The Art and Craft of Silver Casting Jewellery
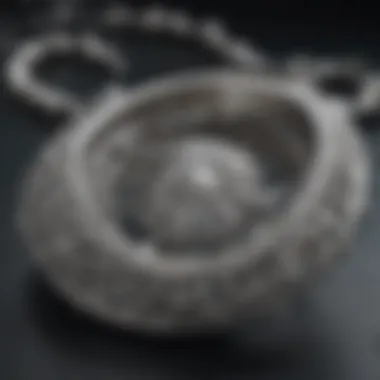
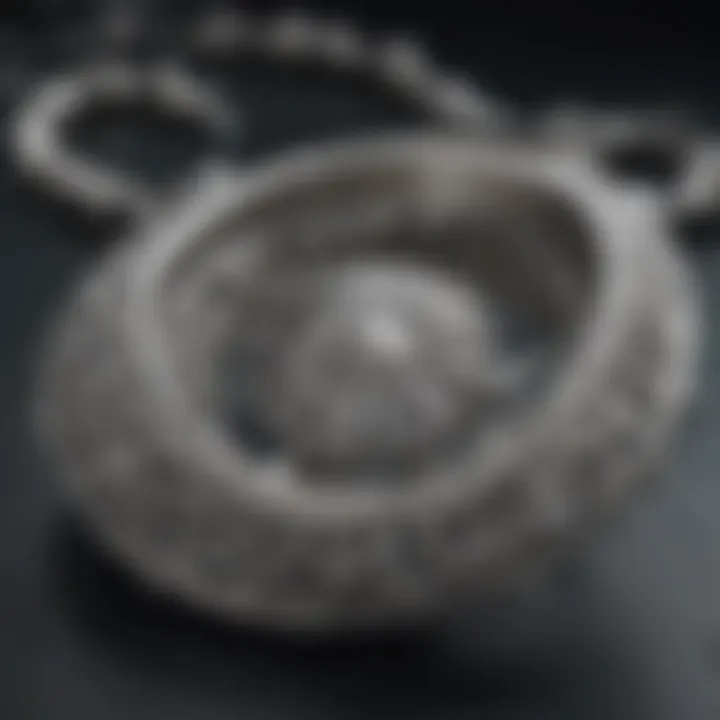
Intro
Silver casting jewellery is not just an art; it's a rich tapestry woven with history, technique, and individual creativity. While the glimmer of silver may catch a casual observer's eye, the depth of knowledge and skill that lies beneath that sheen is what truly characterizes a master artisan. This article aims to peel back the layers, inviting the reader to explore not only the methods and tools used in silver casting but also the artistic vision that shapes each unique piece.
From its historical roots to contemporary practices, silver casting reveals much about human ingenuity and aesthetic expression. The intricacies involved in design, the selection of materials, and the careful execution of techniques tell a compelling story about cultural significance and personal expression in the realm of jewellery. As we journey through this landscape, we'll touch on the challenges artisans face and how these obstacles influence the evolution of their craft in today’s market.
It’s like creating a sculpture where every curve and detail holds meaning, each piece narrating its own story while echoing the traditions of its predecessors.
Understanding Silver Casting Jewellery
Understanding silver casting jewellery is crucial for those interested in the craftsmanship behind it. The art itself goes beyond mere creation; it embodies rich historical narratives and connects to cultural significance across various societies. Silver casting is not just a technical process; it reflects human emotions, stories, and traditions.
The importance of silver casting can be found in its ability to blend artistic expression with practical functionality. Artisans utilize this method not merely to produce items but to tell stories and evoke sentiments within the pieces they create. Furthermore, knowledge of silver casting allows collectors and enthusiasts to appreciate nuances in design, craftsmanship, and even historical context that can enhance their experience and understanding of the jewellery.
Historical Context
Origins of Silver Casting
The origins of silver casting can be traced back to ancient civilizations, where silver was often held in high esteem. Its reflective properties and relative rarity compared to base metals made it a sought-after material. The process began with artisans using simple tools and techniques to mold and shape silver into decorative items and functional objects.
Key to the origins of silver casting is the fact that it was often used in the creation of ceremonial objects and offerings. This reflects its ritualistic importance and showcases how craftsmanship was culturally woven into daily life. The unique feature of these early practices was their reliance on natural resources and local artistry, which fostered innovation out of necessity.
Cultural Significance Across Civilizations
Across various civilizations, silver casting has played a fundamental role in communication and identity. For instance, the jewelry from pre-Columbian cultures often symbolized status, while in European history, silver pieces adorned religious artifacts and royal regalia.
This cultural significance lies not just in the material itself but in its transformation into something meaningful. Silver casting encapsulates moments of history and social status, making it a worthwhile focus for this article. However, access to silver resources and skilled craftsmen varied globally, impacting the evolution and styles seen in different regions.
Evolution of Techniques Over Time
As societies progressed, so too did the techniques employed in silver casting. Early methods have evolved into more sophisticated practices, like lost-wax casting, which allows for intricate designs. The enthralling thing about this evolution is the way it marries tradition with modernity; artisans today often blend age-old methods with contemporary aesthetics.
This blend underscores the adaptability of silver casting techniques, enabling craftsmen to push boundaries while still honoring ancestral practices. However, the disadvantage is that some intricate techniques require extensive skill and practice, leading to higher costs for artisans and consumers.
Fundamentals of Silver Casting
What is Silver Casting?
At its core, silver casting is a method of shaping molten silver into desired forms, typically through molds. This versatile process can yield intricate designs for jewellery, ensuring that each piece can be unique.
What makes silver casting a popular option is its flexibility in creation. Artisans can manipulate the metal to produce everything from minimalist rings to elaborate necklaces. However, there are challenges; casting can lead to imperfections if not carefully controlled, thus affecting the final quality.
Essential Characteristics of Silver
Silver is renowned for its luster and durability which contribute to its desirability in jewellery making. Important characteristics include its malleability, allowing it to be shaped easily without breaking, and its hypoallergenic nature, appealing to sensitivity-prone individuals.
However, understanding the differences between alloys is crucial. For example, sterling silver, which is 92.5% silver mixed with other metals, offers distinct properties compared to fine silver, which is purely silver. This distinction is beneficial to consider within the context of crafting jewellery, as it helps artisans choose materials suited to their design goals.
Comparison with Other Metal Casting Techniques
When comparing silver casting to other metal casting techniques, distinctions become clear in aspects such as cost, material properties, and application. For instance, bronze casting, which predominantly uses a copper alloy, can evoke different textures and aesthetics than silver.
Silver casting may command a premium due to the value of its raw material. This can be both an advantage, as it draws attention to craftsmanship, and a disadvantage, as it may limit the accessibility for budding artisans. Moreover, silver’s properties allow for finer details that other metals might not achieve as easily, making it a preferred choice for high-end fashion jewellery.
Key Techniques in Silver Casting
When it comes to silver casting jewellery, understanding the techniques involved is not just an afterthought; it's the backbone of the craft. Each method carries its own set of benefits relevant to the goals of designers and artisans alike. These techniques pave the way for innovation while honoring traditional practices, creating a bridge between the past and the present. The choice of casting technique can notably affect the final appearance and functionality of the pieces, greatly influencing the artistry that emerges from the workshop.
Investment Casting
Process Overview
Investment casting is one of the most dependable methods for producing intricate silver pieces. The process begins with creating a detailed wax model of the item. This model is then covered in a special ceramic material that hardens upon heating. Once the ceramic shell can withstand high temperatures, the wax is melted out, leaving behind a mold. Silver is then poured into this empty space, allowing for precise replicas of the original model. This attention to detail makes investment casting a popular choice when the design calls for complexity and finesse. The key characteristic of this process is its precision, which lays the groundwork for creating highly detailed jewellery designs that might be tough to achieve through other methods.
Advantages and Disadvantages
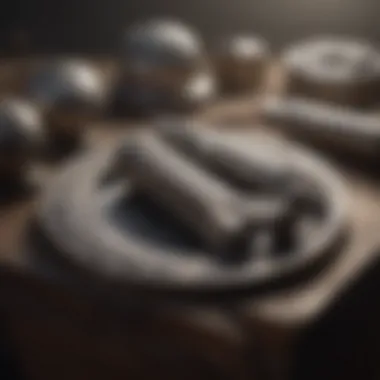
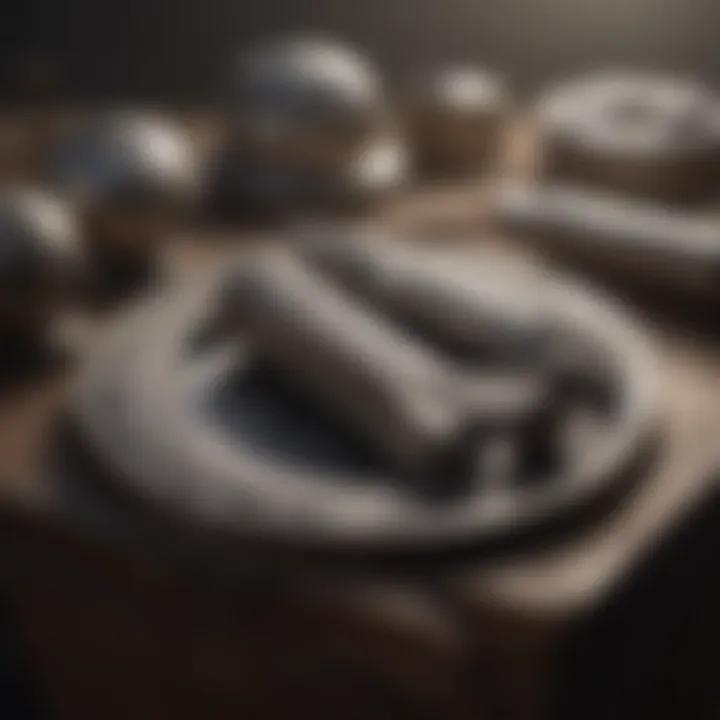
Though investment casting shines in many aspects, it’s essential to weigh its pros and cons. A noteworthy advantage is the ability to produce fine details and shapes that are otherwise impossible or challenging with other techniques. However, it comes with downsides like longer production times and higher costs due to the required materials and equipment. This technique might not be everyone's cup of tea, especially for small-scale productions, where quick turnarounds are preferred. Nevertheless, for jewellery designers focusing on intricate and high-quality pieces, investment casting remains a favored choice.
Applications in Jewellery Design
Investment casting has found its niche in creating bespoke jewellery. For example, artisanal bracelets or pendants with complex patterns or textures often rely on this method to achieve that signature look. The detail retained in the final product is a significant reason many artisans opt for investment casting. Its application goes beyond mere aesthetics; it also enables the incorporation of elements from various cultures or stories, making each piece not only beautiful but rich in narrative.
Die Casting
Understanding Die Casting
Die casting is another essential technique used in silver jewellery making. This process involves pouring liquid silver into a pre-made metal mold. The molten metal fills the mold under pressure, allowing for rapid production of consistent shapes. The strength and durability of die casting come from the use of metal molds, which can endure high temperatures and pressures during the casting process. Designers often choose this approach because it offers a reliable way to produce the same piece multiple times without sacrificing quality.
Tools and Machinery Involved
The machinery in die casting is straightforward yet vital. Key tools include melting furnaces heated at consistent temperatures, high-pressure machines to inject the molten metal, and precision molds crafted from hardened metal. The use of such equipment ensures accuracy and reduces the waste often associated with other casting methods. Though the initial investment in machinery can be a hurdle for some artisans, the potential for reproducibility makes this technique attractive, particularly for designers looking to upscale their production without compromising quality.
When to Choose Die Casting
Die casting is an excellent option when the goal is to produce uniform items en masse. For instance, if a jeweller needs a collection of identical rings or bracelets, die casting is the way to go. While the initial setup could be costly, the long-term benefits in terms of efficiency and product consistency are worth the consideration. Designers should keep in mind, however, that while die casting is great for simpler designs, it may not provide the fine details that other methods, like investment casting, can offer.
Lost Wax Casting
Detailed Process Description
Lost wax casting stands as one of the oldest techniques in jewellery making. The process starts with crafting a model from wax, which is coated in a ceramic shell. After the shell is hardened, it is heated to remove the wax, hence the name "lost wax." The empty mold can then be filled with molten silver. What makes this method so appealing is the creative flexibility it offers artisans. Details etched in the wax are captured perfectly in metal, giving each piece a uniqueness that resonates with the artisan's vision.
Historical Roots of Lost Wax Technique
Lost wax casting has an intriguing history dating back to ancient civilizations, from the Egyptians to the Mayans. It's interesting to note how this technique has evolved while preserving its core principles. Its longstanding relevance in the jewellery-making world is evidence of its reliability. The traditional aspect cannot be understated, as many contemporary artisans still look to historical practices to infuse their creations with age-old wisdom while adapting to new trends.
Creative Freedom through Wax Models
The beauty of lost wax casting lies in its unfettered creative potential. Artists can sculpt intricate details into the wax model that may be difficult to replicate through other means. This method allows for the freedom to experiment and innovate in design. Each wax model is a direct reflection of the artist's imagination before being transformed into silver. While this technique has its advantages, including the ability to create intricate designs and one-of-a-kind pieces, it also requires a deft hand and a clear vision, as mistakes in the wax model can lead to costly errors in the final piece.
Materials Involved in Silver Casting
The materials used in silver casting play a crucial role in the overall quality and aesthetics of the final jewellery piece. From the type of silver alloy selected to the tools and equipment utilized, each element significantly impacts both the process and the outcome. The right choice of materials ensures durability, malleability, and a desirable finish, making the knowledge of these components essential for artisans and collectors alike.
Types of Silver Alloys
Fine Silver vs. Sterling Silver
Fine silver, which consists of 99.9% silver, stands out for its soft and shiny characteristics. This purity often makes it a preferred choice for intricate designs, as it can be crafted into delicate pieces without much hassle. However, its malleability also poses a risk; fine silver can easily get scratched or dented. On the other hand, sterling silver is an alloy made primarily of 92.5% silver mixed with 7.5% of another metal, usually copper. This combination enhances strength and resilience. Hence, sterling silver is a beneficial choice for artisans focusing on both durability and aesthetic appeal.
"The choice between fine and sterling silver can make or break a piece in terms of its long-term functionality and beauty."
Other Common Alloys Used
When it comes to crafting jewellery, there are several other alloys that artists may explore. Argentium silver, for instance, contains a hint of germanium, enhancing its tarnish resistance, making it an appealing go-to for contemporary jewellers. Another option is Britannia silver, which has a higher silver content than sterling, creating a bright white finish. Each alloy offers unique characteristics that impact both the casting process and the final appearance of the piece. An advantage of these alloys is their ability to cater to different design needs, while their notable disadvantages often include variations in price and workability.
Choosing the Right Alloy for Your Project
Selecting the appropriate alloy hinges upon several considerations. The project's specific requirements, like desired durability, appearance, and budget, can all steer the artisan's choice. For those aiming for high-quality output with a lower likelihood of tarnish, Argentium may be the ideal pick. However, for projects demanding intricate details, sterling silver could be more suitable due to its workability. Different projects also call for various characteristics, and understanding these can greatly enhance the end result.
Additional Materials and Tools
Molds and Casting Equipment
The foundations of silver casting often lie in the molds and equipment chosen for the task. High-quality molds crafted from metal or silicone can determine the level of detail achievable in a design. Metal molds, while durable, provide less flexibility compared to silicone options, which easily release cast items without damage. The selection of these tools greatly influences the intricacy and accuracy of the castings produced, underscoring their importance in the jewellery-making process.
Finishing Tools for Detailing
Once pieces are cast, they usually undergo a series of finishing steps to enhance aesthetics and polish. Tools such as grinders, sanders, and files help achieve that perfect shine and detail. For many artisans, investing in high-quality finishing tools is crucial, as they can determine the overall look and feel of the piece. However, the complexity of some tools may present a learning curve, something that beginners must consider before use.
Soldering and Joining Components
The process of joining different parts of a jewellery piece often demands precision and skill. Different soldering techniques and materials directly affect the outcome of the assembly. Using the right solder helps create strong, seamless joins between components, ensuring durability in the finished item. The disadvantage here is the risk of overheating, which might damage the pieces assembled.
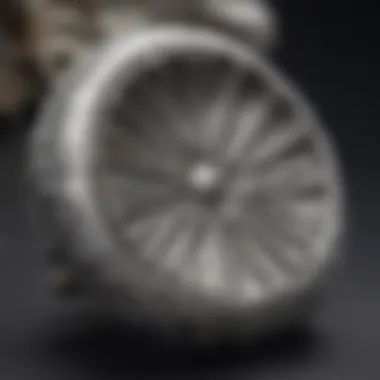
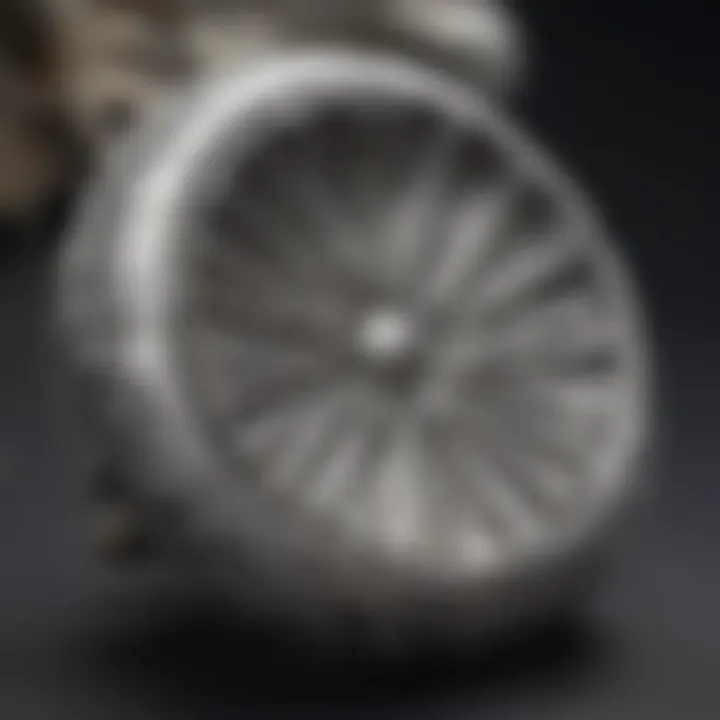
Through understanding these materials and tools, artisans can elevate their craft in silver casting, leading to creations that are not only functional but also visually striking.
Design Principles in Silver Casting Jewellery
Design principles play a crucial role in silver casting jewellery, as they lie at the intersection of artistry and functionality. These principles guide artisans and designers to create pieces that are not only visually appealing but also practical for everyday wear. Unpacking the design principles means looking closely at aesthetic considerations and understanding the factors that influence choices in the creation process. The ultimate aim is to strike the right balance between beauty and usability, which is key to a successful piece of jewellery.
Aesthetic Considerations
Balancing Beauty and Functionality
Balancing beauty and functionality is often seen as the backbone of successful jewellery design. This approach emphasizes creating pieces that are striking yet comfortable to wear. A key characteristic of this balance is ensuring that designs cater to the needs of the wearer. For instance, a striking pendant might catch the eye, but if it swings too low, it might snag on clothing, detracting from its allure.
The unique feature of this balance lies in the meticulous choice of materials and forms. Designers often experiment with various shapes that conform to the natural contours of the body, such as hoops that wrap elegantly around the ears. Such designs not only enhance the aesthetic appeal but also ensure that the piece stands up to everyday use. However, a disadvantage can arise when aesthetic choices overpower practicality, leading to designs that are beautiful but not wearable.
Incorporating Cultural Elements
Incorporating cultural elements into jewellery embraces diversity and tradition, enriching the narrative behind each piece. This aspect allows artisans to pay homage to their heritage while creating something new and appealing. A key characteristic here is the use of symbols or motifs that carry specific meanings, such as the use of the tree of life symbol found in many indigenous cultures, symbolizing connection and life.
These cultural undertones add a unique layer to jewellery that can resonate deeply with buyers, making it a popular choice for many designers today. However, the challenge lies in representing these elements authentically without veering into cultural appropriation, which can create backlash.
Trends in Modern Silver Design
Trends in modern silver design highlight the evolution of tastes and the advances in techniques. This evolution reflects changing consumer preferences, showcasing a shift towards minimalist designs with clean lines. A characteristic of these trends is the fusion of traditional craftsmanship with contemporary aesthetics, appealing to both young and older generations alike.
Designers are increasingly using 3D printing technology, allowing for intricate designs that were previously hard to achieve. This creates unique pieces capable of capturing the imagination. However, there is a downside; as more mass-produced designs flood the market, maintaining an artisan touch becomes a significant challenge, which can affect the perceived value of handmade items.
Factors Influencing Design Choices
Target Market Preferences
Understanding target market preferences is fundamental for jewellery designers. This aspect refers to tailoring designs that resonate with the anticipated clientele's tastes and needs. A defining characteristic is that different demographics may have varying desires. For example, younger consumers might lean towards bold, unique pieces, while older buyers often prefer classic designs.
This understanding allows designers to make informed decisions about which materials and styles to pursue, ultimately maximizing appeal. However, a risk exists in over-analyzing trends, which can lead to a dilution of a designer's unique voice in their work.
Price Point Implications
Price point implications significantly impact design choices, as they dictate the material selection, workmanship, and target audience. The defining characteristic in this aspect is affordability versus luxury. For example, a piece made with fine silver and intricate detail may attract a higher price, catering to a more affluent market.
Designers must navigate these waters carefully, balancing quality with accessibility. While higher-priced items can establish an air of exclusivity, they may limit the broader market. On the flip side, lower-priced items run the risk of being perceived as inferior, which can affect brand identity.
Sustainability and Ethical Sourcing
Sustainability and ethical sourcing have emerged as pivotal factors influencing jewellery design. This focus reflects a global shift towards more conscious consumption. The key characteristic is ensuring that materials, particularly silver, are sourced responsibly, avoiding practices that harm the environment or communities.
Such practices are now seen as beneficial for brand loyalty, as consumers increasingly seek transparency regarding the origin of their purchases. This commitment contributes positively to the designer’s reputation, enhancing their marketability. Yet, the downside can be higher production costs and challenges in sourcing compliant materials, complicating the designer's manufacturing process.
In summary, understanding the design principles, aesthetic considerations, and the factors influencing design choices is essential in the world of silver casting jewellery. This knowledge enables artisans and designers to create pieces that reflect personal artistry while also appealing to market demands.
Challenges in Silver Casting
Engaging in silver casting jewellery is no walk in the park. While the process can yield stunning pieces, it certainly comes with its own share of hurdles that can be quite the headache. Understanding these challenges helps artisans refine their craft, ensuring better outcomes. The significance of tackling these difficulties cannot be overstated; every craftsman who plays with molten silver must be aware of the potential mishaps that can tarnish despite the shine of the metal.
Common Pitfalls
Metal Defects and Handling Issues
Metal defects are akin to a hidden landmine in the world of silver casting. These pesky little problems can arise from various sources, including impurities in the alloy or improper casting temperatures. For instance, if the silver becomes too cool before it fully flows into a mold, it could result in incomplete designs or weak spots. The consequence here is twofold: not only does it compromise the integrity of the piece, but it can also lead to costly reworks.
It's crucial for a jeweller to keep their workspace tidy and organized. Handling issues—like dropping a piece or misplacing tools—can be just as damaging. Each slip-up has the potential to derai the entire project, making attention to detail vitally important.
"An ounce of prevention is worth a pound of cure."
In this case, ensuring a clean and safe environment can save hours of frustration.
Overcoming Design Flaws
Design flaws are another stumbling block. A piece may look stunning on paper, but once the silver is poured, reality can hit hard. This highlights a significant aspect of silver casting; one must stay flexible and ready to adjust. A common issue is underestimating how the dimensions will behave when the silver cools, leading to unexpected results.
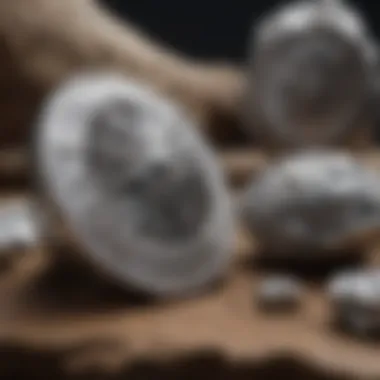
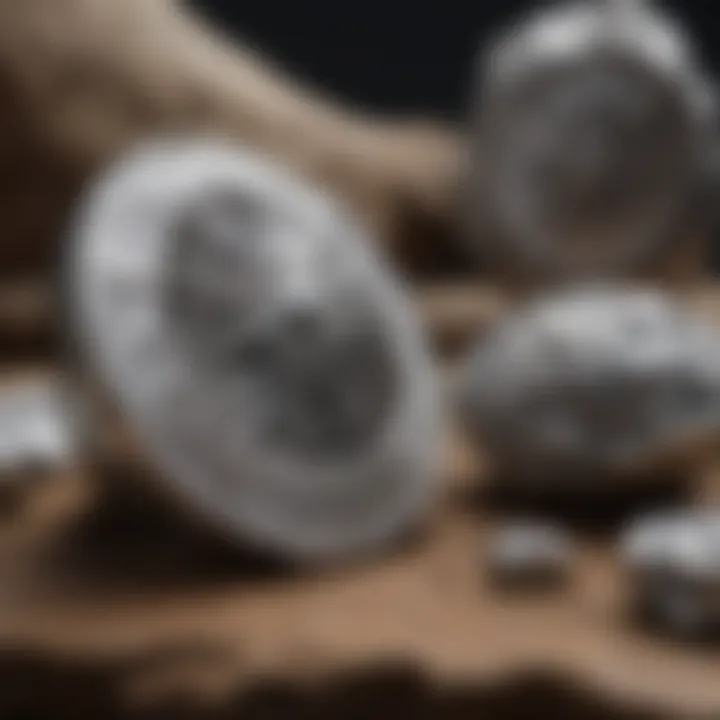
However, being able to pivot and create adjustments on the fly showcases adaptability—a highly admired quality in creative fields. Finding a balance between the ideal concept and practicality is not just beneficial, it’s essential. With a Yoda-like patience, artisans often learn to adapt flaws into beauty through innovation.
Workplace Safety Concerns
Safety in the workshop is paramount, and there are critical factors to consider here. Hot molten silver can be unforgiving. Failing to wear proper safety gear or maintaining an untidy workspace can result in serious injuries. Further, the fumes produced during casting processes may pose health risks—ventilation can't be an afterthought.
Creating a safe environment not only protects the artisan but enhances creativity too. A well-organized, secure workplace fosters focus, allowing artists to work without worrying about mishaps.
Bridging Traditional and Contemporary Practices
Amidst these challenges, the evolution of silver casting practices continues, blending traditional methods with contemporary innovations. This is where staying relevant and current becomes crucial for artisans.
Keeping Skills Relevant
The skillset of a silver caster is like fine wine; it needs to be nurtured and refined over time. Keeping skills relevant demands curiosity and ongoing education. Whether it's attending workshops or immersing oneself in online forums for insights, continual learning is invaluable. One unique feature of staying in touch with modern techniques is the enhancement of adaptability in designs. This allows artisans to produce pieces that resonate with modern consumers while still maintaining a nod to tradition.
Adapting to Technological Advancements
Technology can be both a friend and an enemy in artisans' journeys. Embracing new tools and techniques, like 3D printing, offers a new frontier. However, one can argue that straying too far from traditional methods could lose the essence of craftsmanship. Yet this balance creates opportunities—integrating computer-aided design fosters creativity while streamlining the production process.
Balancing Artistry with Productivity
Artistry versus productivity is a classic tug-of-war. On one hand, there’s the desire to create unique, one-of-a-kind pieces. On the other hand, time is money, and demanding schedules often push artisans toward mass production. The unique aspect here is discovering how to blend both worlds—producing high-quality pieces that can keep pace with market needs, without overly compromising on artistry.
An artisan who successfully manages this intersection will not only thrive but also contribute to an evolving market that appreciates the value of both handcrafted and efficiently produced items.
The Future of Silver Casting Jewellery
The landscape of silver casting jewellery is on the brink of transformation. With ongoing technological advancements and a growing emphasis on sustainability, the future holds a promise of innovation. As the world continues to evolve, so does the craftsmanship involved in jewellery making. This section will explore the emerging trends and market dynamics shaping the future of silver casting, underscoring its significance in the broader context of jewellery design and craftsmanship.
Emerging Trends
Impact of Digital Technology
Digital technology has seeped into every nook and cranny of our lives, and jewellery making is no exception. In the realm of silver casting, tools such as 3D printing and computer-aided design (CAD) are game changers. The adoption of these technologies allows jewellery designers to conceptualize and produce intricate designs with striking precision. This aspect of digital technology means efficiency, as designers can tweak their creations without the usual back-and-forth of traditional methods.
Furthermore, the key characteristic of this trend lies in the accessibility it offers. Now, even small artisans can produce high-quality pieces without investing heavily in physical molds. However, one might argue that this level of accessibility could dilute craftsmanship. Digital shortcuts can sometimes lead to a loss of the unique human touch that bespoke jewellery embodies, raising an interesting debate within the crafting community.
Growth of Sustainable Materials
As climate change continues to dominate discussions around consumer behaviour, the demand for eco-friendly materials in jewellery manufacturing is growing exponentially. Sustainable materials, such as recycled silver or ethically sourced alternatives, not only appeal to environmentally conscious consumers but also provide a unique selling proposition for jewelers.
The key characteristic of sustainable materials is their ability to align with modern values. This responsiveness to market demands makes them a popular choice for contemporary artisans, as they can tap into this conscious consumer base.
However, the integration of such materials isn't without its challenges. Sourcing sustainable supplies can sometimes drive costs up, which is a consideration for smaller-scale artisans trying to balance quality with affordability. Yet, the long-term benefits, such as customer loyalty and brand reputation, often outweigh these initial hurdles.
Incorporation of Mixed Media
The traditional notion of silver casting is evolving with the incorporation of mixed media. Today’s artisans are experimenting with combining silver with various materials – from wood to textiles and even plastic. This approach not only adds layers of texture but also opens up new creative avenues that can resonate with diverse audiences.
The key characteristic of incorporating mixed media is its flexibility; artists can express their individuality in ways that were previously difficult to achieve with silver alone. For instance, adding gemstones or unconventional materials can create unique, statement pieces that captivate potential buyers.
However, designers must find a balance in their creations. Using too many materials can lead to visual clutter, which detracts from the elegance that silver inherently possesses. Maintaining coherence in design remains a fundamental challenge.
Market Dynamics
Cost Analysis and Consumer Demand
The relationship between cost and consumer demand is intricate and sometimes unpredictable, especially in the realm of silver casting. As consumers become savvier, they are not just driven by aesthetics but also by value. Price analysis may reveal trends where customers are willing to invest in quality but expect transparency about sourcing and manufacturing processes.
The key characteristic of this trend lies in the adjustments that manufacturers must make. Brands that emphasize quality and ethical practices can command higher prices, paving the way for a more educated consumer base and ultimately enhancing market dynamics.
Challenges from Alternative Materials
Not all materials behave like silver, and the rise of alternatives such as stainless steel and synthetic materials poses a genuine threat. These materials often appeal due to their lower price points and durability, making them attractive to budget-conscious consumers.
The likelihood of alternative materials gaining traction can jeopardize the traditional silver jewellery sector. While these alternatives can mimic aspects of silver, they might lack the warmth and character inherent in genuine silver pieces. This presents a unique challenge for artisans to differentiate their products by emphasizing the superior qualities of silver.
Navigating Economic Fluctuations
With economic climates swinging like a pendulum, the silver casting jewellery market must adapt swiftly. Variations in silver prices can directly affect profitability, leading makers to adjust pricing strategies frequently.
One major aspect of navigating these fluctuations is scenario planning. Artisans need to stay informed and agile, harnessing data to anticipate market shifts. This proactive approach enables them to protect their businesses against unforeseen downturns, ensuring their creations remain viable in the marketplace.