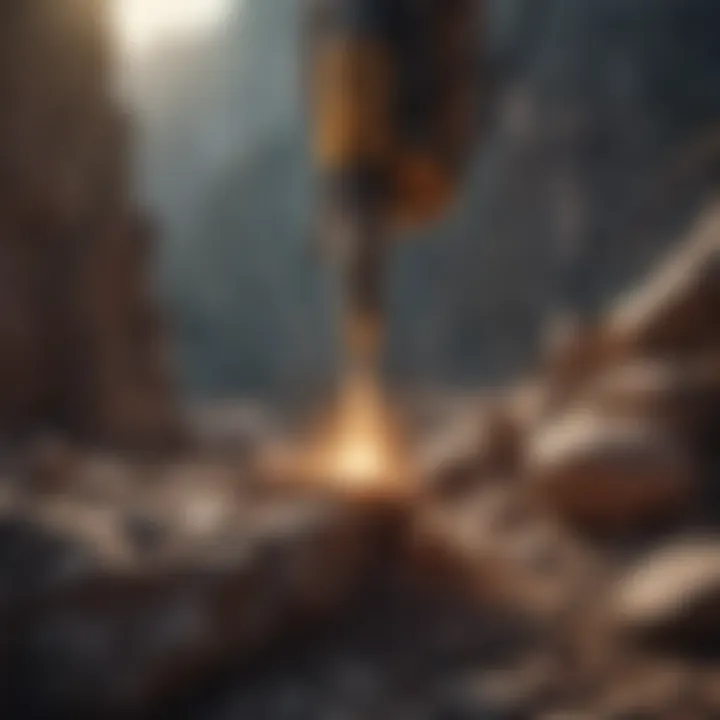
Fossil Excavation
Fossil excavation represents a fascinating intersection of science and history. Rock drilling plays a critical role in this field, as it allows paleontologists to carefully extract fossils from rock layers, often without causing damage. This meticulous approach gives researchers a chance to study ancient life forms and their environments.
Factors influencing drilling techniques for fossil extraction include:
- Preservation of fossils: Using less aggressive drilling techniques minimizes the risk of damaging delicate specimens.
- Contextual Understanding: Each fossil carries significant information about its geological setting. A robust drilling strategy aids in maintaining the context, which is invaluable for research.
A common practice in fossil excavation involves the use of masonry drills, which cater to softer sedimentary rocks typically containing fossils. Attention to detail in both selection and application of tools enhances scientific knowledge while preserving history.
Effective drilling tailors to the specific needs of each application, ensuring that industries can maximize efficiency and preserve the integrity of both current and historical data.
Safety Measures in Rock Drilling
When it comes to rock drilling, safety isn't just a box to tick; it’s the bedrock of every successful operation. Safe practices in this potentially hazardous field safeguard not only the well-being of workers but also the integrity of the project at hand. By adhering to specific safety measures, risks can be minimized, ensuring that drilling activities progress smoothly without unforeseen disruptions. This section delves into the crucial aspects of safety measures in rock drilling, underscoring their importance while drawing attention to protective gear, equipment, and adherence to industry standards.
Protective Gear and Equipment
Every drill operator knows that the best way to avoid injury is to be equipped with the proper gear. The right protective equipment acts as the first line of defense against hazards that are part of the rock drilling landscape. Wearing personal protective equipment (PPE) isn’t simply recommended; it's essential. The critical items include:
- Hard Hats: Given the risk of falling debris, hard hats protect the head from serious injury.
- Safety Goggles: Eyes are vulnerable where fine particles are ejected, so goggles safeguard against dust and debris.
- Ear Protection: High noise levels from drills and machinery can be damaging; using earplugs or earmuffs can prevent long-term hearing loss.
- Steel-Toed Boots: These footwear types protect against heavy equipment or falling rocks that could cause foot injuries.
- Gloves: Not only do gloves enhance grip but they also protect hands from cuts and abrasions.
Understanding and utilizing this gear plays a pivotal role in maintaining a safe working environment. Moreover, regular inspection of equipment ensures that gear doesn’t lose its protective qualities.
Adhering to Industry Standards
In any field, standing by industry standards ensures that operations align with best practices, and rock drilling is no exception. Agencies and organizations, such as the Occupational Safety and Health Administration (OSHA), lay down specific regulations that guide drilling operations. Following these standards brings forth numerous benefits, including:
- Reduced Risk of Incidents: When procedures align with established standards, the likelihood of accidents diminishes significantly.
- Legal Compliance: Adhering to these standards protects operators from legal repercussions that may arise from mishaps.
- Boosted Credibility: Companies known for following industry regulations typically gain a reputation for safety, which can lead to new opportunities and partnerships.
Operators should keep abreast of the latest standards and train all members of the drilling team accordingly.
"Safety is not just a priority; it’s a ethics and way of life. In every drilling operation, it should be the anchor that holds everything in place."
In summation, safe drilling practices underscore the significance of protective gear, the commitment to equipment checks, and unwavering adherence to industry standards. By prioritizing safety in rock drilling, operators not only protect their workforce but also position their projects for success, enabling a smooth and efficient drilling experience.
Market Trends and Innovations in Rock Drilling
The landscape of rock drilling is transforming. This shift is not merely about keeping pace with advancements but fostering a new era of operational effectiveness and sustainability. Understanding current market trends and innovations is paramount, as these elements directly inform the choices that rock drillers make. With the right knowledge, enthusiasts can maximize their drilling activities and minimize challenges associated with traditional methods.
Emerging Technologies
Recent years have seen an influx of technology-driven solutions in rock drilling. High-performance drills are becoming equipped with smart sensors and automation capabilities. These innovations enable real-time monitoring of drilling conditions, ensuring precision and efficiency. Smart drills can adjust their parameters on-the-fly, adapting to varying rock types or moisture levels, limiting wear and tear.
Some notable technologies changing the game include:
- Autonomous Drilling Systems: These advanced units can operate with minimal human intervention, allowing for more consistent results, especially in complex geological environments.
- 3D Simulation Software: Before any drilling begins, geologists can use 3D simulation software to visualize the rock strata, enhancing planning accuracy. This means less guesswork and more data-driven decisions on drill selection.
- Hybrid Drill Bits: Combining the benefits of different materials (like carbide and diamond), these bits are engineered to withstand tougher conditions while providing better durability. This innovation is crucial for drilling in hard rock environments.
"In rock drilling, as in life, adaptation is key. Technological advancements redefine what is possible, allowing drills to do more with less effort."
Sustainability Considerations
Sustainability is another critical factor influencing the rock drilling industry. As environmental concerns gain traction globally, drill manufacturers are adapting to meet these demands. Sustainable practices aren’t just an option anymore; they’re a necessity. Here are a few ways in which sustainability is being integrated:
- Eco-Friendly Materials: Many companies are focusing on using recycled or recyclable materials in the construction of drill bits and machinery, reducing the overall environmental footprint.
- Energy Efficiency: Newer models are designed to consume less power without compromising performance. This aspect benefits not just the planet but also operational costs in the long run.
- Waste Management Systems: Effective drills now come equipped with systems that minimize dust and debris, not only safeguarding the immediate surroundings but also improving visibility and even safety for operators.
The push towards sustainability is not merely about compliance; it’s about innovation and foresight. By embracing these emerging trends and technologies, rock drilling can continue to evolve, maximizing efficiency and minimizing environmental impact.
Ending
In summation, the process of selecting the right drill for rock applications is not something to be taken lightly. It requires a keen understanding of various factors, from the type of rock to the specific drilling techniques that shall be employed. This section synthesizes what has been explored throughout the article, highlighting the crucial points that contribute to informed decision-making in rock drilling.
Recap of Key Points
- Types of Drills: The landscape of rock drilling is vast, with rotary, percussion, diamond, and masonry drills catering to different needs. Choosing the right type can greatly affect not just efficiency but also the quality of the drilling performed.
- Key Considerations: Breakdown of elements such as rock type, drill bit material, and power source can significantly alter performance. Each component plays its part in the intricate puzzle of drilling.
- Drilling Techniques: Emphasis was placed on employing proper angles and techniques to avoid common mistakes, ensuring that drilling tasks are accomplished with minimal setbacks.
- Safety Measures: One cannot overlook the importance of safety gear and adherence to industry standards. These practices not only protect the user but also can enhance overall productivity.
- Market Trends: The insights into emerging technologies and sustainability factors show a forward-thinking approach, vital for anyone in the field aiming to remain competitive.
Future Outlook in Rock Drilling
The future of rock drilling holds intriguing possibilities that promise to revolutionize the industry. As technology continues to evolve, we foresee advancements such as:
- Automation: Increased use of automated drilling systems could streamline operations, allowing for more precise and efficient drilling with reduced need for manual intervention.
- Sustainable Practices: A shift towards eco-friendly materials and methods in drilling projects will likely gain traction. This is not only beneficial for the environment but also could cater to a growing market demand.
- Data-Driven Decision Making: Utilizing data analytics and real-time monitoring technologies could lead to smarter drilling operations. Such changes would facilitate better predictive maintenance and operational adjustments in real-time.
- Improved Training Programs: Enhanced educational resources focusing on best practices and innovative approaches in rock drilling will empower new and seasoned enthusiasts alike.
The road ahead is paved with notable changes that can cater to the evolving demands of rock drilling applications. As we adapt to new technologies, the efficiency and effectiveness of drills will fundamentally shift, providing an exciting horizon for rock and fossil collectors. It’s crucial for all involved in this field to remain informed and prepared, ensuring they can leverage these advancements for fruitful outcomes.